5-Achsen-KMG-Prüfung bringt die „Guten Zeiten ins Rollen“
Messtaster zum Scannen ermöglichen eine schnelle Formdatenerfassung. Die Feedback-Übermittlung an die Bearbeitungszellen, begrenzen die Anzahl benötigter KMG-Spannmittel und reduzieren die Messtaster-Kalibrierzeit von Stunden auf Minuten bei Kawasaki in Maryville, USA. Erhöhter Messdurchsatz und mehr Flexibilität ermöglichen ein schnelleres Feedback an die Fertigungs- und F&E-Abteilungen; Scanning-KMGs könnten letztendlich zur Eliminierung von Prüfsystemen für Zahnräder und Nockenhübe führen.
Kawasaki lockt Motorradliebhaber mit dem Motto „die guten Zeiten rollen zu lassen“, aber im Kawasaki-Werk für kleine Motorenteile in Maryville, USA, rollen gute Zeiten einer ganz anderen Art an: Hier reduzieren zwei 5-Achsen-Scansysteme die KMG-Prüf- und Messtaster-Kalibrierzeit drastisch und beschleunigen außerdem das QS-Feedback zur Bearbeitung von kleinen Maschinenkomponenten. Die 5-Achsen REVO® Systeme von Renishaw sind auf Mitutoyo Crysta-Apex 121210 KMGs installiert und ersetzen zwei PH10 Dreh-/Schwenkköpfe, die mit SP25M Scanning-Messtastern auf herkömmlichen 3-Achsen KMGs verwendet wurden. Die mit REVO ausgestatteten KMGs haben die Prüfzeiten von scanintensiven Anwendungen auf die Hälfte oder weniger reduziert, kundenspezifische Messtasterkonfigurationen praktisch überflüssig gemacht, die Messtaster-Kalibrierzeit von sechs bis sieben Stunden auf etwa 45 Minuten reduziert und ermöglichen die Erfassung großer Mengen an Formmessdaten, was zu einer verbesserten Teilequalität führt. Ganz maßgeblich haben die REVO-Systeme den Messdurchsatz, die Datenqualität sowie die Flexibilität der QS-Abteilung deutlich erhöht und ihren Wert als strategische Unterstützung für sowohl die Fertigung als auch F&E gesteigert.
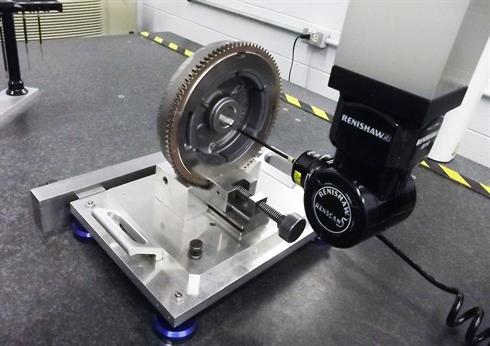
Das Kawasaki Produktionssystem
Das über 70.000 qm große Kawasaki-Werk in Maryville öffnete 1989 seine Tore und stellt luft- und wassergekühlte Ein- und Zweizylinder-Motoren mit 1.000 cm³ und kleiner her – für Hersteller von Rasenmähern für Geschäfts- und Privatkunden sowie für ein Schwesterwerk, in dem ATVs und Mule™ Nutzfahrzeuge hergestellt werden. Der Tätigkeitsbereich in Maryville umfasst u. a. Aluminium-Druckgießen, Kunststoff-Spritzgießen, umfangreiche maschinelle Bearbeitung, Lackierung und Montage. Alle Motoren – ca. 500.000 pro Jahr – werden vor dem Versand getestet.
„Wir verwenden das Kawasaki Produktionssystem (KPS),“ erklärt JC Watts, Technischer Leiter Qualitätssicherung der Kawasaki-Gruppe in Maryville. „Unsere Anforderungen in Bezug auf Qualität und Verarbeitung sind mit den besten der Automobilindustrie vergleichbar, wenngleich sich unsere Produktion auf kleinere Stückzahlen und viele verschiedene Produkte konzentriert.“ Das Werk hat 50 Fertigungslinien, die typischerweise als U-förmige Zellen aufgestellt sind, wobei sich die Eingangs- und Ausgangsmaschinen gegenüberstehen. „Es handelt sich praktisch um eine einteilige Produktion, bei der die Fertigungslinien ein Werkstück in hohem Tempo durch mehrere Prozesse führen“, erklärt Watts. Kawasaki nutzt die Automatisierungstechnik, durch die Integration von Kawasaki-Robotern, in vielen Druckguss- und einigen Verarbeitungsverfahren. Auf einer der Kurbelgehäuse-Produktionslinien laden Roboter das Rohmaterial und entladen die fertigen Teile, die dann gelagert und für die Montage verwendet werden können. Werkstücke werden u.a. aus Aluminium, Gusseisen und Stahl gefertigt.
„Unsere Toleranzen ähneln denen von Kraftfahrzeugantrieben für High-End-Produkte und unsere Aluminiumteile durchlaufen etwa vier oder fünf kritische Prozesse, die Stahlteile dagegen bis 15“, fügt Watts hinzu. Formtoleranzen im einstelligen Mikrometerbereich und Lagetoleranzen von 0,05 mm sind nicht ungewöhnlich.
Die Qualitätssicherung ist für die Prüfung von 125 verschiedenen Massenteilen sowie für Zulieferteile und die für die Entwicklung hergestellten Teile zuständig. Die Umgebungsbedingungen im Messlabor, das sich neben den Fertigungslinien befindet, sind kontrolliert; Werkstücke werden zu Routineprüfungen auf Wagen bzw. über Züge (elektrische Fahrzeuge, die verschiedene Transportwagen ziehen) ins Messlabor befördert. Kritische Komponenten werden zum Teil persönlich in die QS gebracht, damit eine Prioritätsprüfung, während einer Linienumrüstung oder falls ein Bediener ein Problem vermutet, unternommen werden kann.
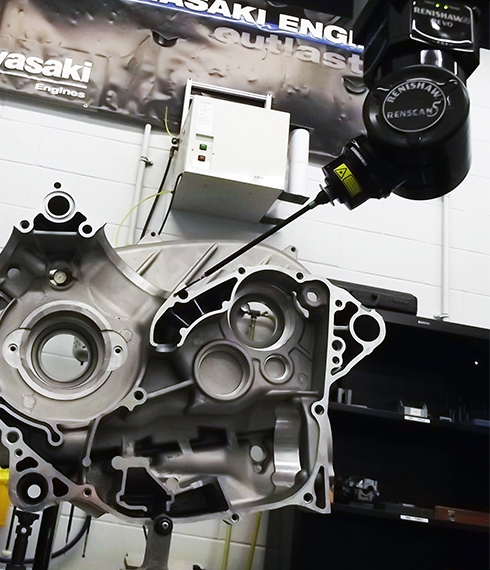
Vorteile des 5-Achsen Scannens
„Als ich hier anfing, hatten wir ein paar 3-Achsen-KMGs mit PH10 Dreh-/Schwenkköpfen und SP25 Messtastern sowie ein weiteres KMG mit einem festen Tastkopf“, erklärt Watts. „Es war frustrierend, dass wir Messtasterkonfigurationen erstellen mussten und selbst mit den Dreh-/Schwenkköpfen an die Grenzen der Machbarkeit gestoßen sind. Wir hatten so viele verschiedene Tasterkonfigurationen, dass die Kalibrierzeiten von sechs bis sieben Stunden unseren Messdurchsatz erheblich verringerten. Wir wollten besser sein als der von der Industrie als normal geltende Standard und haben uns deshalb verschiedene Optionen angeschaut; das 5-Achsen REVO-System schien die schnellste und flexibelste Alternative zu sein. Es passte am besten zu unseren Anforderungen.“
Kawasaki erwarb 2009 eine neue Mitutoyo Crysta-Apex 121210, bei der das REVO-System schon vorinstalliert war, und rüstete 2010 eine identische Maschine nach, nachdem die erste Maschine mit allen Teileprogrammen in Betrieb genommen war.
Der REVO 5-Achsen Scanning-Messkopf kann bis zu 6.000 Datenpunkte pro Sekunde erfassen. Er wurde für Hochgeschwindigkeits-Präzisionsmessungen von Freiformflächen und komplexen Geometrien, die eine großvolumige Datenerfassung zur Validierung von Sitz und Form mit höchster Genauigkeit benötigen, konzipiert. Es verwendet zwei Drehachsen, eine in der vertikalen und eine in der horizontalen Ebene, für unbegrenzte Rotations- und Positioniermöglichkeiten. Die 5-Achsen-Software steuert den Messkopf und synchronisiert seine Bewegungen mit den Linearachsen des KMGs. Look-Ahead-Algorithmen steuern den Messtasterweg und das KMG in einer koordinierten kontinuierlichen Bewegung. Der Kopf passt seine Position während der Messbewegung an und hält selbst bei einem Konturwechsel und Scangeschwindigkeiten bis zu 500 mm/s die Tastspitze in Kontakt.
„Obwohl wir unsere SP25 Scanning-Messtaster verwendeten, führten wir dennoch zu 95% berührend schaltende Messungen durch, da das Scannen mit einem 3-Achsen-KMG zu langsam war“, so Watts. „An unseren Zylinder- und Kurbelwellenbohrungen erkennt man wahrscheinlich am besten, dass berührend schaltendes Messen unzureichend war. Zur Erfassung einer ausreichenden Anzahl an Datenpunkten, um die Geometrie einer Bohrung mit einem Durchmesser von 80 bis 100 mm und einer Länge von 150 mm zu messen, brauchte der SP25 Taster so lange, dass wir die Messungen nur bei Maschineneinstellungen und auf Anfrage unserer Konstruktionsabteilung durchführten. Jetzt macht REVO bei jedem Kurbelgehäuse, das wir messen, eine Spiralabtastung und das System gibt die Werte an die Software weiter. Wir speichern außerdem ein Diagramm der Datenpunkte in unserem Netzwerk, wo es allen Mitarbeitern der QS, Konstruktion und Fertigung zugänglich ist und zur Lösung von Problemen beiträgt. Man kann sich das Problem VERANSCHAULICHEN. Was mit einem SP25 drei bis vier Minuten dauern würde, messen wir mit REVO in zehn Sekunden.“ Die REVO Messköpfe haben den Bedarf am berührend schaltenden Messen praktisch eliminiert. 95% der Prüfungen verwenden jetzt die Scantechnologie – ohne die bisherigen Zeitverluste, wodurch Kawasaki eine so große Menge an Daten erfassen kann, dass die Computer, die die Analysen durchführen, geschwindigkeitstechnisch herausgefordert werden. Der REVO Taster kann auch ‚Head Touch‘-Messungen ausführen und bei Bedarf für herkömmliche, taktil schaltende Messungen eingesetzt werden.
„Bei scannenden Messungen haben unsere Fertigungs- und Konstruktionsmitarbeiter viel mehr Vertrauen in die Richtigkeit der Werte“, fügt Watts hinzu. „Es kann leicht passieren, dass ein winziger Schmutzpartikel bei berührend schaltenden Messungen eine Unrundheit angibt, wenn nur sieben oder acht Punkte erfasst werden. Die Lage dieses Kreises kann schnell falsch sein. Wir haben Praxisbeispiele dokumentiert, bei denen flache Stellen erkannt wurden, die während berührend schaltenden Messungen nicht erkannt und Geometrien von Zylinderbohrungen, die taktil aufgrund der Menge der erfassten Daten mit diesem Verfahren, nicht entdeckt worden wären. Diese Probleme wurden noch vor Versand erkannt, aber die Werkstücke waren Ausschuss. Die Scanfähigkeit von REVO ermöglicht es uns, Formfehler sehr viel schneller und ohne Zeitverlust bei unseren Messungen zu erkennen. Dank REVO arbeiten wir sicherlich proaktiver und erkennen Qualitätsprobleme frühzeitig.“
Die Scanfähigkeit von REVO ermöglicht es uns, Formfehler sehr viel schneller und ohne Zeitverlust bei unseren Messungen zu erkennen. Dadurch sind wir in der frühzeitigen Erkennung von Qualitätsproblemen definitiv proaktiver geworden.
Kawasaki (USA)
Weniger Messtasterkonfigurationen, mehr Flexibilität
Mit REVO hat die Produktion in Maryville nun zwei Messtasterkonfigurationen, mit denen alle Massenbauteile gemessen werden können und die kundenspezifischen Taster werden in einem Wechselmagazin für Sonderanwendungen freigehalten. Sonderkonfigurationen für Zulieferteile wurden ebenfalls eliminiert, da die unbegrenzten REVO Positionierwinkel das Messen eines Werkstückes ohne besondere Aufspannungen bzw. Überlegungen in Bezug auf die Tasterwahl ermöglichen. Dank der niedrigen Anzahl an Messtastern hat sich die Kalibrierzeit auf rund 46 Minuten verkürzt. Jetzt überwachen die QS-Fachkräfte die Kalibrierung anstelle jeden Wechsel zu kalibrieren.
„Wir können jetzt alle unsere Massenbauteile mit nur zwei Tasterkonfigurationen messen“, erklärt Watts. „Aufgrund des großen Anfahrwinkels, den REVO zwischen Taster und Werkstück erzeugt, war es uns möglich, die Tasterkonfigurationen mit der großen Antastkugel zu streichen. Während des Scannens hält REVO den Anfahrwinkel und ermöglicht so die Messungen großer zylindrischer Merkmale, wie z. B. einer Zylinderbohrung, mit demselben Taster, der auch zur Messung einer 5 mm Bohrung verwendet wird, ohne den Tasterschaft anzustoßen.“
Die Flexibilität des REVO Systems hat sich außerdem als Zeitersparnis für Kawasaki herausgestellt. „Wir können alle Teile auf beiden Maschinen mit einer begrenzten Anzahl an Spannvorrichtungen und ohne besondere Kalibrierungen messen“, so Watts. „Wir messen alle unsere Teile auf drei verschiedenen Spannmitteltypen. Nach der ersten Ausrichtung richtet sich der REVO Taster selbst am Werkstück aus. Die Verwendung von Sonderspannvorrichtungen fällt fast vollständig weg, ohne dabei Messfehler aufgrund von Teileausrichtungen befürchten zu müssen.“
Kawasaki programmiert alle Messroutinen betriebsintern unter Verwendung der Mitutoyo Mcosmos 3.1 Software. Die Aufrüstung auf das REVO System regte eine Verlagerung zur parameterorientierten und modularen Programmierung der Messroutinen durch eine interne Kodierungsentwicklung an. Hierdurch ist es nun möglich, ein Programm für eine ganze Teilefamilie zu verwenden. „Wir haben zum Beispiel 30 verschiedene Kurbelwellen, aber da jede dieselben Merkmale besitzt, nur in einer anderen Größe oder Position, können wir mit demselben Messprogramm alle Teile messen“, erklärt Watts. „Das ist einer der großen Vorteile, die wir gewonnen haben.“ Die unendlichen Winkel des REVO Systems vereinfachen die Erstellung von Parameter-Programmen, da der Taster das Werkstückmerkmal, aufgrund dessen Größe oder Ausrichtung, nicht störend beeinflussen kann. Der Taster richtet sich automatisch normal zu dem zu messenden Merkmal aus und vereinfacht so die Programmierung.
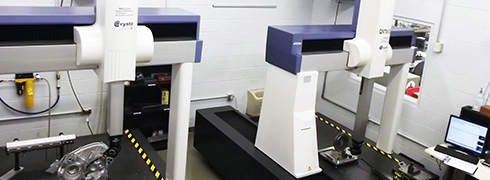
Schnellere Messung, bessere Daten von QS an F&E
Watts erklärt, dass der Wechsel von der 3-Achsen auf die 5-Achsen-Programmierung nicht schwierig ist und dass ein Programmierer mit begrenzter Qualifikation REVO Messungen weiterhin als 3-Achsen programmieren kann. Bei der Optimierung der Messgeschwindigkeit ist es jedoch entscheidend, dass so viele Messkopfbewegungen wie möglich eingesetzt werden. „So können Werkstücke am schnellsten gescannt werden, ohne dabei Messfehler zu verursachen“, fügt er hinzu. „REVO eröffnet viele neue Möglichkeiten mit nur wenigen Einschränkungen, d. h. höher und auch geringer qualifizierte Programmierer profitieren von einer schnelleren Geschwindigkeit.“
Die Prüfergebnisse können manuell an die Fertigungslinie übergeben werden und der Bediener hat außerdem über ein Computernetzwerk direkten Zugriff auf die Ergebnisse. „Einige unserer Prüfberichte liefern Versatzwerte direkt zurück zum Koordinatensystem der Bearbeitungszentren; dies ermöglicht es dem CNC-Bediener die Offsetkorrektur direkt vom Bericht abzulesen, wodurch Fehlinterpretationen in Bezug auf die vom Bediener einzugebenden Werte verhindert werden“, so Watts weiter. „Wir machen uns einige der Best-Fit-Algorithmen zunutze und arbeiten mit unseren Produktionstechnikern, besonders bei Teilen, die komplexere Algorithmen benötigen, um die richtigen Änderungen vorzunehmen und um verschiedene Prozessanpassungen gleichzeitig einzusetzen. Bevor wir das REVO Messsystem hatten, war dies nur schwer durchführbar; dank REVO können wir Parameter-Programmierung verwenden und dadurch unsere Leistungsfähigkeit einfacher ausbauen.”
Das 5-Achsen KMG-Scannen hat sich laut Watts als kleine Revolution für die Qualitätssicherung in Maryville, in Bezug auf Geschwindigkeit, Datenqualität und Messdurchsatz, herausgestellt. "Wir profitieren stark davon, zwei Maschinen zu besitzen, die komplett austauschbar sind, d.h., wenn eine Maschine defekt ist oder gerade kalibriert wird, können wir kritische Teile auf der anderen messen. Dies hat sich in der QS als riesen Vorteil erwiesen, da wir im Notfall das große Werkstück auf das kleine KMG spannen mussten oder das Teil, das den Taster mit dem ungewöhnlichen Winkel benötigte, auf die Maschine, die nicht dafür ausgestattet war. Wir erhielten Anfragen aus der F&E-Abteilung, bestimmte Geometrien zu messen, was in der angegebenen Zeit eigentlich unmöglich war. Jetzt können wir die Daten viel schneller liefern und, da es sich um gescannte Daten handelt, haben unsere Kollegen auch mehr Vertrauen in sie. Die neue Flexibilität, weniger Spannmittel, Formmessungen, die Parameter-Programmierung - das sind alles zusätzliche Vorteile zu der herausragenden Messgeschwindigkeit."
Im Maryville-Werk wurden über 50.000 Teile mit den zwei mit REVO ausgestatteten KMGs gemessen und Watts hat angedeutet, dass das REVO System in Zukunft vielleicht auch zur Zahnradprüfung und für die Nockenwellen eingesetzt wird, sofern dies durchführbar ist. "Wir haben unseren eigenen Algorithmus und unser eigenes Unterprogramm in unserer Software für den Nockenhub entwickelt, was ohne das REVO System, aufgrund des zur Messung notwendigen Winkels, den der Messtaster für den Hub an den Nocken benötigt, viel schwieriger gewesen wäre."