Codeurs hermétiques de Renishaw utilisés dans une nouvelle machine-outil hybride de fabrication additive et soustractive
L’équipe d’Effective CNC Solutions a conçu et construit une machine « tout-en-un » capable d’effectuer en tandem des opérations d’usinage additif et soustractif.
Contexte
Effective CNC Solutions LTD est une entreprise basée à Crewe, au Royaume-Uni, spécialisée dans le rétrofit sur machine-outil. Il y a quelques années, Gary Pearson, directeur et fondateur de l’entreprise, a eu l’idée de mettre au point une machine-outil capable de combiner fabrication additive (AM) et fabrication soustractive classique en un seul et même procédé sur la même machine.
La fabrication additive est une technologie de fabrication polyvalente qui permet de produire une grande variété de formes quasi-définitives, fonctionnelles complexes. Elle offre de nouvelles possibilités de conception prometteuses pour combiner et optimiser les pièces, en réduisant potentiellement les coûts d’outillage et de matériaux.
Gary Pearson, Directeur d'Effective CNC
Bien que la fabrication additive permette de produire de nombreuses pièces en un seul procédé, certaines entités ou surfaces fonctionnelles peuvent nécessiter un post-traitement supplémentaire, comme des opérations d’usinage ou de finition à CN, afin d’obtenir des pièces finales avec des spécifications fonctionnelles complètes.
L’un des objectifs majeurs de la fabrication additive est de rendre ces étapes de post-traitement aussi rapides et simples que possible.
Pour aider Effective CNC à concevoir et à construire sa nouvelle machine, Renishaw a apporté le soutien de ses équipes d’experts en codeurs optiques de position, systèmes de réglage d’outils et palpeurs pour machines-outils.
Effective CNC a sélectionné une gamme de produits Renishaw, notamment la série de codeurs linéaires hermétiques FORTiS™, le palpeur RMP60 et un système de réglage d’outils sur mesure pour construire un prototype de machine qui intègre la fabrication additive et le post-traitement de certaines pièces métalliques.
Défi
Lors du post-traitement des pièces issues de la fabrication additive, la propagation d’erreurs géométriques peut avoir un impact sur la précision de la surface usinée du produit final.
La finition de pièces obtenues par fabrication additive implique souvent plusieurs transferts de machine qui peuvent introduire des erreurs de position et angulaires des pièces à usiner. Il devient alors nécessaire de compenser ces erreurs à l’aide de systèmes de palpage montés sur machine. L’utilisation de plusieurs machines a également un impact négatif sur les coûts et la productivité.
Les machines hybrides, qui combinent à la fois des machines-outils classiques et une tête de fabrication additive, sont un concept relativement nouveau qui peut améliorer la rentabilité de la fabrication additive pour certaines applications.
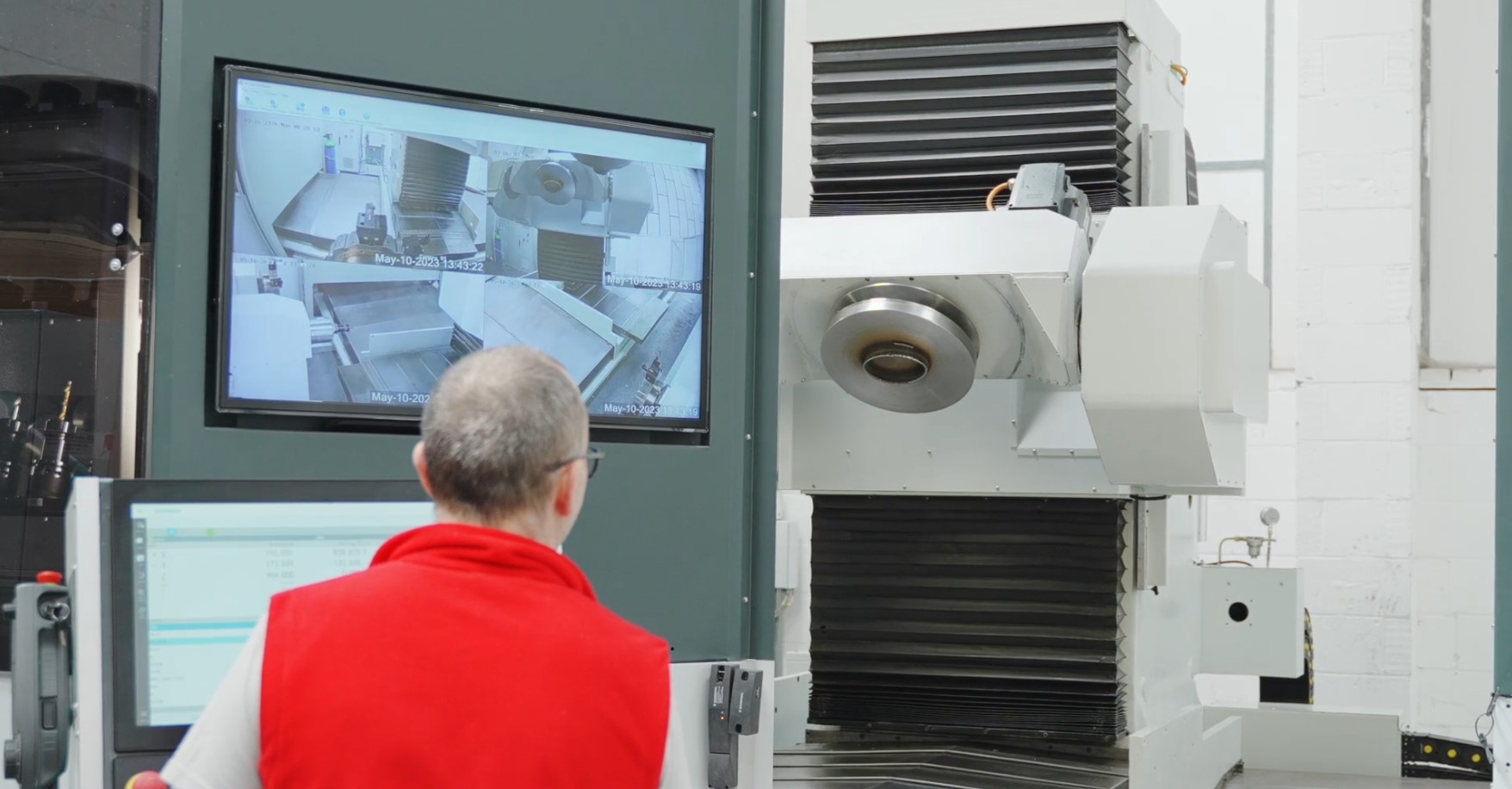
Solution
L’équipe d’Effective CNC a conçu et construit une machine « tout-en-un » capable d’effectuer en tandem des opérations d’usinage additif et soustractif. Selon elle, cette machine contribuera à révolutionner la rentabilité de nombreuses grandes constructions métalliques de précision par AM.
Gary Pearson, directeur d’Effective CNC, explique les caractéristiques uniques de la nouvelle machine :
« Nous avons créé une position fixe et rigide pour une broche et une tête de fabrication additive par dépôt de fil, auxquelles nous avons ajouté une tourelle de tournage.
Nous pouvons déplacer la pièce à usiner sur les cinq axes et entre les différents postes pour ajouter et soustraire de la matière de façon répétée sans avoir à déplacer l’outillage.
Nous avons choisi un système de fabrication additive par dépôt de fil, à savoir un système de soudage MIG intelligent, que nous avons placé sur la machine dans une position fixe. Cela nous permet d’apporter le matériau de base sur un plateau de fabrication propre, puis de l’usiner à nouveau sans avoir à retirer le produit de la machine.
Comme nous avons la possibilité d’ajouter de la matière sur les cinq axes de la machine, nous pouvons concevoir des formes très complexes et les réusiner avec des tolérances très précises, sans avoir à les retirer de la machine. »
Une autre caractéristique innovante de cette machine est qu’elle intègre trois procédés de coupe : fraisage, tournage et rectification, en plus du traitement additif, ce qui permet de créer et de finir une pièce par fabrication additive sur une seule machine.
La conception de base de la machine comprend le support de la pièce à usiner, une broche de fraisage et de rectification ainsi qu’une tourelle de tournage rotative. Les 4e et 5e axes de la machine sont assurés par une table à tourillons qui supporte le plateau de fabrication.
Pour améliorer la sécurité de la machine-outil, les composants tels que l’automate et les codeurs de position ont été choisis conformément aux normes de sécurité fonctionnelle (FS).
Effective CNC a choisi des codeurs fermés FORTiS-S™ FS pour les axes X, Y et Z, notamment un codeur FORTiS long (axe X) conçu sur mesure avec une longueur de règle de plus de 3 mètres. Pour la table à tourillons (axe A), un codeur de position optique absolu RESOLUTE™ FS de Renishaw muni d’une règle annulaire RESA a été choisi pour la lecture de position rotative.
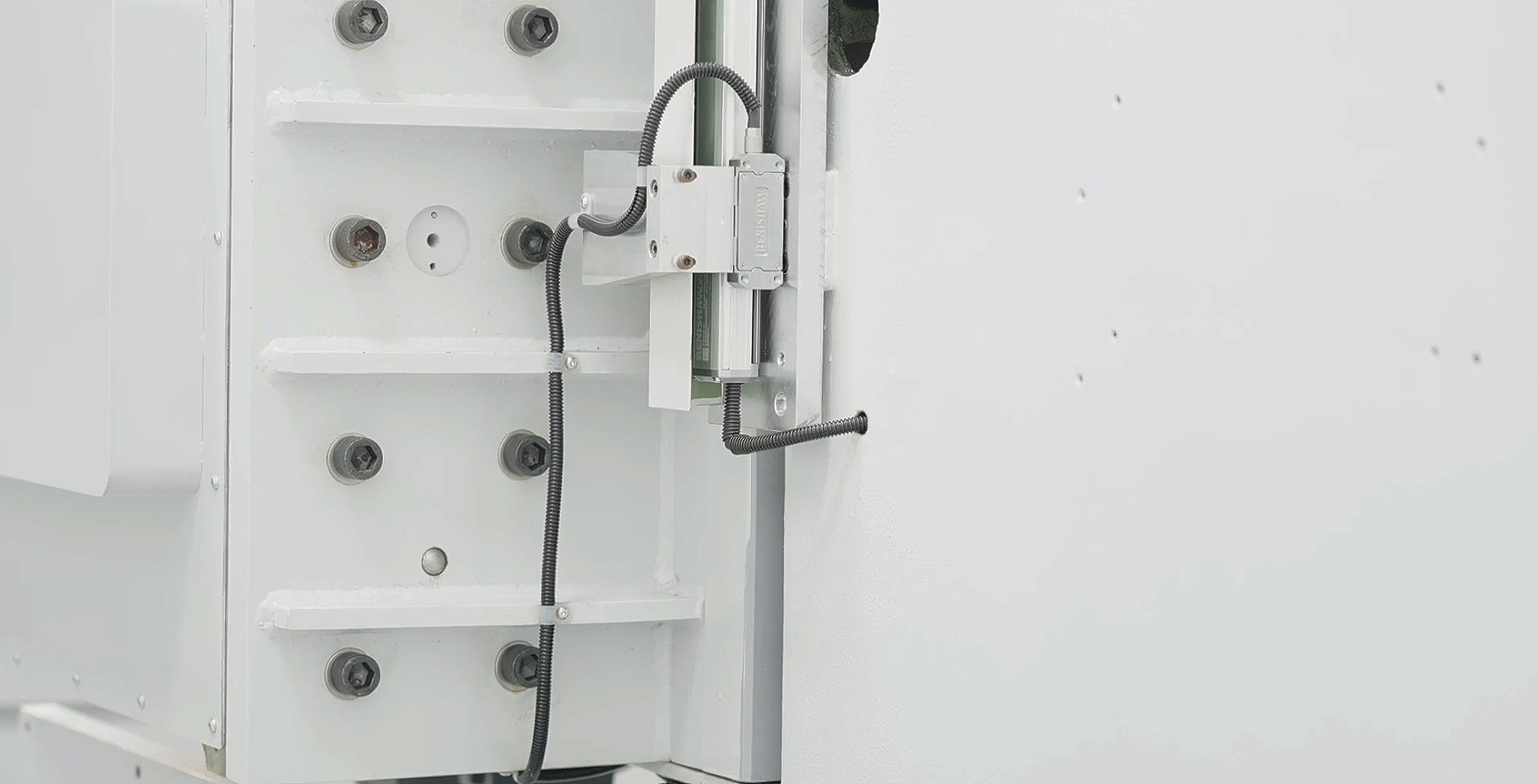
La série de codeur FORTiS est une nouvelle génération de codeur de position absolu hermétique linéaire destiné à être utilisé dans des environnements exigeants tels que des machines-outils. Un avantage du codeur hermétique FORTiS réside dans la rapidité de son installation et de son réglage, qui est nettement supérieure à celle des systèmes classiques, même dans les endroits difficiles d’accès.
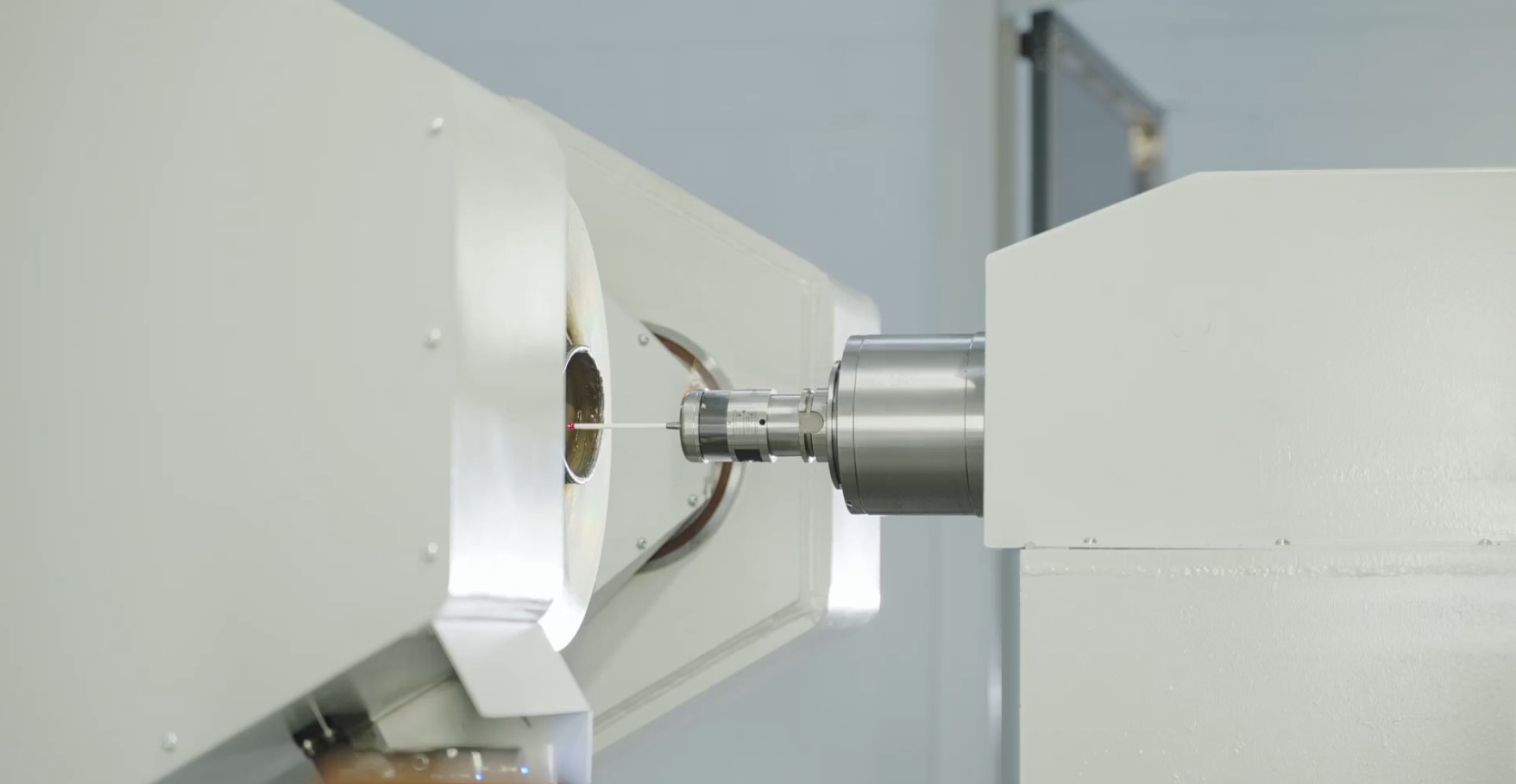
Gary Pearson explique l’intégration des produits Renishaw dans chaque procédé machine :
« Nous avons acheté deux systèmes FORTiS, prêts à l’emploi et très faciles à installer et à régler. Renishaw nous a également fourni un système de palpage RMP60 pour la mesure des pièces à usiner, qui fonctionne vraiment très bien. Son équipe a également développé pour nous un système hybride, qui combine un système laser de réglage d’outil NC4+ Blue pour les opérations de fraisage et un palpeur de réglage d’outil RP3 pour les opérations de tournage.
Et Gary Pearson de poursuivre : « Des experts techniques nous ont demandé ce que nous faisions sur la machine, où nous voulions installer le système de réglage d’outil et ce que nous voulions réaliser, puis ils ont dessiné les modèles de CAO.
Nous avons pu intégrer ces modèles de CAO dans notre propre modèle de CAO de la machine et voir comment ils s’intégraient. C’était exactement ce dont nous avons besoin ! »
L’approche innovante adoptée par Effective CNC s’étend également au-delà du format de la machine et de l’outillage. Un nouveau robot de changement d’outil a également été développé. « Plutôt que de construire un robot cartésien avec une structure complexe de changement d’outil, nous avons choisi une solution prête à l’emploi basée sur un robot collaboratif », poursuit Gary Pearson.
Le robot choisi est d’Universal Robots et ses articulations sont équipées de codeurs rotatifs magnétiques de la série AksIM™ de RLS, une société associée de Renishaw. Associé à un changeur de palettes, le robot permet à la machine de fonctionner en mode entièrement automatisé, sans aucune intervention de l’opérateur.
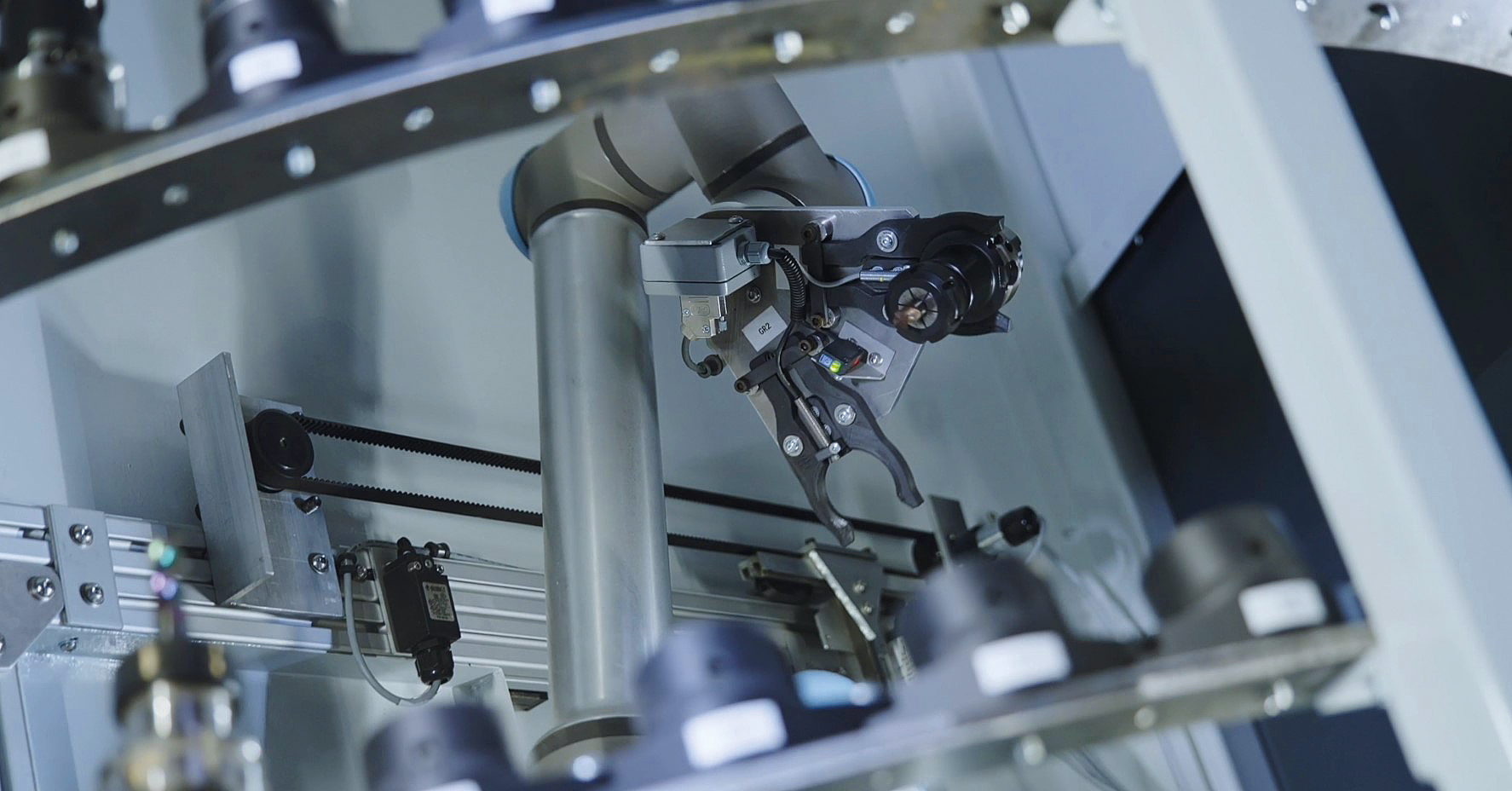
Résultats
Une étroite collaboration avec Effective CNC a permis à Renishaw de mettre à profit ses 50 ans d’expertise dans le secteur des machines-outils pour aider à choisir les technologies les meilleures et les plus récentes pour ce concept de machine.
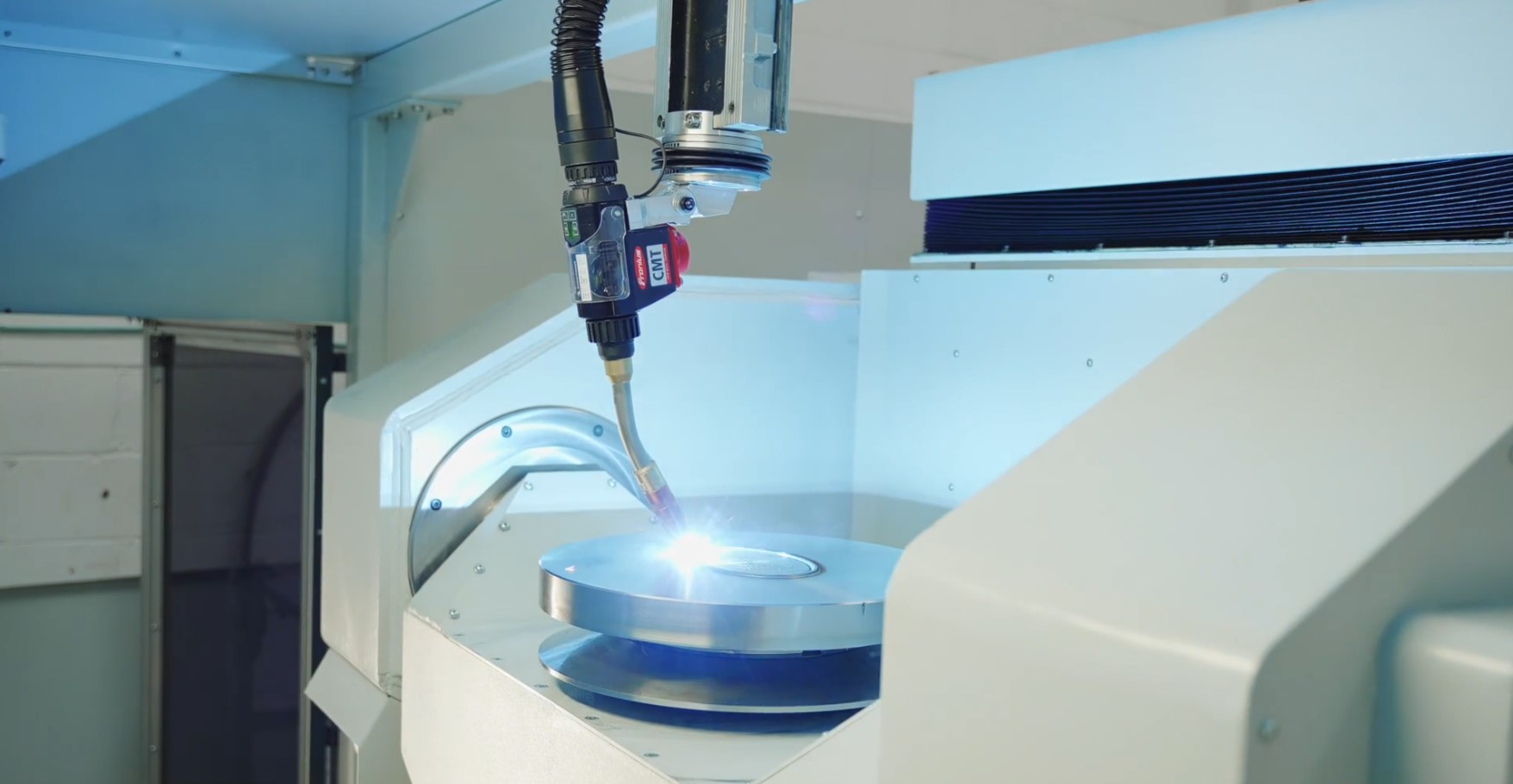
« En termes de fabrication additive, comme nous pouvons fabriquer sur cinq axes, nous pouvons créer des composants plus grands que la table de la machine. Nous pouvons fabriquer un cylindre et pivoter autour pour fabriquer sur son côté la forme de notre choix. Et cela nous offre la possibilité de fabriquer des composants de grande taille qui dépassent même le plateau de fabrication. »
Cette machine est un système polyvalent qui combine avec succès fraisage, tournage et rectification avec un système de fabrication additive, ce qui augmentera considérablement la productivité du procédé de bout en bout et permettra la création par AM de pièces métalliques difficiles telles que des coudes et des raccords de tuyauterie surdimensionnés pour le secteur du pétrole et du gaz.
« Nous avons le sentiment d’avoir un produit novateur et fort pour les entreprises de haute technologie et nous envisageons l’avenir avec beaucoup d’optimisme », conclut Gary Pearson.
Renishaw continue de soutenir l’équipe d’Effective CNC dans sa préparation de la prochaine phase de développement de produits.