Bu sayfa şu anda sizin dilinizde mevcut değildir. Google'ın Çeviri sistemini kullanarak
otomatikleştirilmiş çeviriye
ulaşabilirsiniz. Bu hizmeti sağlamaktan sorumlu değiliz ve çeviri sonuçları tarafımızdan kontrol edilmemiştir.
Eğer daha fazla yardıma ihtiyaç duyarsanız lütfen
bizim ile temasa geçiniz.
Precision position feedback for smart manufacturing
Background
Direct-drive (DD) motor technology has been around for over 40 years, but its widespread adoption has happened only recently. Over the last few years, the cost differential between linear motor systems and traditional ball screw systems has halved.
In recent years, CPC has invested significant resources in motion-control related development projects including linear stages, DD motors, and DD rotary tables – many of which use Renishaw's high-performance linear and rotary (angle) encoders.
RCDM disc scale
Challenge
While the motion-control equipment market continues to see strong growth, competition remains fierce. Manufacturers need to stand out in a crowded marketplace in order to break through.
James Wu, R&D Department Manager at CPC, explains his company's strategy:
“We started out as a miniature guide rail manufacturer and we are a leading player in this market with more than half of our revenues coming from guide rail products.”
He continues, “In recent years, we have seen growing demand for direct-drive motors and associated components, and we have also invested more resources in this area, which now accounts for around 70% of our total R&D expenditure.”
“In a crowded marketplace, efforts to minimise production costs are essential. Most of our machine components, motors and drivers are developed and manufactured in-house. Our biggest challenge is ensuring that our motors are competitive,” adds Mr Wu.
He concludes, “In terms of the parts we buy in, we keep our costs as low as possible by looking for high-performance parts that offer good value for money. We also develop our own motion control software that meets a wide range of customer requirements. Product customisation will become increasingly important as we enter the new Industry 4.0 era.”
Renishaw optical encoders have provided us with extremely reliable performance for many years, along with specifications that meet all our customers' needs.
Chieftek Precision Co. (Taiwan)
Solution
CPC uses Renishaw's optical encoders in much of its extensive family of motion products, including its RP range of mini DD rotary stages. These stages have an outer diameter of 120 mm, a minimum thickness of 37 mm, and are supplied with several different options for position encoder feedback. Options include CPC's in-house magnetic encoders and Renishaw's ATOM™ optical encoders, depending on the level of precision required by the customer.
While large rotary tables are used in machine tools, mini DD rotary tables are mainly used in applications where high levels of speed and precision are needed, such as industrial automation, semiconductor and FPD manufacturing equipment.
As Mr Wu explains: “We have worked with Renishaw for nine years now and we generally use Renishaw optical encoders. Our RP-series rotary tables use Renishaw ATOM™ encoders with a 40 μm pitch scale and a disc diameter of 50 mm, providing an output signal with an angular resolution of ±1.8 arc second. When you look at the ATOM readheads or glass discs, they are designed to be extremely light and thin, which makes them ideally suited to the requirements of applications like mini rotary tables where space is limited.”
Renishaw's ATOM miniature optical encoder family, has readheads measuring just 7.3 x 20.5 x 12.7 mm. It is one of only a handful of integrated miniaturised optical encoders available on the market and features leading-edge signal stability, dirt immunity and reliability.
ATOM optical encoder in a mini rotary platform application
The ATOM encoder's RCDM rotary scale is a one-piece glass disc featuring scale graduations marked directly on the disc face with a single reference mark, and an optical alignment ring. The optical alignment ring can be used to minimise angular alignment errors and improve installed accuracy. ATOM is a non-contact optical encoder with an open format, the advantages of which include the effective elimination of backlash, shaft wind-up (torsion) and other mechanical hysteresis errors that are inherent in traditional enclosed encoders.
During installation, the mounting surface can be fixed under the disc, but must be aligned with the centre of the disc before bonding. This calibration is generally done using electronic or optical methods. Electronic calibration involves monitoring output signals from two readheads installed at a 180° angle from each other, and then adjusting the disc to minimise the difference between the readings from the two readheads (adjustment tools include two ATOM readheads and a Renishaw DSI interface). Optical calibration uses a microscope to manually align the position of the disc with the centre of the mounting surface.
Mr Wu continues: “During installation, we bond the disc onto the mount with UV-cure glue and use a microscope to align the centre of both to minimise eccentricity; after that is done, the assembly is exposed to a UV lamp to solidify the bonding glue. ATOM discs are marked with an ‘alignment ring', so that calibration can be performed by observing changes in ring displacement using a microscope during manual rotation, making the calibration process straightforward.”
He adds, “On the quality control front, we use Renishaw XL-80 laser interferometers to check the accuracy of our motion products, and we are also considering whether to add a few more units to cope with demand from increasing orders and new factories. In addition to using ATOM readheads in our rotary tables, we also use a number of other Renishaw encoders. For example, we use RGH series encoders in our linear platforms, and RESOLUTE™ absolute optical encoders in large rotary table applications. We are also testing optical encoder systems that can operate in vacuum environments.”
Results
The quick and easy installation and set-up procedures of Renishaw's compact encoders enable CPC to build competitive DD products without sacrificing quality and performance.
Mr Wu says, “Renishaw optical encoders have provided us with extremely reliable performance for many years, along with specifications that meet all our customers' needs. The dirt immunity is also superior to other encoder brands. It is very rare for us to experience any issues, and the customer service is also excellent. Encoder set-up is very simple, as you basically just need to look at the colour of the LEDs on the readhead to check that it's been successfully installed.”
He concludes, “Direct-drive technology will become the mainstream due to its advantages in terms of precision, efficiency, high response rates, and durability. As we enter the Industry 4.0 age, the compatibility of hardware with systems, and the issue of whether they can communicate with each other, will drive the biggest trends in the development of motion control products. For this reason, CPC will continue to invest more resources in this area in future.”
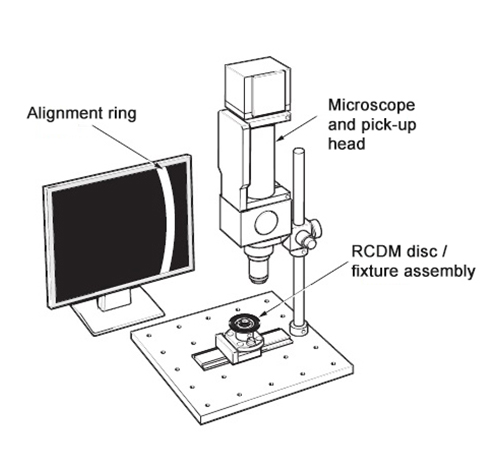
Using a microscope to align the disc with the centre of the mount