Cette page n'est pas disponible actuellement dans votre langue. Vous pouvez en afficher une traduction automatique avec l'outil Google Translate. Cependant nous déclinons toute responsabilité quant à ce service et nous ne contrôlons pas les résultats de la traduction.
Pour en savoir plus à ce sujet, contactez-nous.
Race to innovate: digital position feedback for Land Rover BAR's America's Cup boat
Renishaw, the global engineering company, is part of Land Rover BAR's Technical Innovation Group. The aim of this group is to bring together the best of British engineering to help win the America's Cup and bring it home. This is a big challenge unlike any other in world sailing.
America's Cup Class (ACC) racing yachts use an innovative type of sail called a sail-wing. This operates like the wing of an aeroplane and produces ‘lift' which drives the vessel forwards. The wing used by the Land Rover BAR race-yacht ‘Rita' (code-name: R1) has a sail area of 103 m2 and is 23.5 m high, which is comparable to the main wings of an A320 aircraft. Clearly, there are many difficult engineering challenges involved in designing and building a huge functional wing with numerous moving parts, whilst ensuring sufficient strength and minimal weight. The R1 is a state-of-the-art catamaran that literally flies above the water on a pair of hydrofoils. This type of foiling design has allowed the sport to reach spectacular new speeds.
On the R1, the control surfaces are all driven by hydraulic actuators. Hydraulic pressure is provided by the sweat and toil of the crew's ‘grinders', who turn specialised hand-cranks. When Land Rover BAR realised that control precision could be compromised by the somewhat convoluted load-path between actuator and control surface, they looked to measure the control surface movements directly and contacted Renishaw for help.
Technical Leader Dr. Finlay Evans and his team designed a special position sensor (encoder) for the wing flap control surfaces, which allowed much better direct feedback to be achieved. This allows the helmsman and crew to race the boat with more precision whilst enabling the capture of high-quality performance data during development and training.
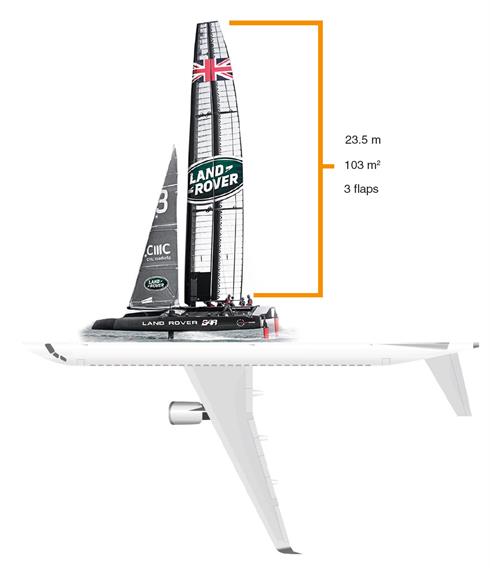
Dr. Evans explains more
What is your background at Renishaw?
I'm a Technical Leader and I've been at Renishaw for 17 years. My background is in dynamics – mechanical engineering. A lot of my previous work has been in R&D – looking at new ideas and new technologies, which is one of the things that attracted me to this project.
What does Renishaw represent to you?
Renishaw is unique - with its forty-year history and position as one of the UK's leading engineering firms. It's a great place to work, frankly, and represents cutting-edge design and manufacturing, which is why Land Rover BAR have confidence in our ability to deliver.
Where are encoders found on the R1 race-yacht and what role do they play?
The encoders are on the main wing, and there are four of them: one at the top, two on the main body of the wing and one at the bottom. A fifth encoder is mounted on the hull at the bottom of the mast. The wing encoders measure the wing flap twist from top to bottom and the one on the mast determines the angle-of-attack of the whole wing assembly. In addition to that, there are two down in the hull for measuring the positions of the port and starboard rudders. Now, these boats can go up to 60 mph or so, which creates a lot of high-impact spray. Saltwater conditions and regular contact with seawater wash necessitate robust sealing of the encoder sensor and electronics – particularly for those closest to the water line.
Could you describe how the flaps on the wing-sail work?
A traditional sail is a curved sheet of material with a mast that the air flows around. The wing is much more like the aerofoil of an aeroplane where you have a flap that pivots in either direction depending on the wind angle relative to your intended direction. To actuate these flaps, there are three main ones, flap control plates called hammerheads are pulled left and right by internal control lines. As far as the encoder goes, a partial-arc scale is mounted on the moving flap part whereas the sensor head is mounted within the wing rib. Down at the rudder, we've taken the same technology – the same building blocks – that we've created and used a similar arrangement.
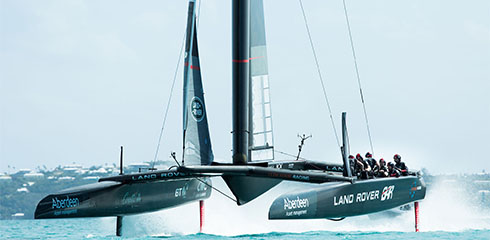
Why put position encoders on the control surfaces?
Actuators are already used to move these control surfaces, but these actuators are not necessarily located in the same place as the control surfaces and ropes (lines) are used to transfer the actuation forces. Position measurements were initially just made on the actuators, far removed, with lots of compliance between the actuator mechanism and the control surface.
By using encoders directly on the control surface, or as near as possible, you get a much more accurate reading of the angular position of the control surface.
The encoders installed on a hammerhead (flap control plate)
Why did you choose magnetic encoders instead of optical?
Conditions at sea are quite extreme as far as precision encoders are concerned. We had the option of either optical or magnetic technology. Now, consider the implications of high-speed winds and salt spray going everywhere – open optical encoders would be a real challenge because you must keep the optical path clear. Magnetic encoders, therefore, were the only viable alternative. These encoders can be fully sealed giving much greater contamination resistance, which is essential for this application. Protecting against the harsh environment was one of the main reasons for our choice. Other reasons were space limitations surrounding the highly loaded wing ribs. By using LinACE™ modules from our associate company RLS, we could design a new encoder that minimised the size of hole needed within the wing rib. We satisfied 3 major technical constraints by designing an encapsulated encoder: reduced size, environmentally sealed and an integrated sliding bearing for maintaining position on the partial-arc encoder plate.
How do magnetic encoders work?
In this case, a magnet is attached to the back of a Hall sensor array and is used in conjunction with a ferromagnetic scale, which has a series of lines (grooves) etched into it. The grooves in the scale surface produce changes to the local magnetic field, such that when the sensor is moved over the scale, a moving magnetic pattern is detected by the Hall sensors, which is then converted into a position measurement. Because the pattern of the scale grooves is non-repeating, the absolute position can be determined anywhere on the scale. The sensor head assembly is completely encapsulated to protect its sensitive microelectronics from the elements. The outer polymer layer also gives a sacrificial surface on to which the scale makes full contact, which ensures correct ride height. Magnetic encoders are unaffected by encapsulation.
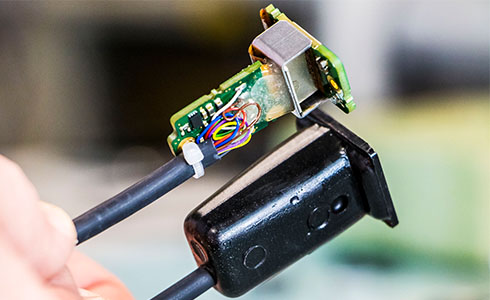
The design process was based primarily around the requirements of the encoder. Up on the wing, a small amount of mass at the top makes a big difference to the performance and stability of the boat. Space was a prime consideration – the space restriction came about because the actuation surfaces are in small spaces with small clearances. At the same time, this wing is approx. 24 m high and is designed to twist by varying amounts at different heights for aerodynamic reasons. What we must contend with is the fact that when the scale plate on the hammerhead moves around, it rotates out-of-plane as well due to the twist of the wing.
Our traditional encoders are designed to run with moderately small ride-heights on good linear or rotary axes. Here we have a tight requirement in terms of measurement accuracy along an arc that is not just moving axially but also twisting as it rotates. We had to come up with a way of maintaining the measurement accuracy throughout the out-of-plane twisting and pitching. Magnetic sensors are arguably the best technology to use in terms of contamination resistance, although ride height tolerance is very tight compared with typical bearing movements in a boat and wing of this size.
Understanding Land Rover BAR's requirements was the most important aspect, but given the time restriction, we had to select technology from building blocks that we already had from pre-existing commercial encoders. Space and geometry requirements in the wing were significant factors in determining the design. Each part was a real challenge; we started with a module that exists for a linear encoder for use on a precision plated shaft with carefully shaped grooves embedded under the surface. We had to effectively unwrap that code and embed it into a flat surface with differently shaped grooves along an arc using a new process and hope that the resulting flat arc equivalent scale would work first time.
We took the pre-existing LinACE™ module from our RLS associate company, and repackaged it into a waterproof encapsulation, which we hadn't done before, to allow it to survive the operating environment. This also provided an encoder body which was small enough to operate within the tight dimensional constraints of the highly stressed wing ribs. We also had to come up with a solution that allowed the scale part to twist and move but without inducing significant errors when the sensor moved.
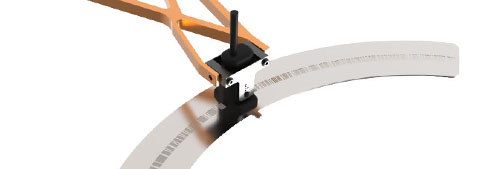
What was your solution?
We had to come up with a gimbal arrangement for the sensor whereby the partial-arc scale can twist out of its plane of rotation without inducing inaccuracy. A special aluminium wishbone and yoke assembly was designed to hold the readhead with high precision while allowing for pitch and roll. The wishbone is attached to the wing's static structure. This whole encoder assembly gives a much more accurate reading of the position of each flap than inferring from actuator movements.
What was the biggest challenge and what are you most proud of?
All of these design features [a new scale manufacturing process, encapsulating a plastic encoder housing, a gimballed support, sliding bearing and weather resistance] together were crucial to the success of the overall encoder system. Any failure in these areas would have meant failure to deliver an encoder in the time scale requested. These building blocks were all separate mini-projects in their own right and ensuring each was successful first time was the biggest challenge. Finding a way to bring all of these elements together successfully within the short timescales involved a rapid response from both our RLS colleagues in Slovenia and our own in-house manufacturing facilities. I'm proud of what we achieved.
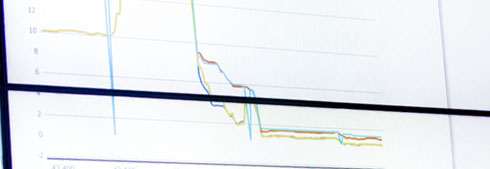
How is the position feedback used?
Position feedback from the encoders is used in real-time on the boat by the wing trimmer, but also a lot of analysis is done and that is where general efficiencies and accuracies are improved.