Bu sayfa şu anda sizin dilinizde mevcut değildir. Google'ın Çeviri sistemini kullanarak
otomatikleştirilmiş çeviriye
ulaşabilirsiniz. Bu hizmeti sağlamaktan sorumlu değiliz ve çeviri sonuçları tarafımızdan kontrol edilmemiştir.
Eğer daha fazla yardıma ihtiyaç duyarsanız lütfen
bizim ile temasa geçiniz.
Revolution in ceramic tile printing signals renewed demand for encoders
The end of ceramic tile screen printing?
Screen printing (flat-bed or cylinder) has traditionally been used for tile decoration and involves applying each of the colours in a design using a separate roller or screen. Digital ink-jet printers for ceramic tiles first appeared at the turn of the century; however, it took a further decade before the technology was mature enough for mass-production lines. Colour printing sits towards the end of the tile manufacturing process - after the tile has been pressed and dried into a green body and following application of a glaze but before firing in a roller-hearth kiln. There are currently 10,000 kiln lines globally corresponding to one print system per line.
The screen printing process has a number of disadvantages including high set-up costs, necessarily long production runs, high cost of ownership and difficulty in exactly matching colours on repeat orders. Digital capability has become the gold-standard for the industry and various manufacturers are now producing ink-jet printers for the ceramic / porcelain tile industry. Several competing inkjet technologies presently enable precise ink application down to the picolitre (10-12 L) at substrate feed speeds of up to 70 m/min.
IT Strategies Inc, US-based specialists in digital printer technology, predicts 86 % penetration of the inkjet ceramic printer market in Europe by 2017, with China still in the early stages, at which point ink-jet printing on ceramic tiles will be worth approx. US $1.3 billion annually.
Inkjet printing is a digitally driven, non-contact, high-definition method of printing patterns or images onto a wide range of substrates. Increasingly the preferred method for applications such as ceramic tile decoration, it delivers substantial benefits over traditional processes in terms of pattern flexibility, higher image definition, reduced waste, elimination of hard tooling and greater automation. Ceramic tile full-width printing machines will become increasingly popular as demand for custom and bespoke designs increases in both consumer and commercial markets. The recent rise of custom design tile services for batch sizes as small as single digit quantities has been made possible by the viability of short print runs – now more affordable than ever. Inkjet printer throughput has also increased dramatically over the last few years due to the advent of full-width print-heads that remain largely fixed without the need to horizontally scan the substrate. However, the picture is still evolving and full end-to-end ink-jet processing from tile texturing to glazing and decoration is conceivable. This article examines the development of single-pass printing and how the latest optical encoder solutions may help.
Enter the future
There has been a sizable uptake of digital inkjet printers in the last five years, such that sales of traditional screen printers have collapsed. Optical encoders have not generally had much penetration in the ceramic tile industry, but this now looks likely to change. Experts estimate that 35% of tiles will be digitally decorated within the next three to five years. Approximately 50 % of world tile manufacturing currently takes place in China.
Inkjet printing offers two print modes: binary print and greyscale. In binary print, the droplet size remains constant. Therefore, binary print provides the only true comparability of dots per inch (DPI). In greyscale printing, the ink droplet size varies to help create a more pleasing and photo-realistic image.
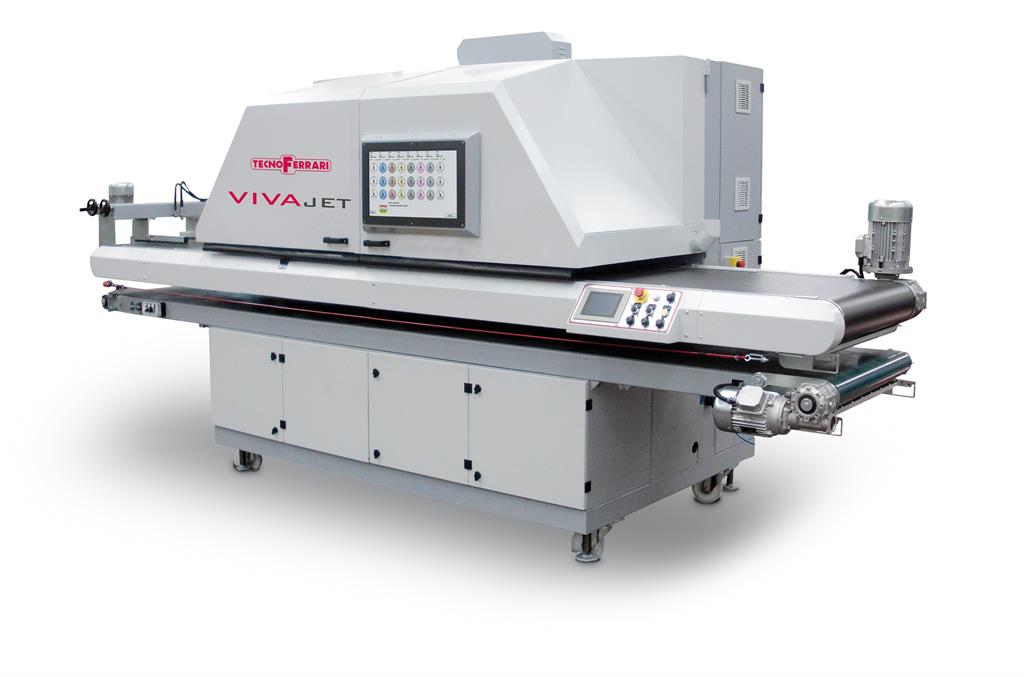
Image courtesy of Xaar: a ceramic tile printing machine
Traditional ‘multiple pass' carriage-mounted printheads move on multiple axes and each axis needs some kind of encoder. The rise of HP's ‘single-pass' Pagewide and Memjet's Waterfall® processes for conventional media has resulted in a paradigm shift in printing technology, but encoder technology has application in this domain too.
It is generally expected that for ceramics greyscale printing will dominate as this allows single pass runs at higher speed, however, many high quality applications will still rely on high DPI resolutions. Colour reproduction in ceramics printing uses a minimum of 4 colours (CMYK), whereby each colour layer is converted into halftones and printed separately.
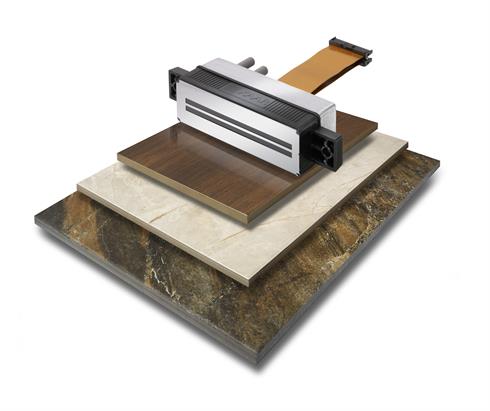
Image courtesy of Xaar: a selection of digitally printed decorative tiles with a single-pass print head
Ultimately, the quality of a halftone image depends on its spatial resolution, grey scale resolution and severity of low frequency artefacts. Halftone dots are formed inside a halftone cell, which produces a single tone, dependant on the size/ frequency of the dots, when viewed by the human eye. Current single-pass printers for ceramics use around 8-10 grey levels which translates to around 3 bits per pixel. By comparison, commercial graphics printers are capable of several hundred grey levels as a result of much higher native print DPI. There appear to be real physical constraints on the native resolution of ceramics printing heads due to the higher viscosity and specific gravity of ceramic inks – which may include glass frit (granulated glass) and heavy metal pigments.
Current native resolutions of inkjet printheads for ceramics are in the 300 to 360 DPI range compared with a standard 2,400 DPI in commercial graphics printing. Lower print resolutions invariably result in reduced LPI, inaccurate reproduction of colours and increased potential for banding in the image and other deleterious effects.
For the highest photographic quality, print heads will require linear / rotational position control to maximise DPI, lines per inch (LPI) and the number of grey levels. By adding one or more motion axes to the full-width printbar it is possible to increase DPI to a level that significantly exceeds the native resolutions of these printers.
Multiple full-width print bars could move perpendicularly to the feed axis in increments of less than the separation between two print nozzles (nozzle pitch). Alternatively several printbars in an array may pivot around the vertical axis to produce any desired resolution. This will allow composite resolutions many times higher than individual print heads. The benefit of using multiple print bars to enhance resolution is that speed is not compromised – the device will remain single pass. Kilns are the most expensive part of the production process and normally run 24/7 with several continuous fast feed lines; single pass printing is essential for handling the continuous stream of newly pressed biscuit tiles.
Clearly, future digital inkjet printers for ceramics will need to be highly flexible devices, in a similar fashion to other high-value mass production equipment, with a greater range of available resolutions, media sizes and increased range of compatible ‘open' inks. Open inks are machine brand independent and have become strong contenders in this industry.
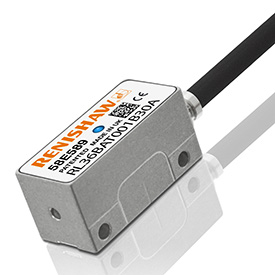
RESOLUTE optical encoder
How do encoders provide better print resolutions and higher quality?
Optical encoders are ubiquitous in quality printing and are expected to become even more so over the next few years. Single pass printers use the latest technologies and are sold at a premium. High-accuracy optical encoders are required for applications in which inkjet print heads move in increments of fractions of the nozzle pitch (20 microns or less) on a linear axis. Alternatively, a rotary application may call for the printbar to rotate about the vertical axis with a minimum accuracy of better than ±5 arc seconds to achieve good dot registration as the substrate passes under a series of similarly orientated printheads. An appropriate optical encoder in the linear case requires a minimum resolution of at least 200 nanometres, assuming dot registration of ± 2 microns, and a specified encoder for the rotary case may feature a minimum resolution of < 0.5 arc sec. Renishaw's TONiC™ incremental optical encoder range would be a good match, alternatively an absolute encoder could be considered. Absolute encoders find position information immediately at switch-on without a reference homing cycle. End-users may find this attractive as it would help to minimise downtime by increasing safety via minimisation of crash risks and general miscounting errors. Examples of optical absolute encoders include Renishaw's RESOLUTE™ absolute series. Print bars will likely hold position on a set point for many hours at a time. Position drift does occur over time due to thermal effects and is particularly pronounced for stepper motor leadscrew combinations, so high-accuracy optical encoders are essential for these types of applications. Ultimately as ink-jet technologies continue to evolve, high-accuracy encoders will become vital system components.
Summary
Developments in ink-jet technology are revolutionising the ceramic tile printing industry. Uptake of wide-format printers for ceramic tiles will increase dramatically over the next few years, which creates an opportunity for the encoder market. Demand for higher quality printing is expected to drive applications for high-performance encoder systems as manufacturers seek to work around inherent technical limitations relating to ceramic inks. Leading motion control solution providers have significant potential to grow and optimise their market share at this time.
For more information about Renishaw position encoders, visit www.renishaw.com/encoders.
Renishaw would like to thank Marco Boer, Vice-President of IT Strategies Inc and a consultant to the digital printing industry, for his expert advice.