智慧製造解決方案倍增燃氣渦輪機元件生產力
Doncasters Precision Castings – Deritend 是製造熔模鑄造及加工工業燃氣渦輪機翼片的領先製造商。翼片多以鎳與鈷組成的超級合金製造。
Doncasters 致力推動業務增長,堅守精實製造及快速原型製造等方式持續精益求精的信念作持續投資。這讓 Doncasters 的加工服務需求大幅增長,並以之促成了其熔模鑄造業務。這需求更讓 Doncasters 大幅投資超過 200 萬英鎊採購 Mazak 工具機、基礎設施及製造軟體,以便有效加工逾 14 種新產品。
背景
在購買 Mazak 五軸加工中心之前,Doncasters 使用傳統的三軸加工中心搭配定位夾治具處理類似作業。這類製程不僅耗時,也需要具備高度技術的工具機操作人員。一般管嘴元件的生產週期時間 (包括設定與加工) 為四小時,因超過可用產能而無法符合不斷增長的需求。此外對工程團隊而言,夾治具更是過時且昂貴的解決方案。因此 Doncasters 決定針對加工技術進行重大投資,訂購三台 Mazak VORTEX i-630V/6 立式加工中心。這些工具機協助 Doncasters 在內部進行加工作業,並為客戶提供單一來源解決方案。
購買的 Mazak 工具機更配備了採用專利 RENGAGE™ 應變電感技術的 Renishaw RMP600 高精度測頭,於生產複雜 3D 形狀及輪廓工件時,提供無可比擬的超微米量測,是生產作業的理想選擇。不過,在最初部署這些新設備期間,Doncasters 認為需要額外支援,因此 Renishaw 便邀請了其關係企業 Metrology Software Products Ltd (MSP) 參與其中。
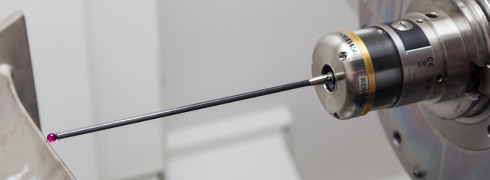
挑戰
Doncasters 面對的挑戰是提升一次到位的加工比率,消除發生誤差的任何可能,以及增加整體生產力。Doncasters 工程經理 Ollie Macrow 解釋:「在處理價值數千英磅的超級合金鑄件時,最好能在切削金屬之前確認加工零件正確無虞。成本也是其中的考慮因素:除了鑄件成本以外,還有損失的時間,以及就材料而言的高成本刀具。此外,就某些無法重工的特定元件而言,如果加工發生錯誤,就變成了廢料。我們知道必須量測零件,但我們面對的挑戰是尋求不使用夾治具的方案。」讓問題雪上加霜的是我們的量測經驗相當有限,過去僅用於基本定位和簡單平面對齊作業,因此 Renishaw 的參與成為成功的關鍵。
Doncasters 也希望不再使用昂貴耗時的夾治具。Ollie 繼續表示:「使用夾治具產生許多問題:成本昂貴,需要高度技術才能準確定位工件,而且如果夾治具損壞就無法為工件找正,無法加工,所以夾治具必須高度維護,因而增加時間與成本。我們的挑戰是以更簡單的模組化系統取代夾治具,並減少設定程序的操作人員介入。」我們必須達到生產目標,因此在引進 Mazak 工具機時,縮短設定時間是重要的考量因素。Doncasters 使用這些新設備在內部執行大部分加工作業時,仍然需要轉包部分次要作業。所以公司希望藉由提升生產力,以達到將外包作業回到內部生產的未來目標。Ollie 表示:「這對公司生產力有著正面影響。如果我們可以自己加工,就不必等待兩天運送工件時間。」
我真心認為如果沒有 Renishaw 和 MSP 的協助,我們就無法成功加工鑄件。Renishaw 與 MSP 提供出色支援,我們每次致電諮詢,他們總是全力協助,並在我們有需要時及時前來。
Doncasters Precision Castings – Deritend (英國)
解決方案
Renishaw 應用工程師分析了 Doncasters 專案後,認為 MSP NC-PerfectPart 與 NC-Checker 軟體結合 RMP600 測頭,是最適合 Doncasters 需求的解決方案。結合以上硬體及創新軟體,可協助使用者在工件定位時找出誤差,並在切割前掌握設備的幾何性能誤差。第一步是「勘測」工具機建立基準化分析。NC-Checker 在執行工具機五軸檢查作業前,檢查測頭效能。這樣可以在工件設定及金屬切削之前,確保量測及加工性能都在設定公差之內。工具機檢查可定期執行,只要幾分鐘就能完成。長期下來,這樣可確保機器持續在設定參數內運作,並生產精確工件。
NC-PerfectPart 解決工件在工具機上因找正不良造成的問題。這對不規則、複雜形狀及以五軸加工的工件特別重要。設定這類工件會較耗時,且難以精確一致地完成。利用 RMP600 工件,只要使用以元件 CAD 檔案建立供 RMP600 測頭量測的程式便可解決以上問題。
首先,以測頭定位工件,消除工件在工具機的定位誤差。找正數據將上傳至工具機控制器,自動計算補償,以生成與工件位置完美配合的加工程式。自動化的設定作業,意味著夾治具在製程中不再那麼重要,不但可消除人工設定誤差,即使是設定最複雜的元件,也只要幾分鐘就能完成。
此外,材料狀況、移載系統及溫度等要素,都可在加工製程的初始階段列入考量,進一步降低製造不良零件的風險。
在金屬切削之後,NC-PerfectPart 可在工具機內先確認工件的精確度,然後再將工件由工具機移往 CMM 進行檢查。
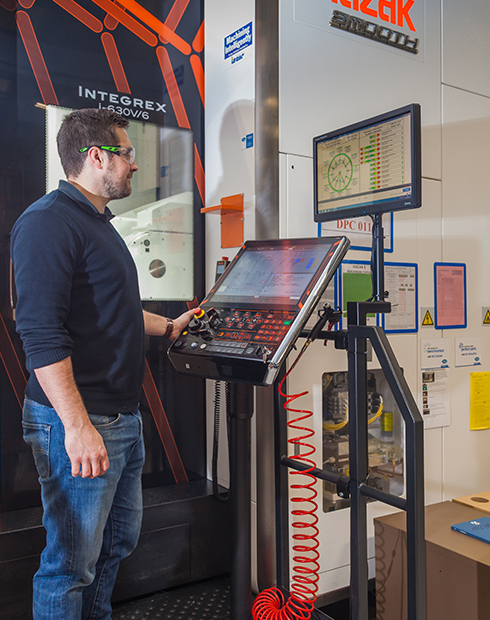
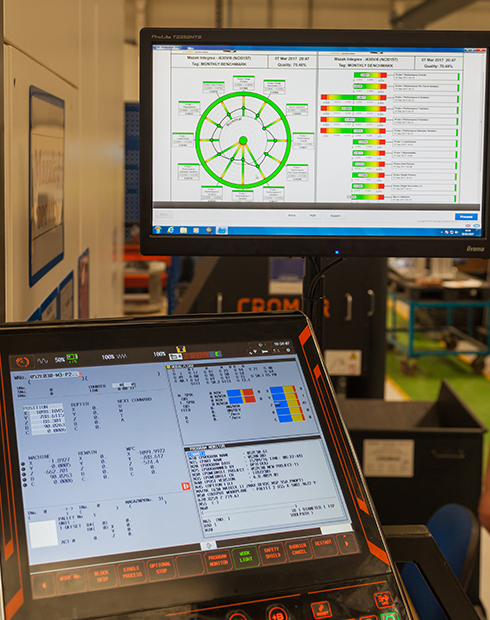
結果
在使用 RMP600 及 MSP 軟體之前,Doncasters 設定及加工一般的工業燃氣渦輪機管嘴需要四小時。現在只要不到兩小時,就能量測、加工及檢查相同工件,讓 Doncasters 提升 50% 生產力。更為複雜的元件生產,過去加工時間可能長達八小時,並需具有高度技術的操作人員在場監督加工製程。但現在這類工件生產就和簡單零件一樣以相同的兩小時週期製造,進一步節省更多成本。Doncasters 與 Renishaw 及 MSP 合作強化工件找正系統,實現更好成果;機上量測、CMM 量測及 Bluelight 掃描系統資料之間的關聯性也獲得改善。
Ollie Macrow 對這次的成功表示:「結果令人鼓舞,如果沒有 Renishaw 及 MSP 的協助,我們不可能有現在的成果。」
他繼續表示:「一開始決定採購工具機時,我們與 Mazak 會面表示『要如何進行這一切?』Mazak 不認為我們能以現有設備達成目標,之後 Renishaw 與 MSP 共同提供我們所需的解決方案。客戶也為我們能大幅提升一次到位的通過率表達了正面回饋意見。我真心認為如果沒有 Renishaw 和 MSP 的協助,我們就無法成功加工鑄件。Renishaw 與 MSP 提供出色支援,我們每次致電諮詢,他們總是全力協助,並在我們有需要時及時前來。」