Ducati při výrobě unikátních vačkových hřídelí spoléhá na detekci poškození nástroje.
Firma Ducati si uvědomuje, že obrábění drahých komponent pro její motory s ventilovým rozvodem Desmodromic musí být pečlivě kontrolováno. Různé nástroje jsou během roku použity stotisíckrát, což představuje stálé riziko, že ze zásobníku bude vysunut vyštípnutý nebo zlomený nástroj a způsobí vážné problémy. Tento problém byl vyřešen pomocí systému detekce poškození nástroje na základě moderní bezkontaktní laserové technologie.
Nejdůležitější fáze výroby vačkové hřídele Desmodromic ve firmě Ducati se odehrává na dvou obráběcích centrech Stama. Stroje vyrábějící vačkové hřídele pro všechny různé motory Ducati pracují nepřetržitě celý rok.
Fulvio Abbondi, specialista firmy Ducati Motor na výrobní technologii poznamenává: „Při výrobě hřídele, která probíhá kompletně v naší továrně, je v průběhu náročného výrobního procesu požadována vysoká přesnost. Jedná se o velmi drahou součástku. Je vyráběna ze speciální slitiny a je drahá již v okamžiku, kdy je jako polotovar upnuta do obráběcího centra po prvním hrubém soustružení.“
Poškození nástroje během výroby vačkové hřídele by bylo velmi vážnou událostí a mohlo by způsobit vznik zmetku, nákladné opakované obrábění a ztrátu času. Mohlo by také dojít k poškození vřetena stroje, což při připočtení nákladů na vlastní speciální nástroje představuje částku v tisících Eur.
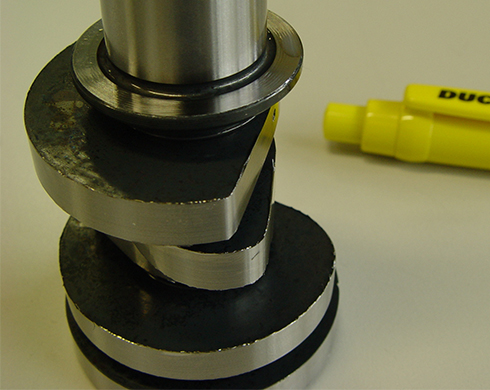
Kontrola
Abbondi se zmiňuje o roli, kterou hraje detekce poškozeného nástroje. „Je velmi důležité, aby kontrola nástrojů byla prováděna v průběhu obrábění. Systémy Renishaw NC4 byly instalovány na dvou obráběcích centrech: ihned po vložení nástroje do vřetena stroje protíná nástroj v definované poloze paprsek sondy. Je-li řezné ostří poškozeno, například je dlouhé 97 mm namísto 100 mm, laserová sonda spustí alarm. Samozřejmě, že každý nástroj má jinou délku, průměr, apod. Systém s tím počítá a rozlišuje mezi poškozenými a nepoškozenými nástroji.“
Pan Abbondi pokračuje: „NC4 nám rovněž umožňuje kontrolovat poškození malých nástrojů použitých k výrobě čepů a jiných referenčních míst na vačce, které jsou rozhodující pro řádný chod motoru. Kdyby nebylo systému Renishaw, stroj by například mohl pracovat se zlomeným břitem, což by vedlo ke katastrofálním výsledkům. Protože využíváme funkci automatické detekce poškození nástrojů, jeden operátor může jednoduše obsluhovat dva stroje. Vše, co musí udělat, je upnout obrobky a kontrolovat, zda vše běží plynule.“
Kontrola procesu je pro obrábění rozhodující
Pan Abbondi popisuje: „Nejprve jsme nainstalovali systém dodaný výrobcem obráběcího stroje, který umožňuje kontrolu výkonu motoru vřetena. Tento systém kontroluje stupeň opotřebení větších vrtáků použitých k vrtání nejhlubších děr, ve kterých je řezný odpor v průběhu obrábění více patrný. Jestliže vzroste kroutící moment, znamená to, že nástroj je opotřebený a je spuštěna výstražná signalizace. My ale také potřebujeme rychle a spolehlivě zjišťovat poškození i těch nejmenších nástrojů, které zpravidla unikne většině detekčních systémů.“
Běžné kontaktní detekční systémy mají určitá slabá místa a jsou obvykle nevhodné pro malé nástroje – nástroj přichází do styku s „tlačítkem“ nebo „tyčkou“, které aktivují zařízení. Existuje také nebezpečí, že nástroj se zlomí nebo poškodí při samotném měření. To znamená, že lze pracovat jen při nízkých otáčkách, což zpomaluje výrobní proces a značně prodlužuje doby cyklů. Systémy musí být často namontovány uvnitř pracovního prostoru, kde zabírají drahocenné místo a mohou být poškozeny. Proto byl systém Renishaw zaveden jako náhrada za tato zařízení.
Kontrola světlem
Vynálezy v laserové technologii vedly k vyvinutí bezkontaktních detekčních systémů, schopných bezpečně měřit i menší nástroje. Laserový paprsek probíhá mezi vysílačem a přijímačem, upevněnými na stole stroje napříč pracovním prostorem. Jakmile nástroj protne dráhu paprsku, množství světla zjištěného přijímačem se sníží a tím je indikována přítomnost nástroje. Není-li zjištěno snížení množství světla, systém vyšle signál upozorňující na poškozený nástroj.
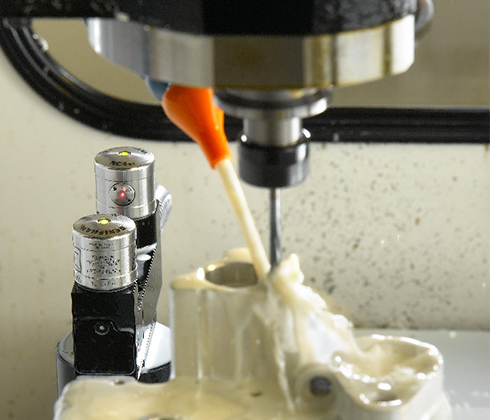
Systém Desmodromic
Naprostá většina světových výrobců motorů používá ve svých motorech vratné pružiny k uzavření ventilů (výfukových a sacích). Tyto pružiny táhnou ventil zpět do výchozí polohy po ukončení operace. Jedinou výjimkou je firma Ducati, která dosáhla značných výhod díky použití méně obvyklého systému Desmodromic. Rozvod Desmodromic přináší větší spolehlivost motoru při vysokých otáčkách tím, že řeší problém setrvačnosti pružiny a snižuje provozní tření asi o 30 %. Teoreticky může motor snadno dosáhnout až 20 000 ot/min.
Desmodromický rozvod využívá k uzavření ventilů mechanický systém, jehož koncepce byla vyvinuta v Americe. Byla však opuštěna vzhledem k nadměrným výrobním nákladům. Slavný boloňský výrobce byl však jiného názoru a v roce 1972 zabudoval rozvod Desmodromic do svých dvouválcových motorů a již desetiletí používá tento výjimečný prvek. Ventily místo jednoduché pružiny uzavírá speciální vačka. V každém případě vzniká úzká vazba mezi ventilem a jeho polohou - termín „desmodromic“ pochází z řeckého „desmòs“, což znamená „vazba“.
Systém Desmodromic přináší závažné komplikace do konstrukce a výroby komponentů, jako jsou vačkové hřídele. Vačka samotná nemá jednoduchý tvar běžné vačky. Je tvořena speciálními zvedacími šikmými plochami. Konstrukční tým firmy Ducati pečlivě navrhl vačku tak, aby bylo dosaženo požadovaného zrychlení a otáček. Přesnost je všechno: vůle mezi dříkem a vačkou je seřízena manuálně během montáže a jedná se o zásadní operaci. Jak Abbondi říká: „Není možné natahovat časovou toleranci, jak to lze dělat u automobilů s hydraulickým nastavování vůle zdvihátek ventilů. Používáme jednu podložku dole a jednu nahoře. Podložky musí být seřízeny s extrémní přesností.“