‘Seamless’ probe head upgrade advances part inspection
When Renishaw announced the PH10T upgrade offer for the obsolete PH9 motorised probe head systems, Rousant Sherwood of Henley-on-Thames, a specialist manufacturer of multi-axis machined components, was quick to take advantage of it.
Rousant Sherwood Manufacturing (RSM) has specialised in manufacturing very complex machined components for over 20 years, and has established itself as a prime supplier within several niche markets. These include components for underwater cameras and medical parts, such as highly-stressed prosthetic components and life support equipment for the emergency services. All of these markets are of a very demanding nature, requiring an ability to manufacture and supply accurate complex components. Some involve the use of six-axis turning/milling centres and even a unique seven-axis machine, with a speedy response often essential.
Components are machined from a wide range of different materials, including stainless steel, ferrous and non-ferrous metals, and certain plastics. As design and production requirements often change, Rousant Sherwood must be sure that its co-ordinate measuring machine (CMM), with its Renishaw motorised head and probe system, is always equal to the task.
The Renishaw PH9 motorised probe head that came with the CMM has proven very reliable and given sterling service.
Rousant Sherwood (UK)
Versatility
As design and production requirements often change, Rousant Sherwood must be sure that its co-ordinate measuring machine (CMM), with its Renishaw motorised head and probe system, is always equal to the task.
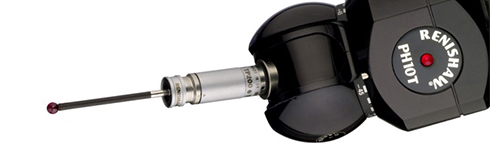
Advantages of upgrading
“The Renishaw PH9 motorised probe head that came with the CMM has proven very reliable and given sterling service”, says RSM production manager, William Law. However, when Renishaw gave notice that the PH9 was to be made obsolete, he decided to install the upgrade immediately. He was impressed with the advantages of the new Renishaw PH10T head and the substantial saving on list price with the upgrade offer.
The dramatic improvement in RSM's processes became evident with the first example of every component they subsequently produced. William Law particularly praises the marked improvement in the system's capability that has helped reduce the time taken for carrying out checks.
Quick and easy changeover
In addition, William Law found that the changeover to the upgraded unit was quick and easy, and completed in a matter of hours. All their previous measurement programs were directly compatible with the new system.
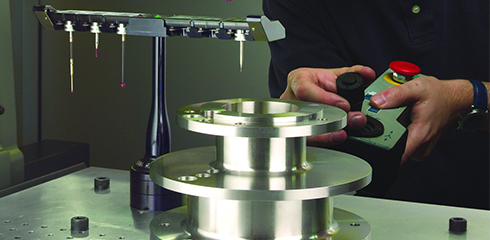
Highly automated
Rousant Sherwood - complex partsThe system at RSM is complete with a TP200 strain-gauge probe and SCR200 six-station stylus change rack. It is highly automated using programs written in-house which can be quite extensive because RSM has developed manufacturing techniques of its own that replace multiple set-up operations on the machining centres, with just one integrated operation.
The manufactured components are highly complex, requiring access to features in numerous orientations. The PH10T head and TP200 probe meet these challenges. The TP200 probe brings faster automated stylus changing without re-datuming, which enables more inspection flexibility than before, while the PH10T has the capability to carry extension bars of up to 300 mm in length. This increases the reach where accessibility is a problem.