Renishaw produces a prototype nose tip for the BLOODHOUND Supersonic car
BLOODHOUND's aim is not only to break the sound barrier but also to be the first land vehicle to exceed 1000 miles per hour (1609 km/hr) - at this speed it will be travelling the length of 4.5 football pitches every second.
Background
BLOODHOUND and Renishaw have collaborated to produce a prototype for a critical component of the Supersonic Car.
The majority of the cockpit and nose is made from carbon fibre reinforced epoxy. During the record attempt the car will experience more than 20000 kg of skin drag. However as the nose tip is on the ‘leading edge' it will experience a greater proportion of this load; up to 12000 kg/m².
Extremely good accuracy of complex surfaces
Although the outer surfaces of the polyhedron appear flat, there are in fact subtle curves which contribute to the aerodynamics. Renishaw calibrates its laser which makes the part to an accuracy of ± 50 µm over the 250 mm bed so is able to reproduce accurately the geometry in the CAD model.
Hollow taper
The hollow pocket depth is 130 mm, and tapers. If the nose tip is to be machined, as a deeper cut is made, a thicker cutter is required to maintain stiffness and this dictates the shape that can be made. With additive manufacturing, although some design rules apply, there is much more scope to manufacture novel shapes with ease.
Titanium alloy, minimal waste
Titanium alloy, Ti-6Al-4V, is easily processed using additive manufacturing, and complexity can be built in at no additional cost. Exotic materials take the same time to process as more standard materials, and, as only the material required is consumed, it may be more cost effective than expected. The honeycomb internal structure is more complex than a uniform wall and uses less material so is cheaper to manufacture.
We believe that the key benefit of using an additive manufacturing process to produce the nose tip is the ability to create a hollow tip to minimise weight. To machine this component conventionally would be extremely challenging, result in design compromises, and waste as much as ninety five per cent of the expensive raw material.
BLOODHOUND SSC (UK)
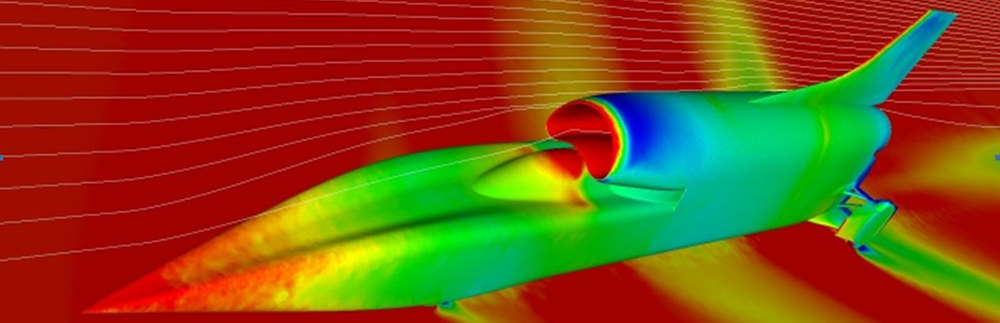
BLOODHOUND aerodynamic pressure map showing concentration at the nose tip
Image courtesy of BLOODHOUND SSC
Strong design
The hexagonal honeycomb is an intrinsically strong design; to manufacture this on internal surfaces would be very difficult in any other way. Currently, physical manufacturing capabilities outstrip digital design capabilities. Software is rapidly improving to capitalise on this new design potential - expect to see more designs inspired by nature (some of the best qualified), as well as iterative methods such as topological optimisation.
Efficient production
“We believe that the key benefit of using an additive manufacturing process to produce the nose tip is the ability to create a hollow tip to minimise weight. To machine this component conventionally would be extremely challenging, result in design compromises, and waste as much as 95% of the expensive raw material.” - Dan Johns, BLOODHOUND SSC.
Fully functional prototypes in days
Renishaw engineers and Bloodhound designers collaborated to model weight-reducing features in the nose tip: the resultant prototypes were printed shortly afterwards. The beauty of this supply chain is that there are no external delays: traditionally there would be delays waiting for the correct material to be supplied (often with a minimum order quantity), tooling, design review, and sign-off (if a significant amount of money is to be spent on the tooling the design needs to be agreed and ‘frozen'). Additive manufacturing reduces the development and prototyping cycle from months to days, freeing engineers and allowing prototypes to be made without part-specific investment. The prototype can be tested and refined to establish further improvements.
Production ready
Although great for prototypes, Renishaw is keen to emphasise that this technology can also provide a production-ready solution and currently uses it in-house to manufacture dental implant bridges and custom dental abutments, as well as mould tool inserts. The parts are ‘fully dense', that is to say better than castings, greater than 99.5%, and suitable for many applications. Hot Isostatic Pressing (HIP) is a well-established post processing technology which can be employed to ensure density and further improve material properties. This can be used if parts are likely to be pushed to their design limit.
Material development
Renishaw has a dedicated team concentrating on materials science and development to generate materials performance data and ensure that all Renishaw's materials meet or exceed current industry standards for traditional methods.
Smart solutions
Renishaw provides a design review service to anyone considering Renishaw's laser melting systems as a production solution. Your component or assembly will be reviewed by Renishaw's applications engineers who can make recommendations on DfM (Design for Manufacture), digitally process the model, and grow a sample component in one of the on-site AM250 machines. A pre-build report, inspection report, and component price estimate can also be provided on request.