CMM inspection: “There is no other option to REVO, nothing else comes close”
Aerospace sub-contractor ANT Industries carried out a study on its production processes with the aim to make improvements, it was clear that inspection was a major bottleneck.
Final part inspection
However, following the purchase of a new co-ordinate measuring machine (CMM) equipped with a Renishaw REVO five-axis scanning system, the situation has changed markedly. “Now we have the new machine we are playing a different game – there is no other option to REVO, nothing else comes close”, adds Mr Rowley. “The closest alternative was a system costing five times as much, but it wouldn't have achieved the same levels of throughput.”
ANT produces over 1000 different machined parts, approximately 85% of which are supplied to the aerospace industry, requiring a high proportion of final part inspection. CMM inspection of finished parts is taken for granted in the aerospace industry, and ANT has to offer it to their customers as part of the manufacturing process. Some parts need 100% inspection, while others must have at least 1 in 10 inspected. “REVO gives us a clear competitive advantage, I am in no doubt it will help us win work”, says Alan Naylor, ANT's Technical Director, who is very pleased with the new CMM. “Not only does it massively reduce inspection time, it also measures complex features like the leading edges of blades, which we just couldn't do before.”
With a sophisticated, highly efficient machining operation, ANT Industries also use Renishaw's spindle-mounted touch probes and tool monitoring systems for process control on their multi-axis machining centres and CNC lathes. However, post-process inspection had to be improved to keep pace.
“Our inspection method now uses a completely different approach,” Mr Rowley explains, “We have taken a big jump in a very short time from slowly taking multiple touch-trigger points with the old Tesa CMM, to rapid 5-axis scanning. But the operator has taken to it very well and we are currently, on average, programming one new job a day. Added to that, the old CMM really struggled to maintain the accuracy needed; there were small but frustrating inconsistencies all over the measuring volume which we had to correct to keep an acceptable standard. We had to do something.”
Mr Rowley is particularly impressed with how the REVO system measures one type of turbine blade with a very complex form. “Each of these blades used to take 2 hours to measure, now it can be done in 20 minutes. With this sort of throughput I'm happy to agree to customer requests for 100% inspection of most components. But that's not the whole story; this is a complex shape with a critical leading edge that the touch-trigger CMM just couldn't measure at all.”
83% inspection time reduction
Prior to the new REVO-equipped CMM, ANT had to analyse the form using a projector technique to measure the shape – a long and laborious task. Now, the REVO system does the same job with a rapid profile scan, overlaying measured data onto the CAD design model and applying variable tolerances in different areas. “The ability it has given us is undoubtedly a key business advantage”, adds Mr Rowley. Calibration of the probe, required periodically to ensure accuracy, is also an area which has seen significant benefits. Previously it took some two hours to calibrate all the different probe angles needed for a measurement routine, whereas the REVO system calibrates in just 20 minutes.
ANT needed their new CMM to be supplied quickly to satisfy the measurement needs of a large blade contract. They decided to purchase a new ceramic CMM frame from Metris (now Nikon Metrology), without a probe system or controller, with axis travel of 2 m in Y, 1.2 m in X and 1 m in Z to allow the measurement of large engine rings. Renishaw then fitted the frame with its REVO five-axis measuring head and probe system, together with its UCC2 universal CMM controller. The work was done at Renishaw's Gloucestershire assembly plant prior to installation at ANT, although Renishaw also carries out retrofits at a customer's site.
The system uses Renishaw's new MODUS™ metrology software, which has particularly impressed Mr Naylor. “Support from Renishaw has been excellent, not just in training operators in using the MODUS software, but also introducing a new way of thinking to inspection methods. It could have been intimidating but it turned out to be a very straightforward transition.”
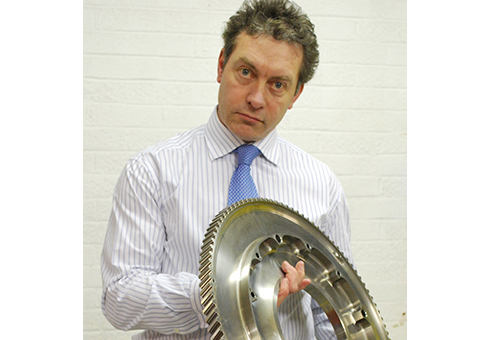
There were thousands of non-productive hours a year where parts were either in inspection or waiting to be inspected. These are expensive parts without any value being added.
ANT Industries (UK)