Simplifier la fabrication additive d'implants rachidiens
La multinationale d'ingénierie Renishaw a collaboré avec deux entreprises de technologie novatrices pour illustrer ce que la fabrication additive métallique (AM) peut faire dans la production d'implants rachidiens légers imitant les propriétés mécaniques de l'os. Dans le cadre de ce projet, l'entreprise de recherche en fabrication Irish Manufacturing Research (IMR) a conçu et fabriqué une série d'implants rachidiens représentatifs. IMR a conçu les implants avec un logiciel nTopology et les a fabriqués sur une machine de fabrication additive métallique Renishaw RenAM 500M.
Contexte
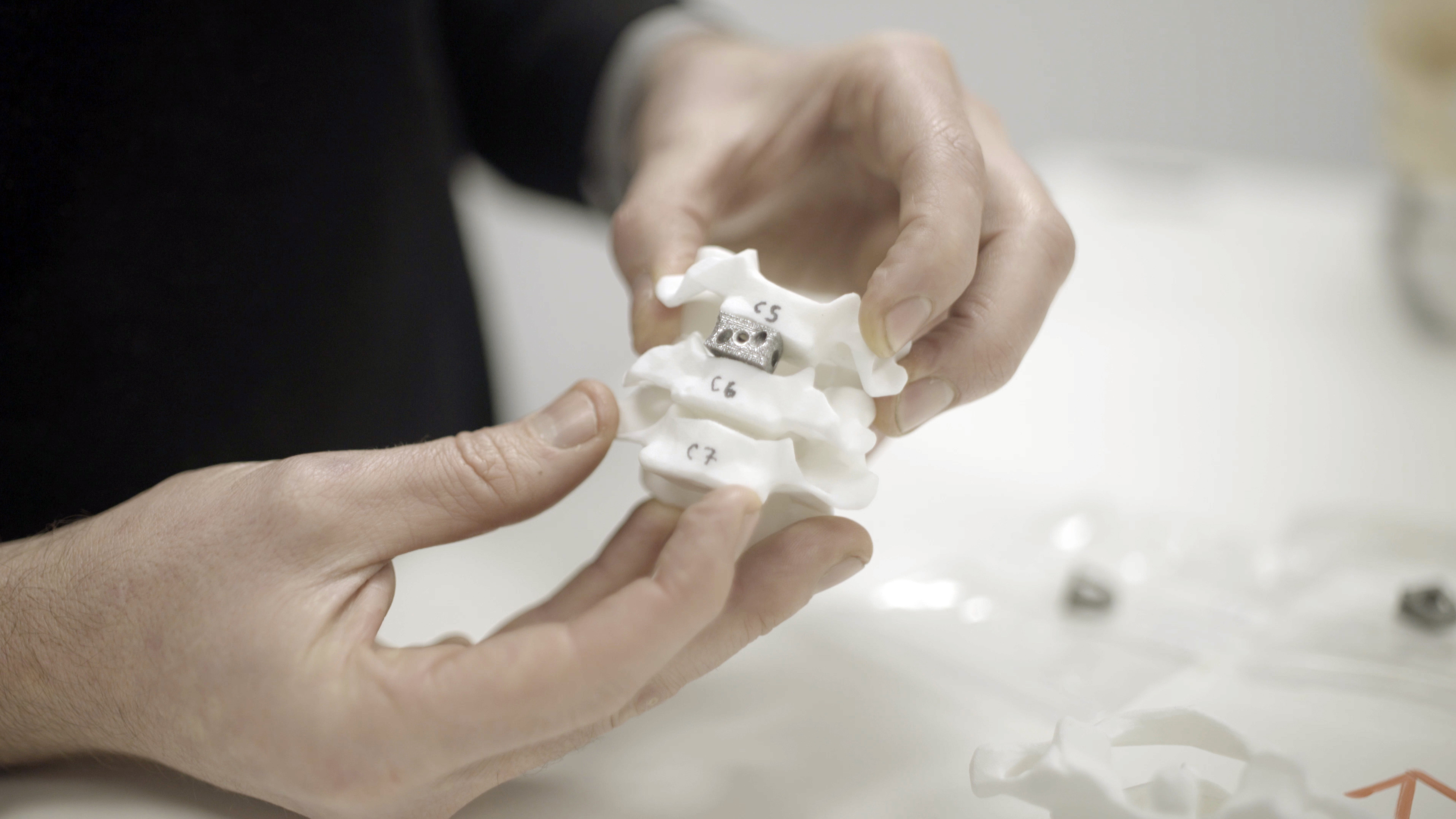
Implanté à Dublin, IMR apporte aux sociétés de fabrication irlandaises l'assistance dont elles ont besoin pour se préparer à la fabrication numérique nouvelle génération. En Irlande, la production de dispositifs médicaux est un secteur important, et IMR étudie, avec diverses entreprises, ce qui peut être réalisé avec des dispositifs médicaux imprimés en 3D.
Implantée à New York, nTopology est une entreprise de pointe dans le domaine de la conception générative qui a mis au point des logiciels techniques de conception nouvelle génération pour la fabrication avancée. La plate-forme logicielle inédite nTopology permet la création de modèles complexes et performants qui tirent pleinement parti des fonctionnalités de la fabrication additive.
Ces conceptions avancées peuvent être créées en plusieurs minutes et non en plusieurs jours. La plate-forme nTopology permet de capturer les workflows d’ingenierie, les processus de fabrication et le savoir à l'intérieur du logiciel. Les utilisateurs peuvent ainsi créer des workflows personnalisés répondant à leurs besoins précis.
Les implants rachidiens sont nécessaires pour rétablir la hauteur intervertébrale chez des patients atteints de pathologies suivantes : discopathie dégénérative, hernie discale, spondylolisthésis, sténose spinale et ostéoporose.
Grâce au soutien que nous avons reçu de Renishaw dans le cadre des implants rachidiens ainsi que d'autres projets, nous avons accru les compétences de notre personnel et nous sommes désormais bien établi dans le domaine de la fabrication additive.
Avec nous, Renishaw a travaillé sans relâche à l'amélioration du processus de fabrication additive pour les implants rachidiens. Ensemble nous avons conçu des expériences générant les paramètres optimaux pour le produit. Nous avons ainsi pu réduire d'un facteur de dix la part de post-traitement exigée sur les fonctionnalités principales."
Irish Manufacturing Research (IMR) (République d'Irlande)
Challenge
Les techniques de fabrication conventionnelles ne sont pas en mesure de produire des implants rachidiens avec une structure lattice. Cette structure offre une grande surface qui favorise la migration des ostéoblastes dans l'implant et permet d'optimiser les propriétés mécaniques d'un volume poreux pour répondre aux conditions de charge requises.
IMR a trouvé dans la fabrication additive métallique une méthode adéquate pour fabriquer des structures lattices optimisées pour l'ostéo-intégration. Il fallait toutefois identifier le logiciel de conception et les machines de fabrication additive qui conviendraient le mieux.
"Les capacités des moyens de fabrication additive se sont développées rapidement et dépassent désormais celles des outils de conception conventionnels, explique Duann Scott, Directeur du développement commercial et des partenariats chez nTopology. nTopology a été créé en 2015 quand son fondateur s'est rendu à l'évidence qu'aucun logiciel ne pouvait concevoir les géométries complexes que la fabrication additive était capable de produire.
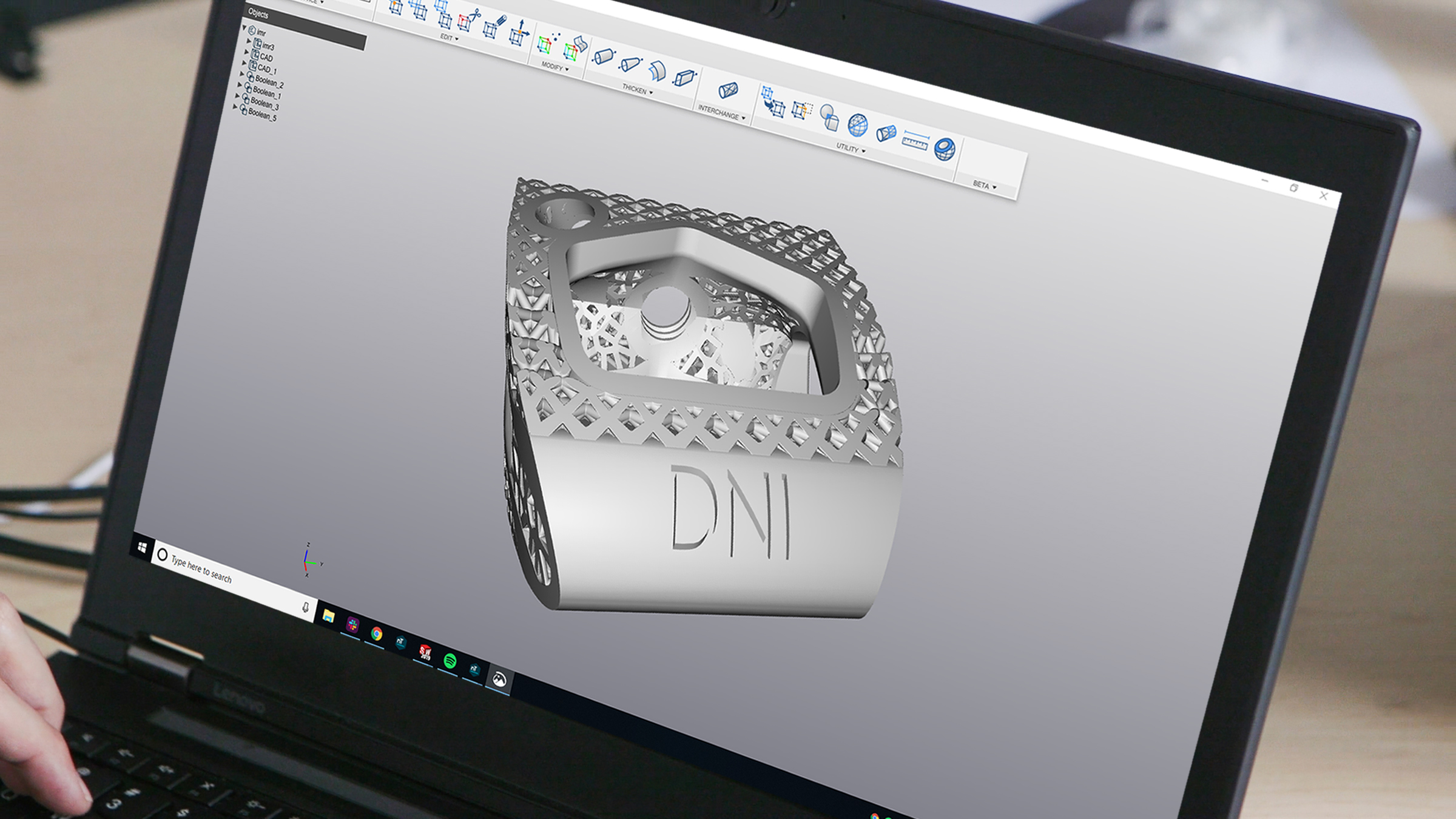
Pour disposer d'un workflow homogène – de la conception à la fabrication - la communication entre les équipements et logiciels de conception doit être efficace, ajoute Scott. Un passage facile du logiciel de conception à la machine de fabrication additive est particulièrement important quand il s'agit de produire des implants rachidiens car les étapes intermédiaires et les transferts d'informations peuvent être une source d'erreurs et d'incohérences.
Solution
Renishaw, IMR et nTopology ont uni leurs forces pour produire, par fabrication additive, des implants à structures lattices pour le rachis cervical. Le nom du projet pour ce type d'implant était ACID, Anterior, Cervical, Interbody Device (en français : Dispositif intersomatique cervical antérieur).
Pour commencer, IMR a créé une enveloppe de conception pour identifier les opportunités inédites que présente la fabrication additive dans l'amélioration des résultats chez les patients. nTopology a ensuite fourni le logiciel pour concevoir la géométrie complexe des implants rachidiens, et Renishaw la machine RenAM 500M servant à fabriquer les implants par fabrication additive.
IMR a réalisé d'importantes recherches pour identifier, d'une part, les dimensions convenant au cas spécifié et, d’autre part, les conditions de charge auxquelles les implants doivent résister non seulement au quotidien mais aussi dans des situations extrêmes comme la course ou le saut. Ces données ont été combinées aux propriétés matières connues de l'os chez les patients atteints de pathologies nécessitant un implant rachidien. Les trois sociétés ont par la suite collaboré pour concevoir les caractéristiques mécaniques principales du dispositif. Ces caractéristiques dépendant en grande partie de la géométrie des cellules individuelles utilisées dans la structure lattice car l'objectif est d'atteindre des propriétés proches de celles de l'os humain et d'optimiser la lattice poreuse pour l'ostéo-intégration.
Une fois les paramètres de conception des implants décidés, IMR a généré les fichiers de conception sur la plate-forme nTop. nTopology et Renishaw ont collaboré étroitement pour faire en sorte que leurs produits soient compatibles pour transférer sans problème un modèle de la plate-forme nTop à la RenAM 500M.
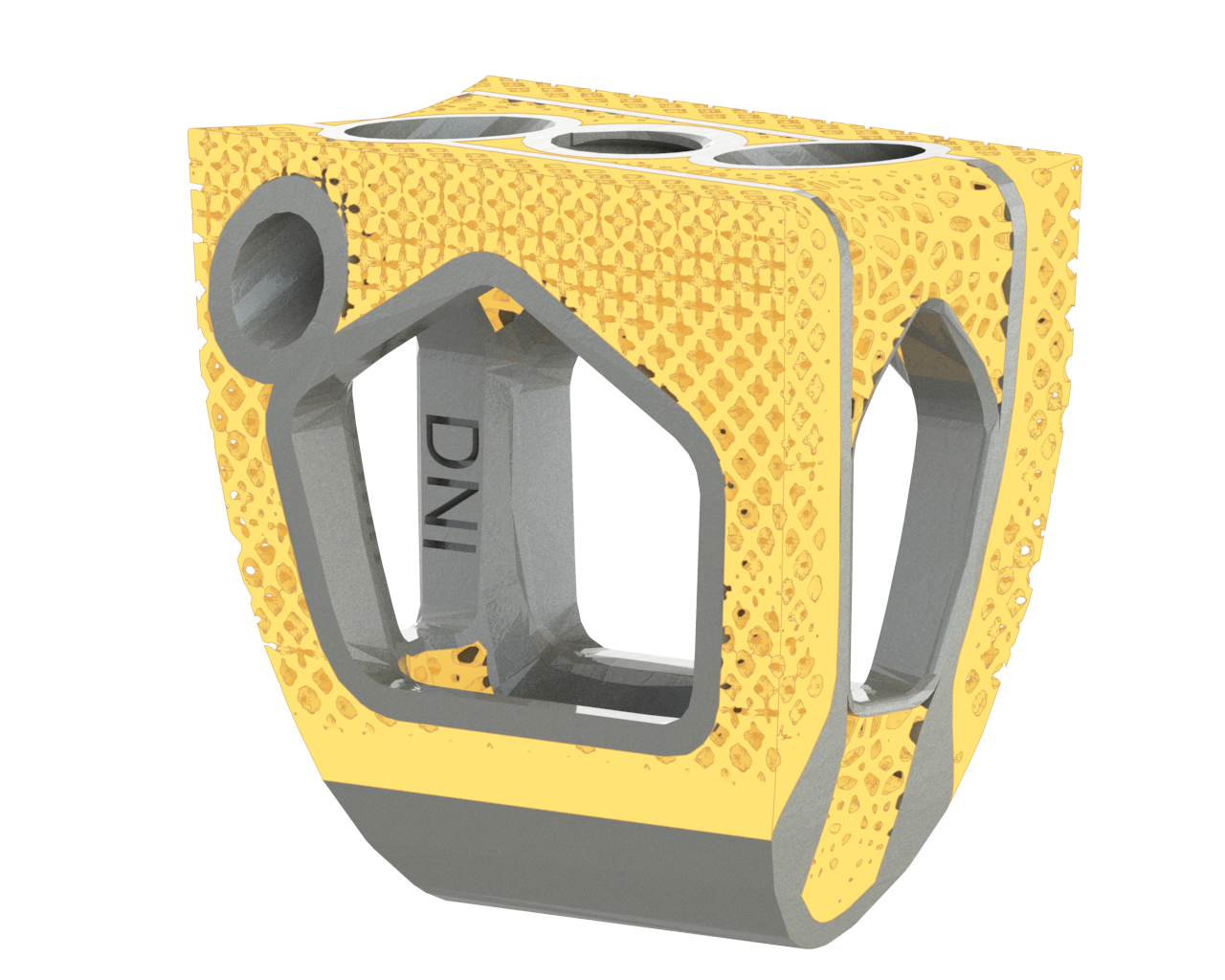
L'entreprise a réalisé une série de tests pour démontrer que le dispositif répondait aux critères les plus pertinents des spécifications énoncées par la FDA. Les propriétés chimiques ont été testées pour garantir la conformité à la norme ASTM F136, spécification standard au titane forgé de grade 23 employé dans les implants orthopédiques, et à la norme ASTM F3302 spécification standard de la fabrication additive en alliages de titane par fusion sur lit de poudre. Les propriétés mécaniques de la structure poreuse ont été caractérisées suivant la méthode d'essai (norme ISO 13314) qui vise à déterminer les propriétés compressives et le mode d'échec d'un matériau métallique poreux. Enfin, des tests ont confirmé la conformité aux normes ASTM 1104 et ASTM 1147, ces deux méthodes d'essai standard visant à démontrer que les structures poreuses ne se délaminent pas des faces solides du dispositif.
"Pour démontrer la faisabilité, nous avons construit des échantillons-témoins sur le plateau de production de la RenAM 500M et réalisé des essais destructifs sur ces échantillons, explique Sean McConnel, Ingénieur de recherche principal chez IMR. Nous avons fait cela pour confirmer les propriétés chimiques, métallurgiques et mécaniques des implants."
Résultats
Cette étude de faisabilité a démontré qu'on peut utiliser la fabrication additive pour produire des implants rachidiens avec des caractéristiques impossibles à obtenir par les méthodes de fabrication conventionnelles. La RenAM 500M a été utilisée pour fabriquer à la fois les prototypes et les implants définitifs. Il n'a donc pas été nécessaire de transférer la procédure entre des machines différentes. Pour les producteurs de dispositifs médicaux, cette simplification du workflow va se traduire par des économies considérables en terme de coûts et de temps.
"Il y a deux ans, la fabrication additive était totalement absente chez IMR, explique McConnell. Grâce au soutien que nous avons reçu de Renishaw dans le cadre des implants rachidiens ainsi que d'autres projets, nous avons accru les compétences de notre personnel et nous sommes désormais bien établi dans le domaine de la fabrication additive.
Nous avons pu transférer à nos clients le savoir-faire en fabrication additive que nous avons acquis chez Renishaw, ajoute McConnell. Nous travaillons avec des sociétés qui auparavant craignaient les risques liés au manque de connaissance sur la fabrication additive, mais celles-ci font désormais de plus en plus confiance à ces équipements.
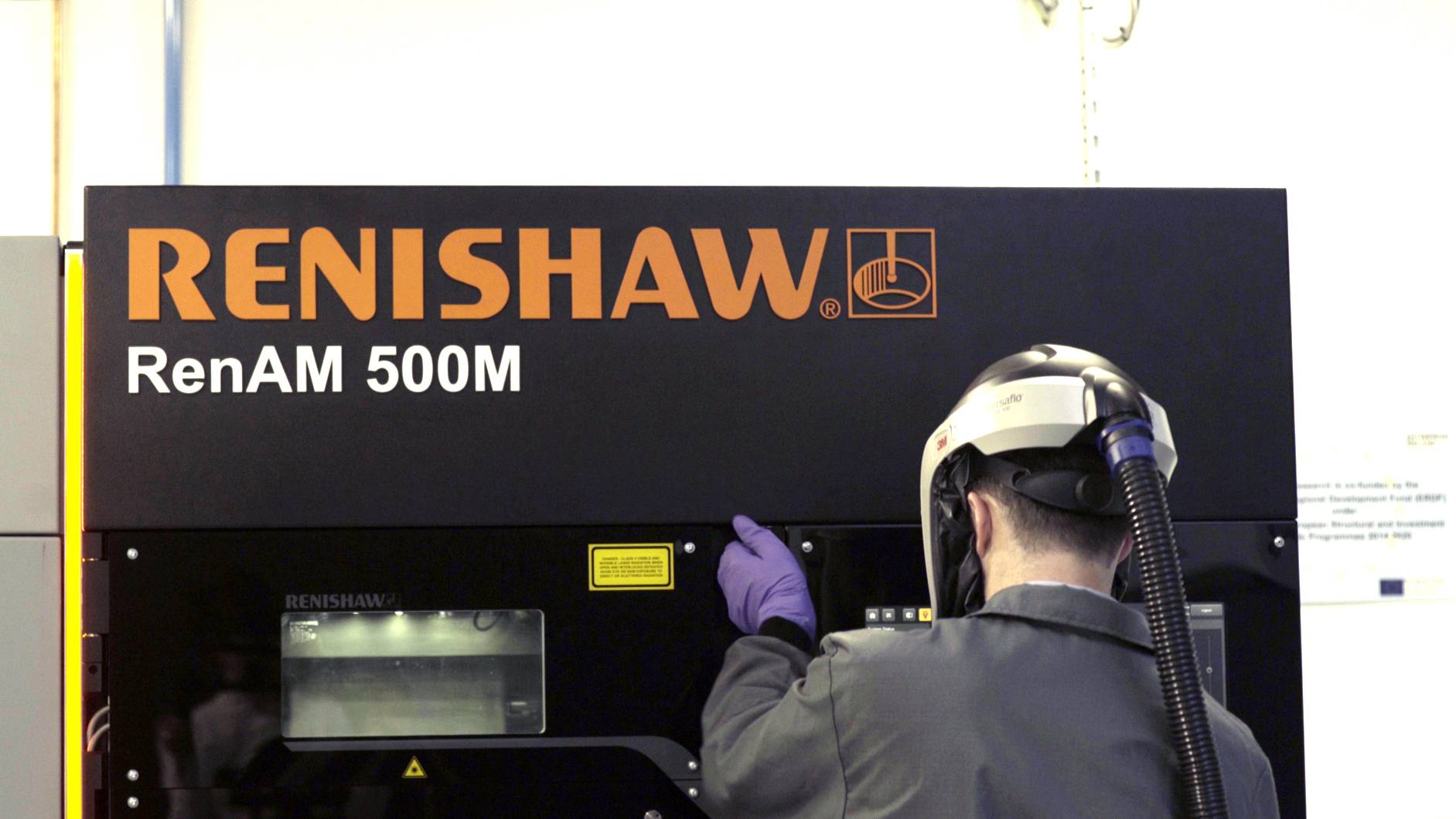
Avec nous, Renishaw a travaillé sans relâche à l'amélioration du processus de fabrication additive pour réaliser les implants rachidiens, poursuit-il. Ensemble nous avons conçu un ensemble d'expériences générant les paramètres optimaux pour le produit. Nous avons ainsi pu réduire d'un facteur de dix la part de post-traitement exigée sur les fonctionnalités principales."
"IMR joue un rôle majeur dans l'introduction de la technologie de fabrication avancée dans l'industrie irlandaise, explique Ed Littlewood, Responsable marketing de la division Produits médicaux et dentaires chez Renishaw. Dans cette entreprise, la rigueur des connaissances en matière de conception et de recherche a permis de produire des implants rachidiens représentatifs illustrant le potentiel de transformation que la fabrication additive peut avoir dans les soins de santé."
En plus de démontrer que la fabrication additive est capable de produire des implants rachidiens, cette étude montre que, en envisageant la conception pour fabrication additive (DfAM) aux premières étapes, on peut réduire le recours aux supports et de ce fait réduire les opérations de finition.
Le projet des implants rachidiens nous a permis d'acquérir notre propre connaissance de la production de dispositifs médicaux et des capacités des machines de fabrication additive, explique Scott. Nous avons donc pu mettre au point notre logiciel de conception pour qu'il puisse être utilisé afin d'appliquer la technologie de fabrication avancée aux dispositifs médicaux.
De nombreux essais ont été nécessaires pour aligner le logiciel sur les critères de la machine RenAM 500M, ajoute Scott. Malgré cela, les ingénieurs Renishaw ont fait en sorte que tout ce processus soit aussi aisé qu'efficace. Les projets de ce type prennent habituellement des années mais l'excellente collaboration entre nTopology, Renishaw et IMR a permis de boucler l'étude en quelques mois.
Nous allons poursuivre notre étroite collaboration avec Renishaw pour faire en sorte que les entreprises puissent accéder à la technologie de fabrication additive. Notre souhait est d'élargir la collaboration dans l'industrie de la fabrication avancée, conclut Scott.