Bu sayfa şu anda sizin dilinizde mevcut değildir. Google'ın Çeviri sistemini kullanarak
otomatikleştirilmiş çeviriye
ulaşabilirsiniz. Bu hizmeti sağlamaktan sorumlu değiliz ve çeviri sonuçları tarafımızdan kontrol edilmemiştir.
Eğer daha fazla yardıma ihtiyaç duyarsanız lütfen
bizim ile temasa geçiniz.
Gauging system accelerates COVID-19 test kit production
In the race to combat the global COVID-19 pandemic, the distribution of coronavirus test kits became a very high priority. For mass production of plastic test kit components, manufacturers could not afford metrology processes to become bottlenecks. Verus Metrology Partners was tasked by its customer to increase metrology throughput to keep pace with part production.
Background
Verus Metrology Partners is a leading provider of bespoke turnkey metrology solutions. It specialises in the measurement of complex plastic component geometries, and serves customers in a variety of sectors, most notably MedTech, pharmaceutical and FMCG (fast-moving consumer goods).
The company's comprehensive metrology service comprises fixture design and manufacture, qualification, validation and programming, Moldflow analysis, installation and aftercare. It has developed a global reputation for innovation, enabling dramatic increases in metrology machine efficiency through integrated metrology solutions.
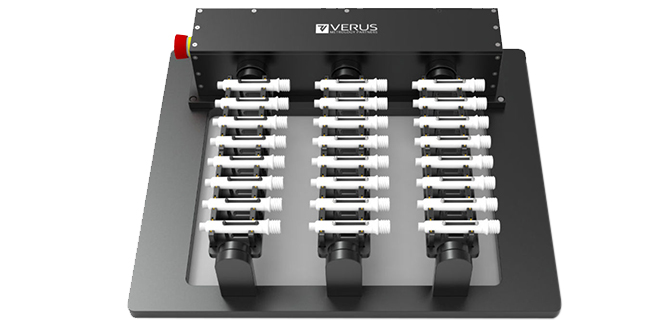
One of Verus Metrology Partners, bespoke fixture solutions
Challenge
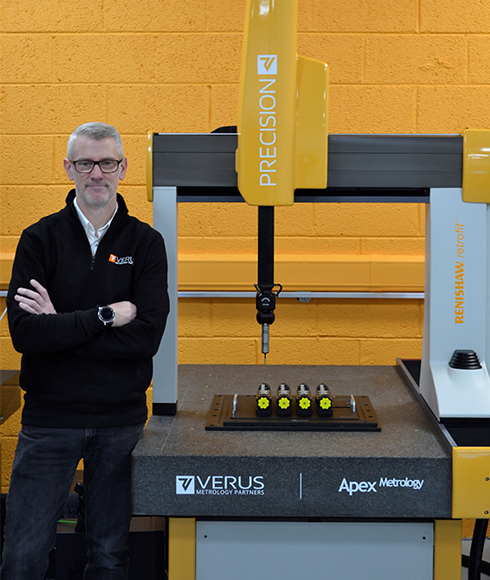
Michael Nugent, Verus Metrology Partners' Chief Operating Officer with Verus' first Renishaw CMM Retrofit
At the height of the global coronavirus pandemic, Verus Metrology Partners was approached by the American medical-grade container manufacturer SiO2 Materials Science (SiO2) to help increase the throughput of a metrology process critical to the volume manufacturing of COVID-19 test kit components.
SiO2 is an advanced materials science company with deep roots in chemistry and engineering. The company is dedicated to producing step-change innovative solutions via advanced proprietary materials science. It is renowned for bringing the benefits of glass and plastic together without drawbacks.
SiO2 tasked Verus Metrology Partners to provide high-speed batch inspection of two quite different test kit components: a vial and a cap. Along with the inspection of the components, the provision of live inspection data recording was an essential requirement.
Verus Metrology Partners' Chief Operating Officer, Michael Nugent, said, “In this instance, time really was of the essence - in every sense. Not only did our metrology solution have to be developed in a short time frame, but it needed to repeatably and accurately measure critical component dimensions at the highest possible speed.”
He continued, “Social distancing measures and severe restrictions on both national and international travel of course presented a further challenge. A pragmatic solution was needed, one that made the best use of existing on-site inspection equipment and adapted it to work hyper-efficiently within a turnkey metrology system.”
Combining high-speed, automated gauging systems, like Equator™ 300, with multi-station component inspection routines allows an operator to maximise the time they have available to produce parts and minimise the time taken to inspect them, leading to more efficient and productive use of their time, which maximises ROI.
Verus Metrology Partners (Ireland)
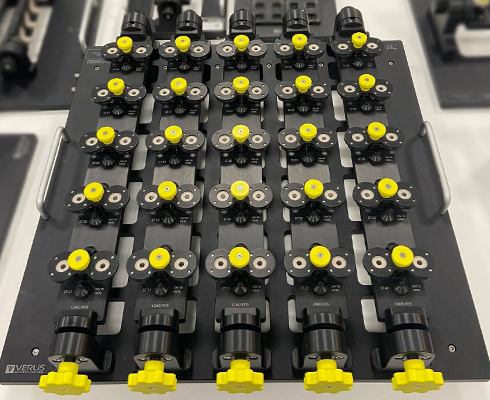
A bespoke Verus 48-station fixture for measuring soft rubber components
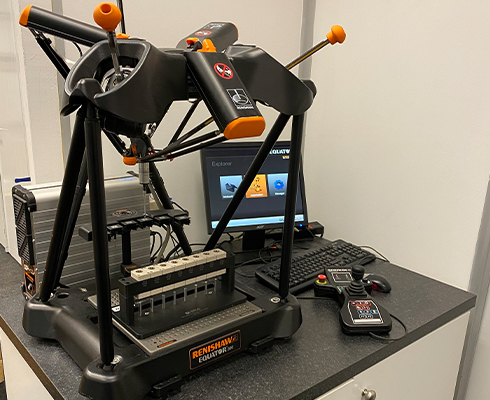
One of Verus Metrology's fixturing designs holding tubes and caps for inspection on the Equator 300 gauging system
Solution
SiO2 had recently purchased an Equator™ 300 gauging system from Renishaw, which was not yet integrated into its metrology processes. Verus Metrology Partners considered the Equator gauge the perfect fit with its metrology solution.
Michael said, “We were already aware of the capabilities of the Equator gauge, having put the gauging system through its paces in our R&D facility. In particular, we knew that it was capable of rapid inspection of parts.”
Comprising a programmable comparator gauge, controller, inspection probe and application software, the Equator 300 system is suitable for accurate inspection of medium to high volume parts.
Michael continued, “The working volume of the Equator 300 gave us the start point. Our solution would need to fit within the Equator 300 gauge's working volume of 300 mm diameter and 150 mm height. When you know that a gauging system like Equator can perform very fast inspection routines, then the challenge quickly becomes: how can we get the most out of it? Inspecting single components one-by-one, even using some kind of shuttle system to load and unload, was just too slow and cumbersome. Given the relatively small size of each of the two components, we determined early on that multi-station fixturing was perfectly viable and would give us the means to achieve the increased speed objective.”
Working in hard anodised aluminium and medical grade plastic, Verus Metrology Partners designed and manufactured a bespoke 8-station fixture for each different component. This repeatedly presents tubes and caps into fixed positions within the working envelope, ready for probing.
Michael commented, “The fixturing here plays a critical role. Not only does it need to present the Equator gauge with all the access it needs to inspect the two or five critical dimensions on each component, but it also needs to avoid any deformation of the component. It needs to support robust, repeatable metrology and can't jeopardise the geometry or integrity of the component being measured – be it vial or cap.”
Component gauging routines for the two different test kit component fixtures were developed by Verus using Renishaw's MODUS™ gauging software on the Equator Controller.
All of the system's metrology data is shared with QC-CALC statistical process control software in real time. It can be printed and stored locally, while an immediate Pass-Fail indication is graphically displayed to the machine operator.
Results
By integrating an Equator 300 gauging system with bespoke multi-station fixturing, Verus Metrology Partners has succeeded in dramatically reducing the batch release times of SiO2 Materials Science's COVID-19 test kit components. Once programmed, the Equator gauge executes the inspection routine at the push of a button. An operator simply loads the vials or caps onto the relevant component fixtures, sets the inspection program running on the Equator gauge and can leave it to inspect eight components at a time.
Michael comments, “More and more attention is turning towards ensuring that all production personnel have roles and responsibilities that add real value to the business. Combining high-speed, automated gauging systems like Equator gauge with multi-station component inspection routines allows an operator to maximise the time they have available to produce parts and minimise the time taken to inspect them, leading to a more efficient and productive use of their time, which maximises ROI.”
“It is often the case that clients approach us looking for fixturing and metrology solutions that will serve them for a 20-year product lifecycle. And we say that our systems will frequently surpass the lifetime of the parts they're designed to hold. In this particular instance of course, we sincerely hope a far shorter time frame will be required.”
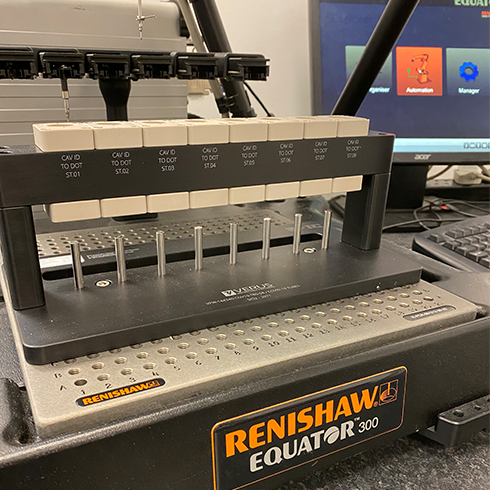
One of Verus Metrology's fixturing designs holding tubes and caps for inspection on the Equator™ 300 gauging system