要成功加工純機械切削零件,需要具備哪些條件?
除設備加工能力之外,操作人員的經驗以及對整個工藝制程的設計也是影響生產效率的重要因素。
本文改編自《Modern Machine Shop》雜誌,已獲原刊編者正式授權
© 版權所有 Gardner Business Media, Inc.
如果採用鑄造方法加工零件,一般可以保證如期交付,但確實存在極少數延期交付的情形。R&D Manco 公司是位於美國亞利桑那州鳳凰城的一家機械加工分包商,為航太業的眾多知名客戶提供服務。它加工的零部件通過了相關標準的認證,包括飛機燃料和控制系統使用的高精密元件。零件從鑄件毛坯開始加工,一般總交貨週期為32周。但是,如果 R&D Manco 能夠從實心坯料塊直接切削出零件的精確形狀,從而完全避開鑄造工序,通常可以將客戶期望的整體交貨時間縮短 60% 以上,並且零件加工成本一般也會降低20%。因此,R&D Manco 制定了一項長期目標 — 並且十年如一日般地不懈努力 — 盡可能將更多的零件從鑄造加工過渡到純機械切削加工。
他們的努力也得到了客戶的支援與鼓勵。一家重要客戶在他們的一些加工合約中經常會附加一項要求,表示如果工廠有能力做到的話,可以自行選擇使用鑄造方法還是純機械切削方法生產零件。另一家同等規模的客戶甚至還擁有一個切削制程團隊,專門負責分析將鑄造加工轉換成純切削加工的可行性。然而,並不是所有零件都適合通過切削方法製造,比如某個交貨週期為一年的零件,由於其具有較深的凹陷形狀,而工廠(到目前為止)無法通過機械加工做出這種形狀,因此可能無法轉換成純切削方式。但是隨著時間的推移,R&D Manco 已經能夠將一半曾經需要鑄造加工的常見零件改造成純機械加工製造。
避開鑄造工序後,客戶的供應鏈得以進一步整合,工廠也可以承接供應鏈上的更多業務。
然而,隨著純切削加工趨勢日漸明顯,這種加工方法也受到更多其他因素影響,這與工廠越來越重視相關加工作業有關。工廠在決定採用純切削方法製造零件時不僅僅是增加銑削作業,避開鑄造工序後,客戶的供應鏈得以進一步整合,工廠也可以承接供應鏈上的更多業務。工廠在決定最終成本和零件交貨週期方面發揮著愈加重要的作用。它必須承受進一步縮減成本和縮短交貨週期帶來的全部壓力。簡而言之,採用純切削加工方法的工廠註定需要付出更多努力。
因此,除了機台的加工能力之外,R&D Manco 的生產方案中至少還有其他兩個也很重要的因素影響其在純切削加工方面取得持續成功。一個是操作人員,另一個是工藝制程。針對純切削加工,工廠致力於培養相應的企業文化和能力,以實現不斷提高金屬切削率的根本目標。
-
過去,這樣的零件會從毛坯鑄件開始加工。 如果 R&D Manco 能夠成功地將生產過程轉換為從實心坯料塊開始直接切削出零件,就一定可以為客戶縮減成本並縮短交貨週期。 但是,要做到這一點,他們註定要承受更大壓力,也必須付出更多努力。
-
純機械切削加工對R&D Manco最基本的能力要求是五軸加工技術。 R&D Manco擁有六台Haas Automation製造的五軸加工中心。
-
他們在純機械切削加工方面取得成功的秘訣中有一條不可或缺:鼓勵經驗豐富的機械工程師不斷改進和優化工藝製程 — 這已成為一種企業文化。
-
純機械切削加工會完全取代鑄造加工嗎?不會。有些零件仍然需要採用鑄造加工方法。就拿這個零件來說,機械切削加工無法製作出這種內部形狀。雖然R&D Manco可以將鑄造加工轉換成純切削加工並使客戶獲益,但是,對於許多加工任務來說,鑄造方法依然是最理想的選擇。
競爭文化
R&D Manco 擁有兩家毗鄰的工廠,總面積達3萬平方英尺,員工人數超過70人。這個不常見的名稱最初來自 Manco 和 R&D Specialty 兩家工廠的合併。這兩家工廠很早以前就已經合併了,但這個名稱卻保留至今,其中部分原因可能是仍有許多員工曾親歷了當時的過程。
「我們聘請了一些經驗極其豐富的機械工程師,」Bloom 先生說。經驗對於工廠成功發揮五軸加工的優勢非常重要。持續不斷地從鑄造加工轉換到純切削加工,這意味著工廠需要定期設定新的工藝制程,以突破原始設計,通過銑削製造出具有複雜、有機形狀的零件。在開發此類加工工藝時,幾乎總會出現理論設計與實踐經驗技能相交匯的一點。例如,在模擬加工中看似可行的五軸銑削迴圈在實際操作過程中可能會受到雜訊或精度超公差的困擾,這是因為工件位置設定不夠精確,導致刀具無法沿特定輪廓行走等等。在這種情況下,聽從經驗豐富的加工團隊成員的意見,通常可以找到最有效的方法來改進制程,從而以最好的方式解決問題。
公司管理層向生產人員明確指出,這種經驗判斷非常寶貴。事實上,不斷進行此類性質的制程改進意義重大。畢竟,針對一個零件換用純切削加工方式最重要的原因之一便是這種方式能夠不斷提高加工效率。為了促進實際生產經驗在不斷改進工藝制程方面發揮更大的作用(即提高金屬切削加工的速度和效率),工廠有意在員工當中培養一種競爭文化。實際上,這種文化發揮效果最明顯之處可能不是在五軸加工領域,而是工廠的50錐形主軸加工設備。在這一領域中,工廠投入使用了大型、重型的加工中心機,目的是最大限度地提高鋁材和鈦材切削加工過程中的金屬切削率。與其他領域一樣,工廠鼓勵該領域的機械工程師與程式設計人員一起合作探討更多切削路徑和切削刀具選項,以不斷改進制程工藝。50 錐形主軸設備加工的不同之處在於,機台的加工效率有時可能實現顯著提升,特別是加工鋁材時。比如一個被工程師昵稱為「三球」(因其形狀得名)的鋁制零件,在採納了員工在進給速度和切削深度方面提出的多項改進建議後,在第一個加工迴圈期間便可去除此工件幾乎 90% 的初始原料,而所需時間也從八個多小時縮短至兩小時四十三分鐘。而促使這些改進發生的驅動力則是為了超越自己以往的成績,甚至是(良性)超越他人。
當有人衝破束縛、成功創新時,我希望其他人也勇於效仿,敢於突破。
Bloom 先生(R&D Manco 公司)
當然,眾多工廠都對經驗豐富的機械工程師求賢若渴。但是,這些擁有寶貴經驗的人才已經越來越難找了。R&D Manco 也面臨同樣的挑戰。為了充實人才儲備,期待他們將來能夠運用不斷積累的豐富經驗做出貢獻,工廠根據美國模具與加工協會的培訓課程制定了一項學徒計畫,目前已有三名員工加入了該計畫,將來會有更多的員工加入。該計畫中有一個有意義的細節,即員工接受培訓的起步領域。在我們工廠,每位員工都是從工件檢測領域入門,Bloom 先生說。沒錯,我們的目標是要不斷縮短加工迴圈時間和交貨時間,為此我們還營造了競爭性的企業文化,目的就是鼓勵員工努力實現這一目標。但是,要實現目標,首先要充分理解目標,這一點更為重要。也就是說,R&D Manco 的每一名員工首先要瞭解合格零件的標準。
運用機台監控,把握制程能力
機台監控是 R&D Manco 公司取得成功的另一個重要因素。採集機台狀態基本資料,分析資料以診斷並糾正切削中斷的原因,這是工廠提高加工能力最重要的手段之一。工件切削與機台監控之間的關聯可能並非一目了然,但事實上,它們之間確實存在著直接的聯繫。這種聯繫可以歸結為一點:每當 R&D Manco 在某個零件的加工制程中避開鑄造工序時,就意味著突破了一個曾經阻礙零件製造效率的巨大瓶頸。然後工廠就可以將注意力轉向純切削加工過程中新出現的其他瓶頸。
實施機台監控的第一步是正視機台稼動率 — 這一數字一度低得令人失望。
R&D Manco 的許多機台都購自 Okuma。公司指出,這些機台是實施機台監控的寶貴物件;利用製造商基於 Windows 的控制器,系統能夠輕鬆地從機台收集即時狀態資訊。對於老式機台或製造商未提供此開放介面的機台,公司採用來自 Shop Floor Automations 公司的 MTConnect 轉換器對機台控制器進行了改造,以便將這些機台也納入整個工廠的機台監控系統之中。Predator 公司的軟體能夠整合這些機台資料,將其整理後輸出為圖形和報表,供工廠隨後進行分析。
實施機台監控的第一步是正視機台稼動率 — 這一數字一度低得令人失望,公司管理者表示。對於機台有效切削時長而言,幾乎所有工廠都犯了同樣的錯誤:他們主觀認定的時間都要比機台實際切削時間更長。不過,瞭解實際的機台稼動率會非常有幫助,即使這一數字可能令人失望,Beach 先生說道。首先,這個指標可以讓工廠瞭解自身實際加工能力。用於生產規劃的企業資源規劃 (Enterprise Resource Planning - ERP) 軟體不一定瞭解這一點,這就是為什麼即使已經在 ERP 中制定好生產計畫,零件還是會延遲交貨的原因。瞭解實際能力能夠讓工廠知道何時需要將業務外包出去,從而彌補工廠自身加工能力的不足。第二,瞭解實際稼動率能夠讓工廠看清改進的潛力空間,繼而著手努力挖掘這一潛力。
這項工作並不一定簡單,但我們也不會特意將其複雜化。Beach 先生說:「我們第一次開始實施機台監控時,各種各樣的識別代碼紛紛跳出來提示機台停機的原因。」電腦螢幕變成了一個五顏六色的調色板,顯示著(或者軟體認為識別出的)各種各樣機台停止切削的原因。「原因多到令人眼花繚亂,卻沒有太大的價值,」他說。他得到的機台未切削的分析資料並不能很好地解釋機台上實際發生的情況。相反,他意識到,實際上「未切削時間就是未切削時間,僅此而已」。在任何情況下,如果某種狀況發生過於頻繁,就應該找出原因並予以解決。如今,工廠的機台監控系統可以使用三種狀態而不是兩種狀態(切削和非切削)對所有機台的所有活動進行描述。其中一個導致生產延遲的原因經證明其影響頗為顯著,值得將其記錄下來並加以監控。
這個原因就是首件檢測。實例證明,首件檢測的等待時間是導致工廠生產中斷最重要的原因。這一發現可能是執行機台監控最早得到的主要成果之一。瞭解了問題所在之後,工廠採取了各種措施來解決問題。質檢室增加了一台三次元和一名技術人員,專門負責首件檢測。此外,R&D Manco 還在探索在工件無需離開機台的情況下執行首件檢測的可能性。借助 Renishaw 的 “Productivity+” 軟體,機台自身便可通過測頭對工件進行測量,並將測量值與原始 CAD 檔資料進行對比。部分工件種類已成功轉為以這種方式完成首件檢測,從而無須再將加工出的首個成品件送往質檢部進行檢測,因此完全避免了生產延遲。
機台監控實現的其他成果
Bloom 先生和 Beach 先生指出了工廠通過機台監控獲得的有關提高加工效率的其他各種發現,如果不是監控生成的資料令這些發現更為清晰明瞭,工廠管理層就不會這麼快掌握它們。R&D Manco 總結出的經驗如下:
- 臥式加工不僅適合某些工件類型,也是一些加工種類的理想之選。工廠於 2017 年安裝了一台配有六個交換工作盤的臥式加工中心,但是最初的稼動率並不十分理想。Bloom 先生認為,問題在於工廠主要考慮的是這台機台的加工能力。工廠將加工作業分配給這台臥式加工中心,看重的是它可以很好地利用四軸完成加工。在當時,這種做法固然很好,但僅考慮加工能力就會忽視這樣一個事實,即機台的生產效率實際上取決於操作人員當天可以設定的加工作業數量。對於臥式加工中心而言,最適合的加工作業就是那些因為加工的重複性特點而可以保留初始設定的工件。因此,一開始工廠在給機台分配工作時考慮的是加工能力,但現在會綜合考慮加工能力、訂單數量以及該作業是否是確保合約連貫執行所必需的關鍵部分等因素來合理安排機台的加工任務。
- 大型工件的搬運難題是制約生產效率提升的一大因素。例如在一個雙機台加工單元中,如果被車削的工件太大而無法實現人工搬運,那麼此時對加工性能進行數位化分析後,便會發現只需購買一套技術含量很低的硬體設備,便可大幅提升整體加工性能。當工廠發現將工件從該加工單元的一台機台搬運至另一台機台所需的時間甚至比預期還要長之後,他們為專門為這兩台機台服務的起重機安裝了一套龍門導軌,從而解決了這一效率問題。
- 關於七軸車削加工單元稼動率的問題,有一種說法是正確的。為了執行最複雜的車削作業,工廠建立了一個由三台七軸車削中心組成的車削加工單元。鑒於這些機台的加工自動化程度如此之高,只需一次銑削迴圈即可完成整個工件的加工,所以大多數人認為一名操作人員便足以管理所有這些機台的生產作業。然而有些人並不同意這種看法;工廠管理層中持不同意見的人認為,實際上由兩名操作人員負責該加工單元是較為合理的。這種爭論可能會無限期地持續下去,直到機台監控資料最後給出了定論。在該崗位配置兩名操作人員的做法是正確的。該加工單元的機台稼動率是工廠所有設備中最低的(它們的稼動率本來應該是最高的),而增加人手則大大提高了該單元的加工效率。
R&D Manco 現有一名員工專門負責總結更多此類生產經驗。其製造工程師 Luis Hernandez 被任命為公司持續改進團隊的負責人。透過上述的調查與分析得出的結論顯著提升了工廠設備的稼動率,由此產生的潛在回報無疑證明組建這個團隊是值得的。公司表示很需要像 Luis Hernandez 這樣的角色,因為導致某一發生生產中斷時刻的最根本原因並不總是那麼顯而易見,很可能是多個因素導致的結果。事實上,Hernandez 先生並不是孤軍奮戰。他的一部分工作是聽取他人的想法與意見,與團隊成員深入探討有關機台加工中斷的問題,以便找出可能的原因和解決方案。他說:「我過去主要與工程技術部門溝通,現在我更多的是與車間領班們交流。下一步我將與機械工程師討論資料,希望確定造成他們加工延遲原因。」
Bloom 先生最後指出,這種分析資料和改進效率的做法同樣適用於生產車間以外的場合。他說,這種做法也適用於辦公室工作,例如向客戶報告生產計畫。甚至早在實施機台監控之前,公司就已經意識到,必須從「我們事先報告的情況對比我們實際完成的情況」的角度定期分析已完成的工作,他特別強調了它的重要性。他最近在這方面吸取的一個經驗教訓是:公司在鋼件生產計畫報告上過於激進。事實上,鋼件的實際加工速度無法滿足工廠預先排定的生產進度。這方面的工藝流程可能還有待改進,不過目前由於在排定生產計畫時將預期切削率調低,因此鋼件生產報備的準確度提高了。
當客戶詢問一個未完成的生產訂單的狀態時,公司通常會發現當完整收集到回答該問題所需的所有資訊時,答案可能已經過時了。
實際上,如果僅僅為了獲取這些所需的資訊,這一過程也將導致效率低下並浪費時間。他說,Bloom 先生早在大約七年前就意識到了這一點。當客戶詢問一個未完成的生產訂單的狀態時,公司通常會發現當完整收集到回答該問題所需的所有資訊時,答案可能已經過時了。資訊太分散了,涉及的範圍也過於廣泛。
當時,他與一位軟體發展人員合作開發了一款他稱之為「Grand View」(大資料視圖)的軟體,這款軟體可以快速提供足夠的資訊,用於回答客戶的詢問。該軟體所需的某些資料可在工廠的 ERP 系統中找到,另一些則可在本地試算表中找到。也就是說,這個自訂實用程式整合了多個不同系統的資料。他說,在使用了一段時間之後,他開始意識到這個統一的視圖工具是多麼有用,不僅可以用來回答客戶的問題,還可以幫助自己更好地理解各種導致生產中斷的原因,並且能夠協助監控工廠日益複雜的工藝流程 — 尤其是在交貨期要求越來越嚴格的情況下。
過去,以切削鑄件為主的加工作業極少需要像現在這樣多的流程控制工作。無論工廠的生產能力如何,等待鑄件完成的時間都會導致冗長的成品交貨期,工廠只有在收到鑄件後才能開始加工。如今,情況不同了。現在,更多情況下,生產作業從開始到結束都由 R&D Manco 自主掌控,公司完全要對所承諾的更短工期和按時交貨負責。責任增加意味著需要實施更全面的生產監控,因此,Bloom 先生改進了他的 Grand View 實用程式,以滿足這一需求。通過查詢 ERP 系統的資料庫來提取工件的加工迴圈時間,該自訂實用程式如今可自動計算並向管理層彙報最晚必須何時開始加工此工件,以確保滿足承諾的交貨時間。通過查詢工廠的數位庫存記錄,該實用程式現在也可以顯示庫存是否充足或者是否需要補充庫存。
這些都是很容易被忽視的重要資訊。對於將客戶供應鏈中的更多環節整合到自身業務範圍內的工廠而言,對其提出的一個要求是,必須有一套日益成熟的系統,能夠保持資訊條理清晰、訪問便捷,以便即使當工廠作業繁忙時,工作進展情況仍一目了然。
請訪問 www.renishaw.com.tw/machinetool,瞭解有關 Renishaw 機台測頭系統和軟體的更多詳情。
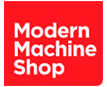