Renishaw 協助精密加工廠 提升超過 80% 的鋁製熔模鑄件加工效率
數年前,由於油礦產業的不景氣,位於猶他州奧格登市的 LeanWerks 公司不得不向其他產業拓展業務;包括航太和高速自動化產業,以建立更平衡的客戶群和更穩定的工作流程。這家代工廠現已獲得 AS9100C 航太標準認證,同時也開始對其現有的部分加工設備進行改裝,以更佳地滿足新接觸產業的加工要求。
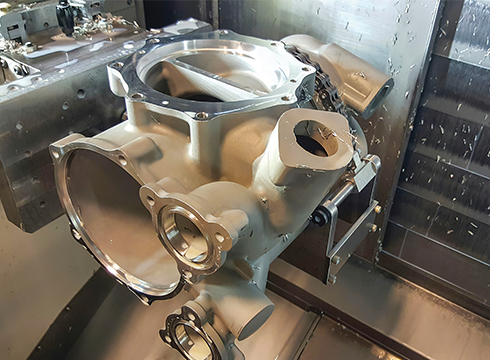
LeanWerks 開發了一個整合切削刀具、工件夾持和測頭量測技術的加工製程,實現了在車銑複合機上透過一次設定對這種熔模鑄件的五個面進行加工。圖片來源:LeanWerks
LeanWerks 總裁兼聯合創辦人 Reid Leland 舉了個例子:用於製造噴氣式引擎燃油濾清器外殼的鋁製熔模鑄件。在 LeanWerks 最初接觸到這個專案時,他們某家航太零組件鑄造客戶的生產進度已經落後交期計畫將近一年,原因是內部加工製程太慢,導致生產效率極低。因此造成這家鑄造廠的客戶(即安裝這款外殼製造噴氣式引擎的 OEM)對他們失去耐心,而且這項作業的延誤還導致其他訂單被迫積壓,令其他客戶頗有微詞。因此,為了減輕內部加工資源的負擔,該鑄造廠找上 LeanWerks,希望他們承接這種鑄件的加工作業。
相較其他鑄造工藝,熔模鑄件具有形狀複雜但尺寸精度高的優點,因此許多工程師在其工件設計中指定使用熔模鑄件;但是,這些鑄件仍需要經過精加工才能實現精確的裝配,以達到產品功能的高效能要求。
然而,由於這類毛胚鑄件複雜各異,而且相關的工件夾持要求比較棘手,因此有些工廠不願承接此類加工作業。
比如說,燃油濾清器外殼需要多項加工操作,包括深孔銑削、鏜削、端面銑削、鑽孔、攻絲、內徑開槽和 3D 輪廓加工。起初,LeanWerks 認為可以先在三軸銑床上進行幾次設定,然後在車削中心上進行一次設定,透過這種方法完成這項作業。但是後來他們發現這種方法並不理想,因為在多次設定之後,工件的複雜基準設計的嚴苛位置公差要求將難以被滿足。
LeanWerks 轉而考慮如何充分利用現有的 Mazak Integrex i200S 車銑複合機的銑削能力,盡可能減少在加工過程中接觸工件的次數。該工廠過去主要使用這機台生產錐形旋塞閥鑲套閥芯(用於石油和天然氣產業的高壓泵送作業),應用於水力壓裂和連續油管等方面。Integrex 機台既可以車削工件的錐形外徑,又可以銑削工件內部的斜向(或橫向)流道孔,因此非常適合加工閥門的鑲套閥芯。這機台還可以銑削在裝配時需要接合 O 型圈的孔,由於這些孔是錐形面,因此需要進行五軸輪廓加工。
也就是說,在車銑複合機上加工燃油濾清器外殼時,雖然不需要車削操作,但也存在多項挑戰。例如,A356.0 航空級鑄鋁的二氧化矽含量很高,切削難度大。
此外,這種鑄件的幾何形狀複雜,在各個表面上具有多個角度各異的特徵(包括鑄件內部 13 英寸深的底部有一個關鍵裝配特徵),而且薄壁部位在加工過程中會產生振動問題。再加上,這種工件具有公差要求嚴苛的複雜基準結構,例如:某些寬距特徵的位置度公差為 0.25 mm,而其他窄距特徵的尺寸公差為 0.01 mm,位置度公差為 0.05 mm。
因此,LeanWerks 採取了三大步驟,實現了在車銑複合機上藉由一次設定對熔模鑄件的五個面進行高效加工。第一步是設計一款夾具來固定鑄件,以便對工件的五個面進行加工。這款夾具的一個關鍵部分是支架,它與鑄件的主體接合,同時可接近支架腿之間和旁邊的工件特徵。為了將鑄件固定在支架上,LeanWerks 在支架腿之間安裝了鏈條和滑輪機構,以實現均勻夾緊。
由於車銑複合機沒有足夠的 Y 軸行程可接近所有特徵,因此 LeanWerks 在夾具中加入了一個 Setco 燕尾滑塊,使支架和工件能夠滑動並在可接近的位置重新夾緊,而無需完全重新固定工件。為確保剛性,支架被安裝在鋼製底板上,並通過定位銷和焊接進行加固。底板安裝在在燕尾滑塊的鞍座上,而滑塊底座安裝在機台現有的三爪卡盤的主爪上。
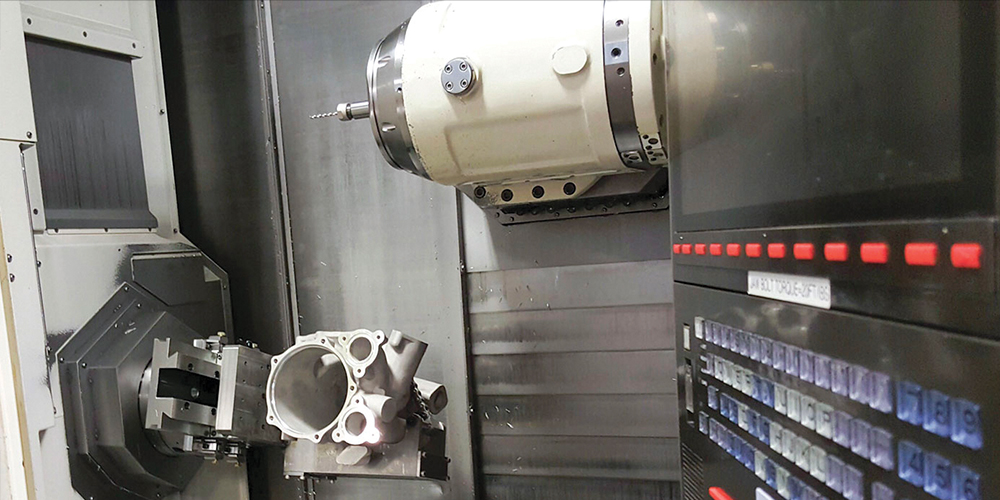
由於該工件的尺寸限制,車銑複合機的 Y 軸行程無法使主軸接近待加工工件的所有部位。為了解決這個問題,LeanWerks 開發的夾具加入了燕尾滑塊,使夾緊的工件能夠滑動並在可接近的位置重新夾緊。然後透過測頭量測程式檢測重新定位的工件的位置度。
第二步是,該工廠整合了一套接觸觸發式測頭量測系統。由於每個毛胚鑄件的形狀略有不同,而且用於解決 Y 軸行程問題的滑動夾具會改變工件的位置,因此必須進行接觸觸發式測頭量測。透過測頭量測可精確地確定工件移位後的新位置,進而使後續刀具路徑與實際工件位置實現最佳擬合。
事實上,該工廠意識到,除了標準長度的測頭之外,他們還需要一個量測範圍加大的測頭,用於量測工件內部深處的特徵。由於車銑複合機只有一個測頭量測通道,LeanWerks 使用 Renishaw RMI-Q 無線電介面對機台進行了改裝,並在主機控制台中安裝了可編程邏輯控制器 (PLC) 卡來處理第二個測頭的訊號。短測頭使用長度為 25 mm 的測針,長測頭使用裝在 200 mm 延長杆上的 50 mm 長測針。兩款測頭均使用 Renishaw RMP60 測頭。
使用 Renishaw 的 Inspection Plus 工件量測軟體對測頭量測程式進行編程,並將生成的代碼加到機台程式的適當位置。初始測頭量測程式在外殼腔內的底部埠及外殼正面的開口上採點,以確定工件的中心軸。量測的其他特徵包括靠近表面的其中一個小埠,以確定工件的旋轉方向;以及主側法蘭的一個內壁,以確定工件的 Z 軸位置。Mazak 的工件位置誤差補償 (WPEC) 軟體模組能夠利用初始測頭量測位置進行計算,以檢查工件隨主軸分度運動後的真實位置偏差。在初始測頭量測程式之後,再執行後續量測,以確認相關特徵和加工後表面的位置。
最後一步是,他們採用先進的切削刀具技術對該工件和研磨鋁材料進行深加工操作。在這項作業中,該工廠使用 Rego-Fix 公司的 powRgrip 刀具夾持系統。作為熱縮配合的替代方案,powRgrip 是一種機械壓合系統,由刀架、精密夾頭,以及一個用於將夾頭和刀具插入刀架的緊湊型台式液壓夾緊裝置組成。Rego-Fix 表示,該系統能夠產生高夾緊力,同時將總指示器讀數保持在小於 0.0001 英寸。該系統的剛性有助於提高刀具使用壽命和切削精度。
用於這項作業的切削刀具必須具有高正傾角,以極高的速度運行,且切深較小。LeanWerks 選用的是 Garr Alumistar 立銑刀,以及一把帶有無塗層、高拋光、高正傾角刀片的小型面銑刀。
LeanWerks 還使用線外刀具設定裝置為這項作業進行設定。這項操作不僅可對刀具進行外部刀具設定,更重要的是,還可檢查切削刃、驗證成型刀具的形狀和量測跳動度,進而協助校驗和故障排除。
轉捩點
LeanWerks 開發出在車銑複合機上加工熔模鑄件的製程,將每個工件的加工效率從每件 10 小時提升到不到 2 小時。在此基礎上,該工廠還在探索更多方法,以提高現有的生產加工能力,向更多產業拓展業務。
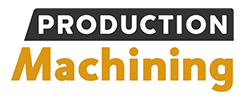
英文原文刊載於《Production Machining》期刊 (productionmachining.com)。© 2021, Gardner Business Media, Inc., 6915 Valley Avenue, Cincinnati, Ohio.