Renishaw 精密校正產品協助打造高品質的高端工具機
傳統檢測工具無法全面評估工具機誤差的整體情況,難以滿足現代工具機(尤其是五軸機)加工的精度和效率要求。採用 Renishaw 全系列機器校正產品,對機台從組裝、整機校正驗收、故障排除乃至日常精度維護等各個環節的品質把關。
工具機加工精度的提升一直是機台製造商所追求的目標。然而,加工精度受到多種因素的影響,包括工具機導軌的安裝誤差及床台部件組裝缺陷所帶來的各種幾何誤差、空間定位誤差等原因。這些誤差若無法有效消除或降低,將直接影響工具機的最終加工精度,進而影響產品的品質和效能。工具機製造商在面對這一挑戰時需要尋求解決方案。
隨著科技的不斷發展,傳統檢測工具已無法滿足現代工具機加工的精度和效率要求。單光束雷射干涉儀是一種較為普遍使用的量測工具,通過量測特定位置的參數來評估工具機的定位精度。然而,這種方法只根據該量測位置的量測結果對該工具機的定位精度下結論,往往無法全面評估工具機誤差的整體情況,這個問題在五軸工具機加工時更為明顯。
為了解決這一難題,身為中國領先的五軸加工中心機製造商之一,廣東今科機床有限公司(以下簡稱今科)導入 Renishaw 全方位機台校正方案,為其工具機從組裝、整機校正驗收、故障排除乃至日常精度維護等各個環節的品質把關。
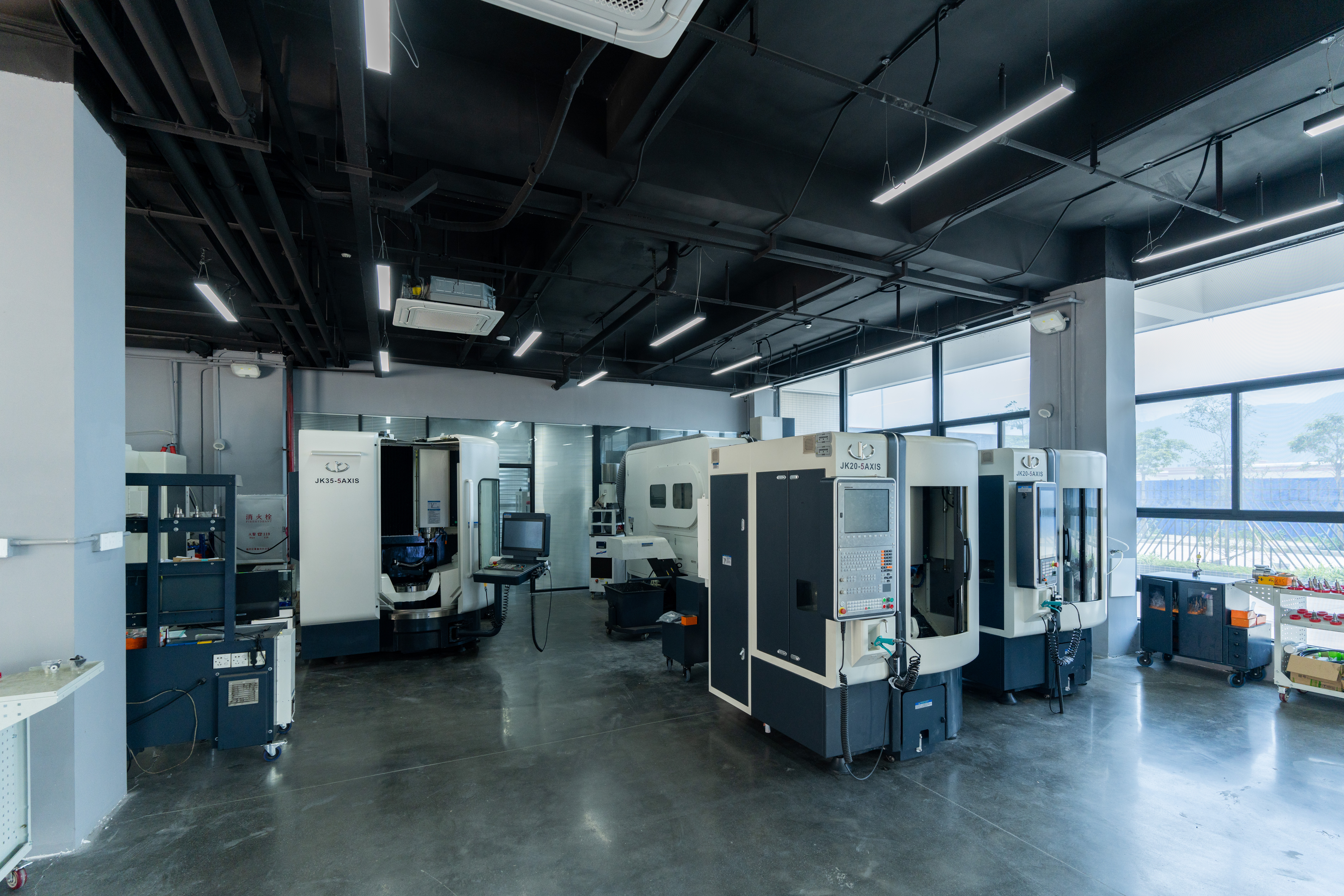
今科工具機展廳
工具機行業要求非常嚴格,對功能、性能和精度的穩定性都有高度要求。我們很早就開始導入 Renishaw 全系列的校正產品,並且得到了全面的技術支援。在這個過程中,我們也學習到了很多量測方面的技術知識。
廣東今科機床有限公司(中國)
工具機組裝
床台的基準在工具機裝調精度中扮演著重要的角色,尤其對於精密工具機而言,從鑄造底座開始,就需要嚴格控制其精度。今科主要把 XK10 應用於工具機組裝階段,以確保工具機在組裝過程中的各項幾何精度,例如真直度、平面度、垂直度和平行度等。在導入 Renishaw XK10 校準雷射系統之前,工具機組裝過程中僅能依賴一些傳統工具進行校正,如百分錶、千分錶、大理石角尺和自準直儀等。然而,這些工具不僅需要大量的空間來存放,還需要多名操作人員的協作才能完成校正工作。此外,這些工具極度依賴操作人員的熟練程度,需要定期維護工具並手動記錄和存檔檢測資料。
然而,隨著 XK10 校準雷射系統的使用,這一情況發生了改變。目前 XK10 已能夠完全替代之前使用的各種傳統工具,並且適用於不同型號的工具機。這一技術的導入不僅使得操作更加簡便和快捷,同時也實現了資料的自動封存,方便追溯和管理。這種數位化、資訊化管理方式為工具機組裝過程帶來了便利,同時提升了整體的效率和準確性。今科技術總監邵建卓先生給予 Renishaw XK10 校準雷射系統極高的評價:「XK10 校準雷射系統非常輕便,操作人員不再需要搬運笨重的大理石,工作變得輕鬆且效率提升。使用 XK10 後,生產效率大幅提升,相比起之前使用傳統工具,效率提升了 200%以上。」
在檢測真直度方面,XK10 給今科留下了深刻的印象。使用 XK10 只需要進行一次量測,就能獲得水平方向和垂直方向的兩個真直度數據。以往在檢測不共面的導軌平行度時,他們需要客製夾具進行檢測,這無形中增加了成本。對於一些特殊結構的機台而言,傳統工具甚至無法完成檢測工作。邵總監表示:「XK10 不僅提高了組裝效率,同時也在不增加人力成本的情況下提升了產能。這使得今科能夠在更短的時間內交付產品,提高了市場競爭力,並獲得了更多的訂單。」
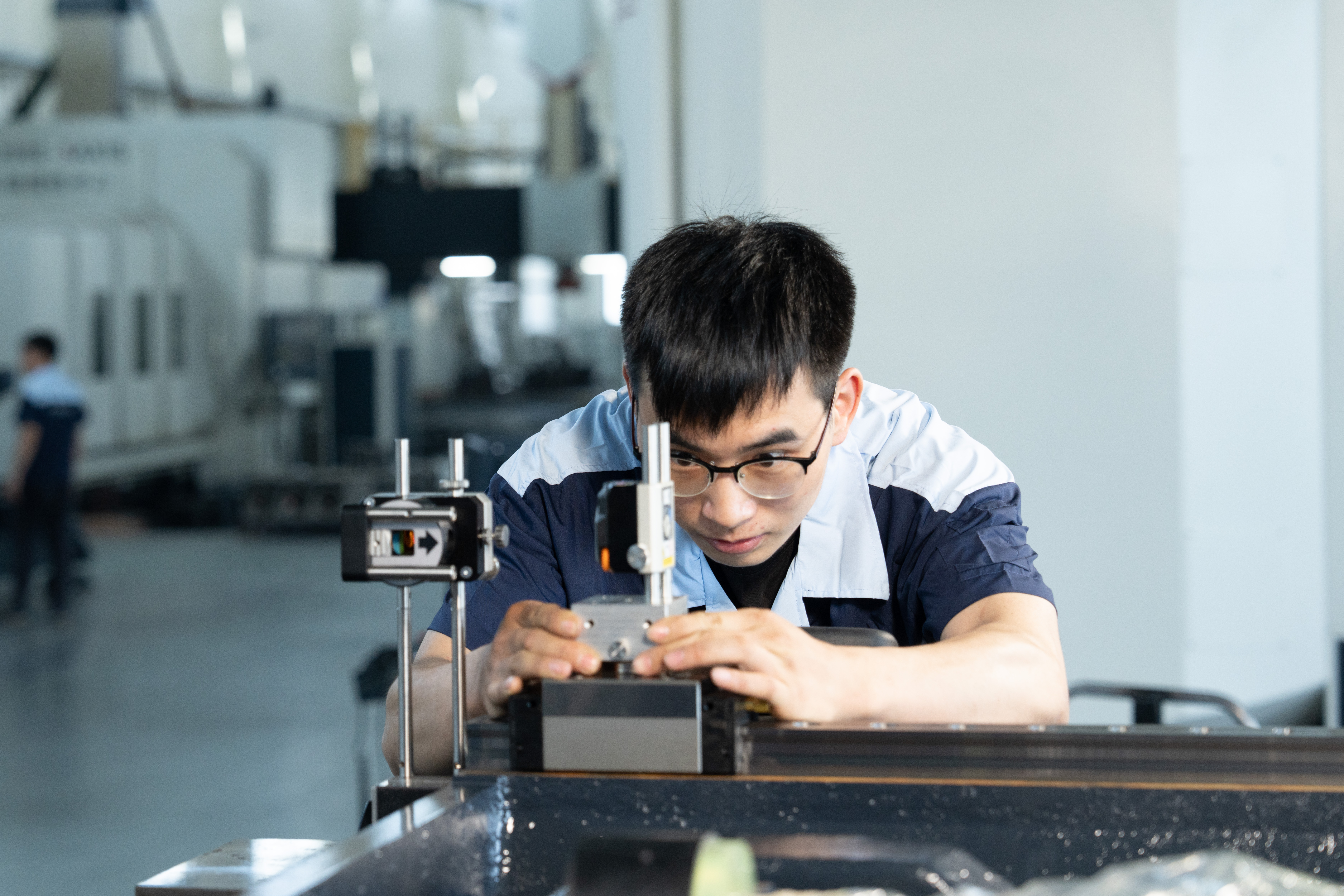
今科使用 XK10 校準雷射系統儀做工具機精度裝調
工具機驗證
當前工具機結構日益複雜,工件製造工藝也日趨精密。僅量測線性性能是遠遠不夠的。軸向結構的摩擦效應和其他故障會導致軸向在移動時旋轉,造成工具機元件的指定位置和實際位置之間出現偏差。這些「角度」和「真直度」影響會出現嚴重的特徵位置誤差或輪廓和表面偏差,最終導致工件尺寸誤差不達標,增加廢品率。
在工具機組裝完成後,技術人員需要對整機性能和各項精度進行驗證,並在需要時進行機台校正或補償。目前,今科使用 Renishaw XM-60 多光束校正儀針對五軸工具機進行驗證,包括線性軸誤差來源分析、空間精度檢測、空間精度補償、動態真直度檢測以及工具機定位精度的不確定度分析等。
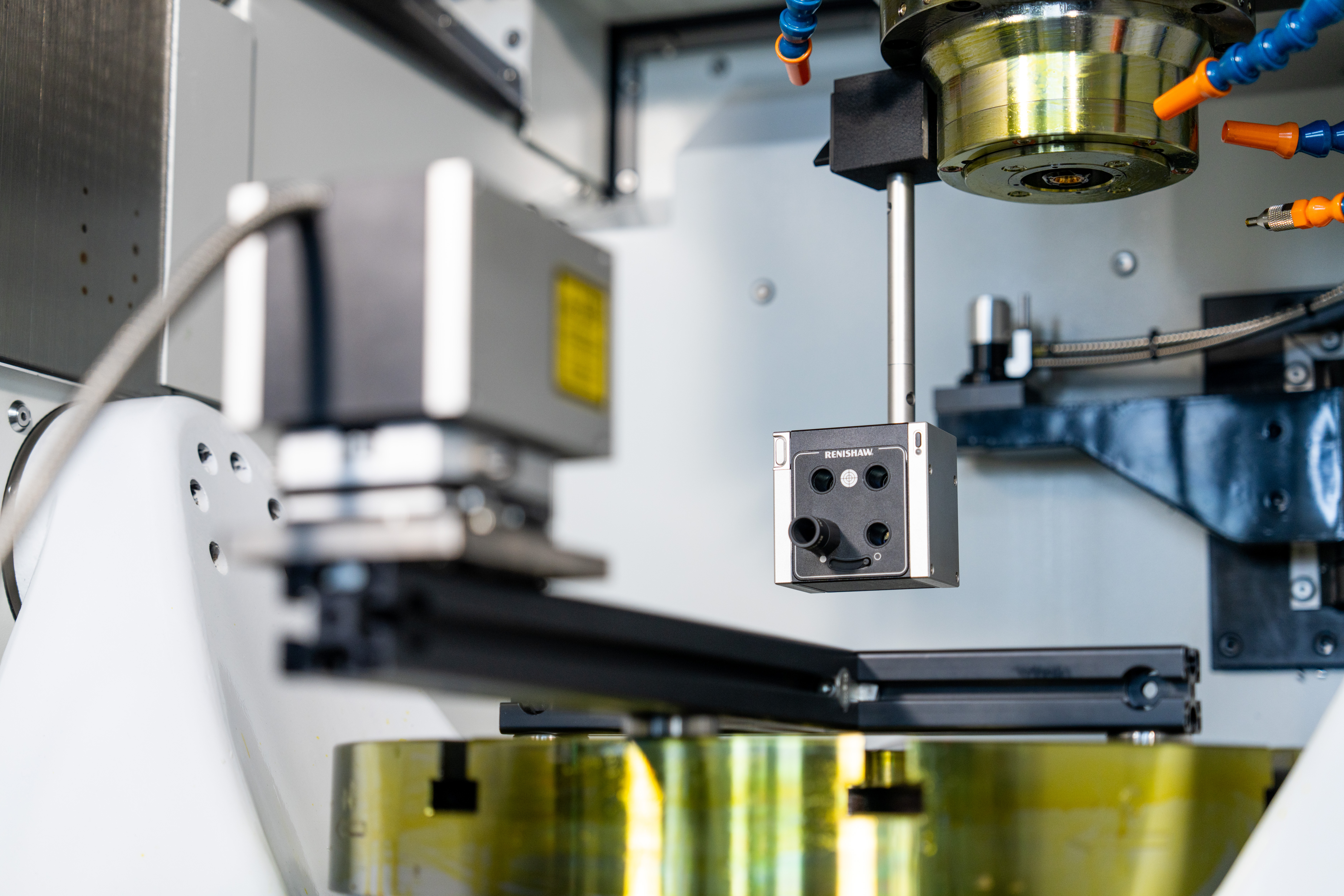
今科藉由 XM-60 多光束校正儀對五軸工具機進行驗證
今科選擇 XM-60 主要是因為他們了解到單光束雷射干涉儀存在侷限性。單光束雷射干涉儀採用單參數量測,無法同時獲得光路在兩個方向的準確移位,也無法量測出被測機台在量測行程中不同位置的角度(如滾擺角),這導致無法得知空間真直度的誤差和阿貝誤差。
以往單光束雷射干涉儀使用者僅通過對機台軸向的某個位置進行定位精度檢測合格,便認為該軸基本滿足加工要求。然而,在實際加工過程中,仍然存在一些已通過定位精度驗收的機台出現零件加工品質問題。這是因為這些機台可能存在較大的各種角度誤差,無法滿足整個機器空間精度的要求。
換句話說,檢測結果也僅基於該量測位置的結果對工具機的定位精度做出結論,缺乏對軸向的空間誤差資訊的全面體現,確實不夠完全。在工具機精度驗證的實際應用中,經常出現同一軸線在不同檢測位置的定位精度可能相差很大,尤其在五軸工具機的加工中,這個問題尤為突出。在市場上尚未出現多光束雷射校正儀之前,廠商一般使用單光束雷射干涉儀對精密機台進行檢測,不過每次架設僅能量測一個誤差參數。今科也不例外,他們以往採用 XL-80 雷射干涉儀和 XR20 旋轉軸校正儀對機台進行檢測,邵總監說道:「在導入 Renishaw XM-60 多光束校正儀後,我們發現它具有更高的量測效率,可以大幅簡化操作設定,一次架設就能完成 6 個自由度的誤差量測,包括滾擺角的量測,並且結合軟體能夠快速分析誤差來源。
目前,今科主要將 XM-60 應用於五軸工具機的校正與驗證,分析主要空間幾何誤差的根源,為批量生產和組裝精度的保持奠定基礎。而在其他機型,今科仍然依賴 XL-80 雷射干涉儀進行檢測。使用 XM-60 能提高至少 4 倍以上的效率。」
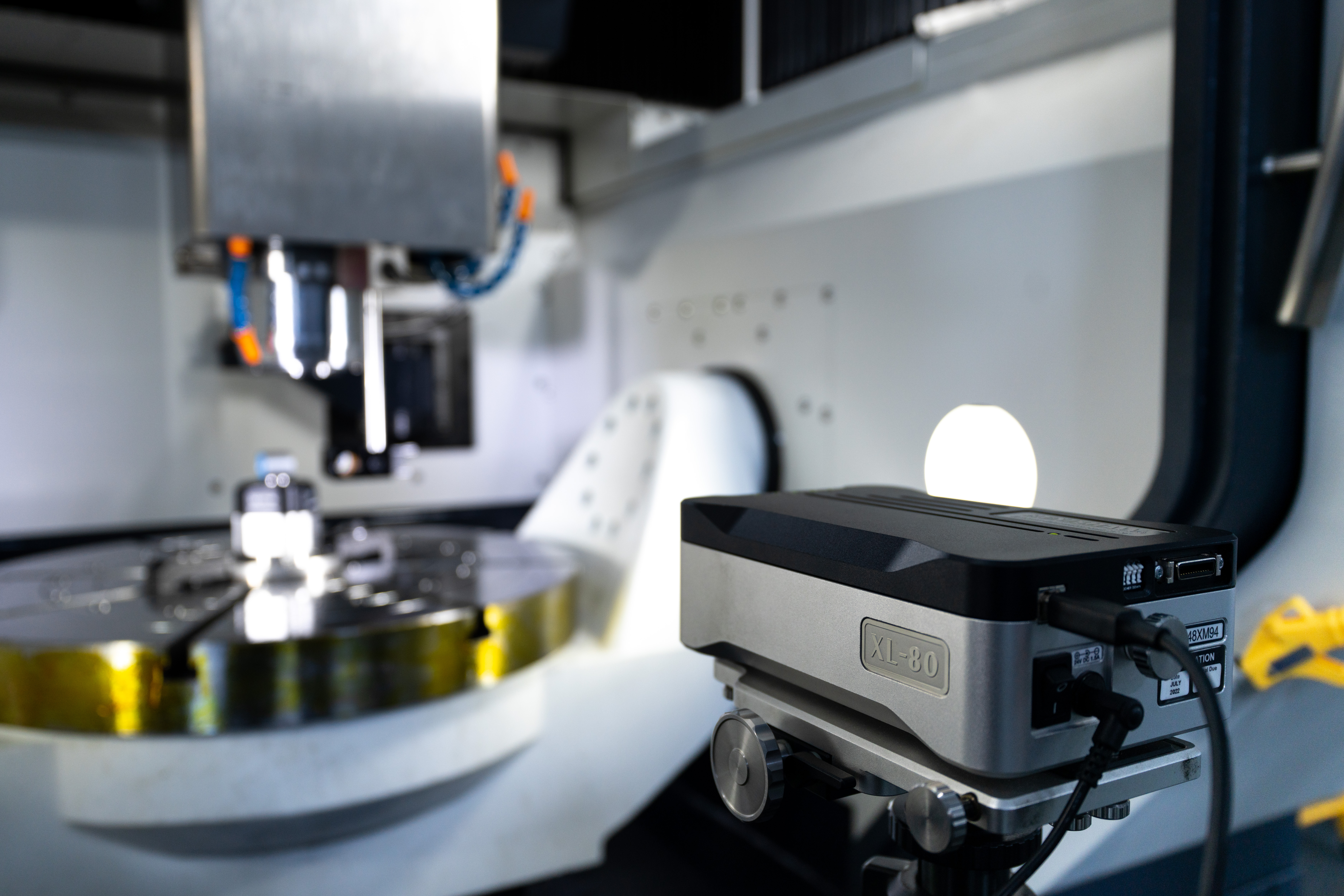
XL-80 雷射干涉儀和 XR20 旋轉軸校正儀針對機台進行檢測
Renishaw XM-60 是市場上先進的方案,採用干涉原理量測角度和線性,並將採用位元敏組件(PSD)量測真直度的簡便性集於一體的四光束系統,其封裝尺寸大幅減小。XM-60 通過將雷射光束與工具機軸校準,直接量測工具機誤差,相較於其他量測技術使用複雜數學計算求得工具機誤差的方法,XM-60 的方式具有可追溯性。另外有別於其他產品,XM-60 採用專利保護的光學原理滾動量測技術,不依賴重力可在任何方向直接進行滾擺角量測。
快速故障診斷
在工具機經過驗證和校正後,在發貨給客戶之前,今科的技術人員會使用 Renishaw QC20 循圓測試儀進行快速故障診斷,模擬實際操作以檢測機台的綜合精度。有需要時他們會對機台進行修正和補償,以確保所有機台在出廠前處於最佳狀態。邵總監表示:「QC20 循圓測試儀可以在 10 分鐘內檢測出工具機的多項運動誤差,幫助我們快速識別加工品質未達標準的原因,方便我們追蹤和解決相關問題。」
Renishaw QC20 循圓測試儀配合 Ballbar Trace 軟體可以根據國際標準快速驗證五軸工具機的精度,例如 ISO 10791-6 標準,該標準旨在驗證具有三個線性軸和一個或兩個旋轉軸的四軸和五軸工具機的運動精度。由該標準定義的刀尖跟隨測試可以使用 QC20 循圓測試儀完成。在多軸移動期間,工具機會試圖保持刀尖和工件特定位置之間的固定距離。循圓測試儀可以量測刀尖與工件之間的任何偏差,並根據此量測結果評估輪廓加工性能(稱為刀尖跟隨測試)。使用 QC20 循圓測試儀進行快速故障診斷, 模擬實際操作以檢測機台的綜合精度。
使用 QC20 循圓測試儀進行快速故障診斷,模擬實際操作以檢測機台的綜合精度。
關於今科機床
今科機床是一家比肩世界先進一流工具機企業的公司,同時也是中國國家高新技術企業,並擁有廣東省級的「五軸工程技術研究中心」。他們擁有自主核心技術,主要專注於研發和生產五軸同動加工中心等六大系列工具機,共計 28 個不同品項的產品。這些工具機廣泛應用於新能源汽車、航太、醫療設備等高端製造業領域。