Smart manufacturing data platform for industrial process control
Renishaw Central is a smart manufacturing data platform that collects, presents, and actions accurate process and metrology data. Discover how Renishaw Central can help you optimise your manufacturing processes.
Unlock the power of
data-driven manufacturing
Today, factories are collecting and processing more data than ever before. But only those with access to the right data, at the right time, can take real advantages of the smart factory.
Renishaw Central is a manufacturing data platform that collects and presents process and metrology data from the shop floor. It connects to measurement devices across the manufacturing process and provides invaluable insights. Manufacturers can use these insights to analyse, identify, predict, and correct process errors before they occur.
The result is a highly efficient and productive factory, with optimised processes, reduced downtime and minimised waste, thereby reducing costs.
The benefits of a connected machine shop
On a connected shop floor, machines and systems communicate with each other by sharing data and trends. Real-time monitoring enables manufacturers to make informed decisions and have complete control of their end-to-end manufacturing.
Renishaw Central can connect to multiple devices (from Renishaw and other suppliers) across multiple factories, enabling you to:
- Collect and store end-to-end process and metrology data.
- Build controlled processes to enable automation and boost throughput.
- Identify, predict, and correct process errors before they happen.
- Enhance decision making for process improvements.
- Increase operational efficiency and reduce human intervention.
Unlock the power of your data with Renishaw Central
How does it work?
Renishaw Central collects metrology, status, and alarm data from connected devices across the shop floor. Devices include additive manufacturing (AM) systems, on-machine measurements systems, shop floor gauging, and co-ordinate measuring machines (CMMs). With insight into the process performance of each workstation, manufacturers have a better understanding of where to take action.
In unattended processes, the status of devices can be monitored remotely. If any errors occur, they will be detected and displayed within the Renishaw Central platform's dashboards or other third party applications. As a result, an appropriate operator can be deployed to resolve the fault.
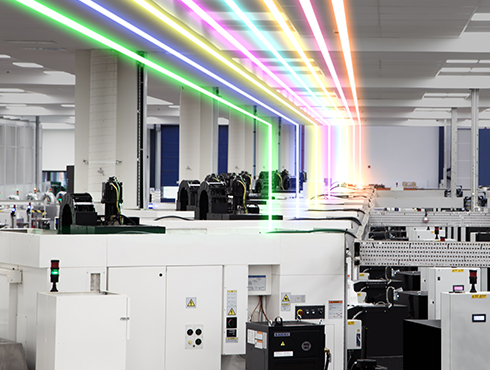
When coupled with Renishaw's intelligent process control (IPC) module, Renishaw Central can process metrology data and automatically update machine tool variables. Enabling truly automated, closed-loop process control.
The platform operates on-premises, giving you fast and robust process control feedback. This allows your administrators to own your data collection and ensure your process control is not dependent on internet connections.
Live data can be displayed, sorted, filtered, and analysed within the easy-to-use dashboards.
For more information on Renishaw Central dashboards, download our comprehensive brochure at the bottom of the page.
Features:
Renishaw Central gives you the confidence to implement automation, modernise your processes and take your decision making to the next level via actionable data.
- Easy-to-use dashboards which can be monitored from a central location.
- Connect to a single, or to multiple, connected machines across numerous facilities.
- Designed to connect to devices from Renishaw and other suppliers.
- Automatically update machine tool variables.
- All data is sent securely to a central on-premises store, providing an archive for traceability.
- The platform can also benefit from integration with industry-leading tools which support APIs, such as Microsoft© Power BI.
Connectivity, consistency and control drives confidence; Renishaw Central enables users to exploit digital twin and future factory concepts.
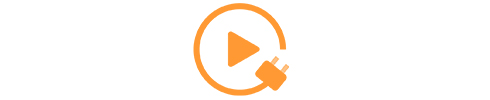
Connectivity
Connect multiple machines and devices to automatically detect which machines are running and determine why idle machines have stopped.
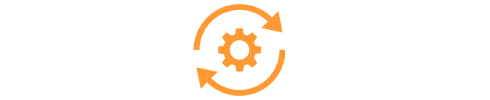
Consistency
Collect metrology data from connected devices in a central location and increase quality throughout the entire manufacturing process.
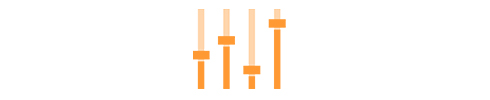
Control
Control process variables and gain operational knowledge over a period of time. With IPC, automatically calculate adjustments and update tool offsets or variables.
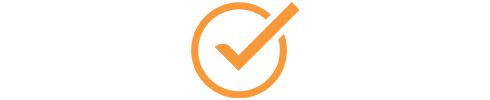
Confidence
Build confidence in your process and reap the benefits of true lights-out machining.
Explore how our powerful platform can enhance your manufacturing operations
Renishaw Central in action
Enable closed-loop process control on the shop floor
Renishaw Central collects measurement data from gauging systems, CMMs, or CNC machine tools. The platform can use this data to identify deviations and automatically send correction updates to the appropriate manufacturing machine. These updates may then be applied to the part being machined, leaving you confident in your automated, closed-loop production process.
Ensure part quality with final stage measurement data
Traditionally, metrology data from final inspection is locally stored. With Renishaw Central, all machines can be connected and data stored centrally, providing a factory wide view. This enables the identification of any parts close to exceeding tolerance. The platform can then automatically update the relevant CNC machine tool, applying corrections to the next part produced, maintaining part quality.
Renishaw Central boosts weekly machine availability by 79 hours
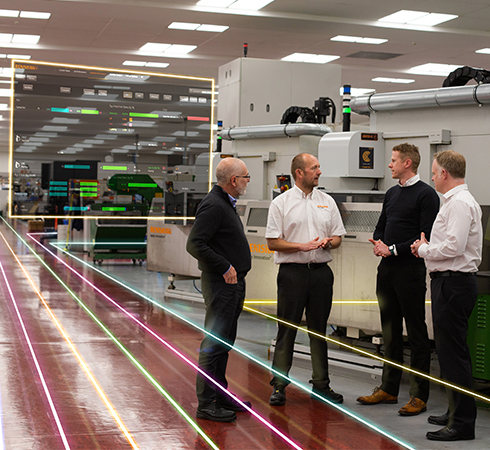
Our smart manufacturing platform is a prime example of our commitment to help manufacturers drive process improvements, enhance quality, and increase efficiency. And because we are so confident in its capabilities, we have implemented it into our own facilities.
“The scale of Renishaw Central's integration is impressive," explains David Miles, Manufacturing Engineering Manager, Renishaw plc. "We've connected the platform to 69 machines across our two main manufacturing sites in the UK. At our Miskin facility in South Wales 43 machines are loaded and run by just four staff per shift.
At this level of automation, CNC alarms and other unplanned stoppages have a significant effect. Renishaw Central has addressed this issue leading to unexpected efficiency gains.”
Since integrating the platform, we have found that two key issues are responsible for 82% of automation stoppages. By converting this actionable data into remedial actions, we have been able to increase weekly machine availability by 79 hours.
The early indications are positive. With the introduction of bespoke setting pieces and automated offset updates, we have achieved significant set time reductions. Critically, set-up has been de-skilled and can be reviewed and redone quickly, if necessary, which is increasingly important in a tightening labour market. At the same time, records of the updates made are available for traceability and ongoing data interrogation.
David Miles, Manufacturing Engineering Manager, Renishaw plc
Demonstrating over 50 years of innovation
As manufacturers ourselves, we understand the challenges faced in manufacturing.
- To be highly productive and flexible.
- To achieve more consistent capability.
- To increase levels of process automation.
- To reduce costs and be globally competitive.
We use our own products within our manufacturing operations to address common production challenges. Additionally, we apply our Productive Process Pyramid™ methodology. This enables highly productive and automated operations, by eliminating or controlling sources of variation, with minimal human intervention.
With this first-hand experience, we shape our innovations and product development into solutions we know our customers truly need.
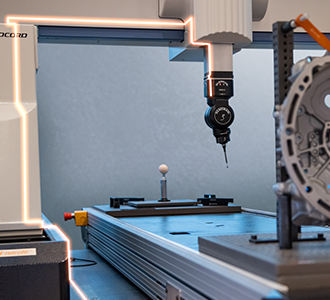
Supporting you in your digital transformation
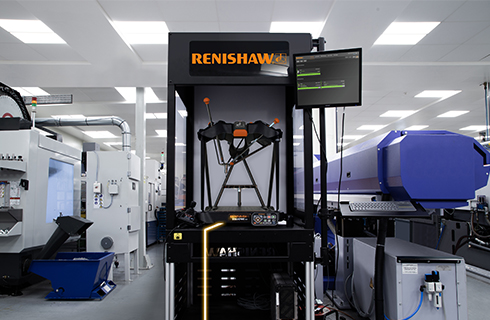
Digital transformation is accelerating. This is due to rapid progress in technologies such as artificial intelligence (AI) and the Industrial Internet of Things (IIoT). Technology advancements and plug-and-play options have made it simpler to link to manufacturing systems. However, the use of shop floor connectivity has not been as successful as anticipated. That's why Renishaw Central has been designed to easily connect to shop floor systems from a wide range of third party suppliers.
Today, smart thinking remains at the heart of our approach. We're not just a well-established manufacturer; we've also been practising smart manufacturing principles across five decades.
So, who better to partner with for expert guidance and support on the journey to your smarter factory?
Embrace closed-loop process control
with Renishaw Central
Frequently asked questions
Q: What is Renishaw Central?
Renishaw Central is a smart manufacturing data platform. It is designed to streamline manufacturing operations by connecting multiple machines, devices, and software systems. It provides real-time data insights, enabling manufacturers to make informed decisions to improve shop floor productivity and efficiency.
Q: What is the difference between physical factory automation and process automation?
Physical factory automation drives operational efficiency by increasing machine uptime and overall output, without adding extra manufacturing machines. The use of robots to load workpieces onto machining centres is an example of physical automation.
Our shop floor and on-machine measurement solutions for the automation of CNC machining processes allow you to increase machine utilisation and operate 24/7. With reliable process automation technologies in place, you can implement physical automation, which increases productivity and, in turn, can reduce waste and energy consumption.
Q: What are the benefits of smart data in manufacturing?
Smart data refers to data that has been transformed from meaningless numbers into actionable insights. Using smart data in manufacturing enhances decision making, leading to improved efficiency, better process control and predictive maintenance.