Cette page n'est pas disponible actuellement dans votre langue. Vous pouvez en afficher une traduction automatique avec l'outil Google Translate. Cependant nous déclinons toute responsabilité quant à ce service et nous ne contrôlons pas les résultats de la traduction.
Pour en savoir plus à ce sujet, contactez-nous.
The Primo™ system reduces part set-up time for Victory Precisions from hours to seconds
Victory Precisions Pvt. Ltd., Pune, India,manufactures aluminium diecastings and large machined engineering components for companies in the oil and gas, automobile, agricultural, infrastructure, and other sectors. It is critical to maintain an accuracy of 15-20 microns on these components and reduce non-productive time while machining. The Primo™ system, developed by Renishaw, has helped Victory Precisions to achieve this accuracy, reduce part setting time and increase productivity.
Victory – the one-stop solution company
Victory Precisions was established in 2006 and supplies components to well-known companies such as ABB, Alfa Laval, Atlas Copco, Cummins, and many others across the globe. The company has a workforce of 165 people consisting of engineers, designers, operators, and other staff. It registered a turnover of INR 250 million in the financial year 2013–2014.
The well equipped aluminium die-casting foundry has an E6 heat treatment plant, a drop quench facility, core shooters and shot blasting machines providing the capacity to produce 100 tonnes of castings every month.
The machine shop has 14 twin pallet horizontal machining centres (HMCs), three vertical machining centres (VMCs), two CNC vertical turning lathes machines (VTLs), turning centres, co-ordinate measuring machines (CMMs) and comprehensive inspection facilities. It is an ISOTS certified company and a proud Zero PPM supplier to all of its customers. The company is a one-stop solution for its customers as it has the facilities for making dies, patterns, castings, and extensive machining capacity.
The Primo system – a big saver for Victory
Victory Precisions was incurring huge losses in terms of time and material until it started using Renishaw's Primo system. The Primo system which consists of a Primo Radio Part Setter and a Primo Radio 3D Tool Setter, is available at a competitive price, and is aimed at delivering a fast return on investment. It enables automated on-machine part setting, part inspection and tool setting, helps to eliminate manual setting errors, and improves accuracy and part conformance whilst reducing non-productive time and scrap. This helps to increase productivity, improve quality, and increase profits.
The Primo system is easy to use, simple to install and represents a low initial financial outlay. Additionally, its exclusive, enhanced warranty offers users peace of mind. The innovative Primo Credit Token system offers users the flexibility to ‘pay-as-you-probe'. Its 6-month renewable tokens allow unlimited use of the Radio Part Setter and the Radio 3D Tool Setter within this period of time. The credit tokens are also available as an upgrade to enable unrestricted continuous use.
A key benefit is the elimination of the need for extensive G-code knowledge. The system is supplied with GoProbe, an innovative ‘all-in-one' software package that simplifies part setting, tool setting and calibration. Simple, single-line commands are used instead of multiple lines of code which further eliminates the need for any
special training.
While it is revolutionary, installing the Primo system is also very easy. Renishaw installed it within one and a half hours at Victory Precisions and the operators were trained to operate the probe in just three hours using Go Probe. Requiring no previous experience of probing, GoProbe makes the probe system easy to understand and use.
Victory Precisions (India)
Going with the best
“We were introduced to Renishaw in 2007, when we decided to install probes in our manufacturing unit. The selection parameter was to go with the best supplier and Renishaw, being best in class and category, was a natural choice for us. Today, we have seven different probing systems from Renishaw,” said Mr Sagar Kaushik, the Director of the Victory Precisions.
The company felt that the Primo system suited various applications and installed it on one of its HMCs. “While it is revolutionary, installing the Primo system is also very easy. Renishaw installed it within one and a half hours at Victory Precisions and the operators were trained to operate the probe in just three hours using Go Probe. This combination of software, self-learning material and reference tools is standard with the Primo system. Requiring no previous experience of probing, GoProbe makes the probe system easy to understand and use.”
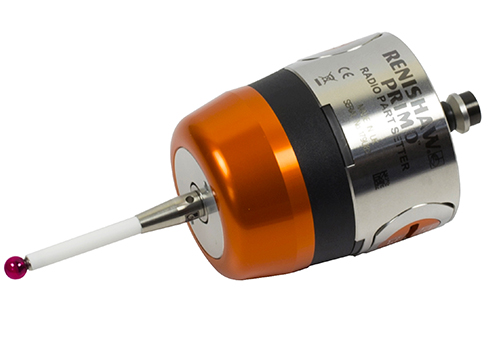
Time saved is money earned
At Victory Precisions, the Primo system has helped to save time and eliminate scrap. When machining a crankcase – a critical product for any engine – some casting process variations are often present. At Victory Precisions, in order to get equal wall thickness and avoid future failures, the component would be set up on the machine and bore alignment would be performed manually using dial gauges. Before the Primo system was installed this part setting process took two and a half hours and caused machine downtime. With the Primo system, the on-machine alignment of a crankcase takes just 5 to 10 seconds, saving time and costs. In addition, scrap is eliminated – a saving of INR 45,000 per component – and precision is guaranteed.
When machining a cylinder – an engine component and a high-performance part – concentricity is critical. Once the boring operation is performed, checking of concentricity is essential and previously it was necessary to take the product to another inspection facility, which led to a delay in the machining cycle. This entire process took one and a half hours. The Primo system enabled the inspection of this parameter to take place on the machine itself, and in just 30 seconds, without a gap in the machining cycle.
A bonnet – an oil and gas industry component –is very heavy and the cost of the raw forging is high. After machining the diameter and other operations are performed on a VTL, the component is set to within an accuracy of ±10 microns of the centre axis on an HMC, for middle hole boring, PCD holes and threading operations. This alignment was previously carried out by using a dial gauge and it took around two hours. After installing the Primo system, it took a minute to perform this alignment, resulting in a significant time-saving and confidence in the alignment.
Another critical component where the Primo system has helped in maintaining accuracy and reducing rejections is the air intake manifold used in automobile engines. This component comes in different sizes and can be very long. When a manifold is cast, there is normally a distortion of 1 mm to 2 mm. Correct alignment is very important when machining, so that bored and clamping holes are machined as per the drawing. The Primo system probes port holes on the casting and aligns the component perfectly. It takes wall thickness variations into account, leading to a total time saving of ten minutes and the elimination of scrap.
Mr Kaushik is clearly impressed with the Primo system: “The software is very simple: the operators using the Primo system can be trained in 30 minutes and find it very easy to use this product. The advantage is its probe-on-probe calibration and the credit token system, which is a unique payment system that Renishaw has offered. We do not have to pay everything at one time and as such, higher initial investment is avoided. We can buy credit tokens as and when we want to use Primo. It is like a prepaid system that is a low cost solution for SMEs.”
The Primo system comes with Primo Total Protect cover, a comprehensive warranty scheme which safeguards the probes against any accidental damage. “Primo is surely recommendable for any shop floor and is beneficial to each and everyone,” Mr. Kaushik concluded.