Les solutions de refroidissement conforme Renishaw donnent de l’élan à la productivité du moulage
Contexte
Les nettoyeurs à haute pression de Alfred Kärcher GmbH & Co. KG, dotés de leur inimitable boîtier jaune vif, sont devenus un équipement incontournable de nombreux foyers allemands et leur popularité s’élargit à l'échelle internationale. La puissance et la fiabilité des appareils encouragent les utilisateurs à se servir de leur « Kärcher » dans leur routine de nettoyage quotidien, tant à l'intérieur qu’à l'extérieur de la maison.
Pour répondre à la demande croissante provenant de partout dans le monde, Kärcher produit ses nettoyeurs compacts par millions chaque année. Rien que plus de deux millions de nettoyeurs à haute pression K2 standard quittent l'usine d’Obersontheim chaque année. Toutefois, même ce niveau de production n’est pas en mesure de répondre à la demande mondiale.
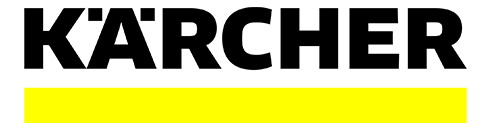
Défi
L'une des caractéristiques les plus reconnaissables des nettoyeurs Kärcher est leur boîtier jaune vif. Il constituait aussi l'un des principaux goulets d'étranglement dans le processus de fabrication. Par exemple, les boîtiers des nettoyeurs de la série K2 sont produits sur six machines de moulage par injection, chacune capable de mouler 1 496 boîtiers par jour. Ce n'était pas suffisant pour Kärcher, qui dispose de quatre lignes d'assemblage, fonctionnant avec trois équipes par jour, pour donner une capacité de production de 12 000 nettoyeurs à haute pression K2 assemblés et emballés chaque jour.
De toute évidence, une solution consisterait à ajouter plus de machines de moulage. Toutefois, Leopold Hoffer, coordonnateur pour le moulage par injection à l'usine Kärcher d’Obersontheim, a estimé qu'il devait être possible d'obtenir une meilleure productivité à partir de l'équipement existant. « Notre objectif était de réduire le temps de cycle des 52 secondes d'origine à entre 40 et 42 secondes » explique-t-il. Il s'est rapproché de la société LBC Engineering basé à Pliezhausen, acquise par Renishaw GmbH en mai 2013, afin d'œuvrer à l'amélioration du temps de refroidissement dans les moules.
Les résultats furent meilleurs qu’escomptés. Renishaw nous a vendu un ensemble complet d'amélioration, avec une approche holistique et une analyse du moule utilisé afin d'obtenir les meilleurs résultats.
Kärcher (Allemagne)
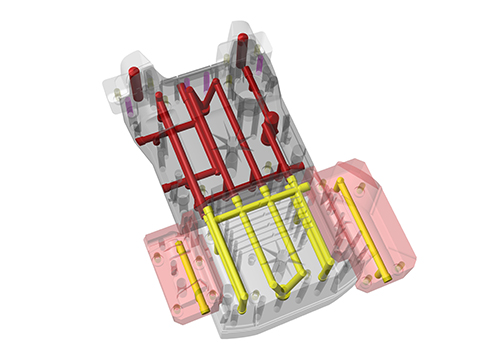
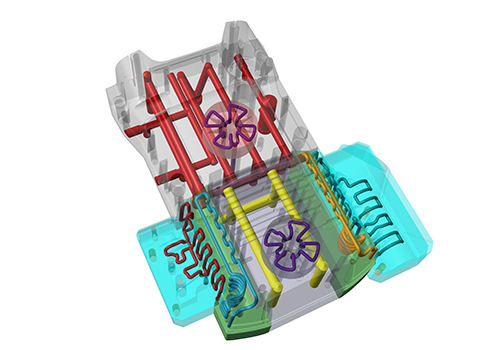
Solution
« La première étape du projet consistait à obtenir des données pour les moules existants afin de déterminer si l'objectif de Kärcher était réaliste » se souvient Carlo Hüsken, ayant coordonné le projet pour Renishaw. Le processus de moulage par injection existant était mappé avec des images thermographiques fournies par Kärcher et simulées à l'aide du logiciel de simulation Cadmould® 3D-F. Cette étude a révélé que, sur les 52 secondes du temps de cycle, le refroidissement prenait 22 secondes, avec une fonte à 220 °C et un démoulage à 100°C. La température de l’outil de moulage était contrôlée par de l'eau à une température de 35°C et un débit de 10 litres par minute. Les points chauds, détectés par la thermographie, ont aussi été modélisés, car ces zones étaient responsables de l'allongement du temps de cycle et nécessitaient d'être analysées plus en détail. Avec ces données, une simulation sur 20 cycles a été effectuée, comprenant une analyse de la température de la paroi.
Sur une suggestion de Monsieur Hüsken, la commande de température côté buse a été améliorée pour le second cycle de simulation. Le cuivre au béryllium, partie bombée du raccord fileté, pour le couvercle du corps s’est doté d’un refroidissement supplémentaire en insérant deux canaux de refroidissement classiques dans la plaque de moulage sur le côté buse.
Deux simulations ont alors été exécutées pour évaluer le potentiel d’amélioration grâce à l'utilisation d’un refroidissement conforme. Le refroidissement de moule classique est constitué d'un réseau de canaux percés. Le perçage des canaux limite les géométries qui peuvent être produites. Ainsi, alors qu’il est adéquat pour les moules simples, il ne peut pas fournir le refroidissement le plus efficace dans des exemples plus complexes. Le refroidissement conforme est basé sur l'utilisation de la fabrication additive métallique pour produire le noyau du moule. La fabrication additive construit les noyaux en une série de couches minces. La souplesse de cette approche signifie que des canaux de refroidissement d’une complexité presque illimitée peuvent être incorporés. Généralement, le refroidissement conforme est utilisé pour garder les canaux plus à égale distance du moulage, procurant un refroidissement plus homogène, ou pour se concentrer sur des zones où les points chauds sont connus afin de permettre un refroidissement plus rapide dans ces zones.
Les simulations ont montré que pratiquement toutes les zones de points chauds pouvaient être améliorées par le biais du refroidissement conforme, avec des températures de paroi réduites jusqu'à 70°C.
Enfin, dans l’une de ces zones où l’espace était insuffisant dans le moule pour ajouter des refroidissements conformes, Kärcher a introduit des améliorations brillantes à la conception du produit afin d’atténuer le problème.
En fonction des résultats des simulations, Renishaw a présenté un projet d'amélioration complet à Kärcher. Celui-ci a montré que le refroidissement conforme pouvait être utilisé pour améliorer la commande de la température des points chauds du moule, permettant ainsi d'atteindre un taux de refroidissement plus uniforme et un temps de refroidissement réduit. Une conception de moule modifiée a été proposée permettant d'intégrer deux noyaux créés en fabrication additive, visant à fournir un refroidissement conforme aux points chauds identifiés.
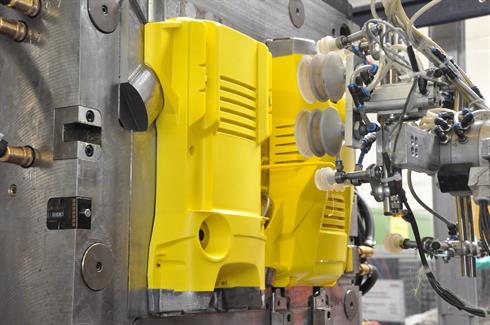
Résultats
Les résultats de la conception de moule modifiée ont été vérifiés par Renishaw, à l'aide des images thermographiques fournies. Celles-ci ont confirmé que les températures de paroi pouvaient être réduites de 40°C à 70°C. Le temps de refroidissement a été ramené de 22 à 10 secondes, soit une réduction de 55%. Volker Neu, leader du groupe Technologie et Matières plastiques chez Kärcher, a avancé des chiffres confirmant que la nouvelle conception du moule, combinée avec la restructuration de certains composants périphériques (alimentation des matériaux, systèmes de manutention, etc.), a permis de réduire le temps de cycle de 52 secondes à 37 secondes. De ce fait, la capacité quotidienne sur une machine pouvait être augmentée, passant de 1 496 à 2 101 pièces moulées.
Kärcher a ensuite mis en œuvre les changements de conception pour les autres moules. Les inserts hybrides en fabrication additive pour ces moules ont été produits et fournis par Renishaw, avec l’assistance active de Monsieur Hüsken auprès du fabricant de moule durant la fabrication de l'outillage.
Après avoir été sceptique concernant le projet au départ, Monsieur Hoffer nous confie : « à la fin de la journée, les résultats furent meilleurs qu’escomptés. Renishaw nous a vendu un ensemble complet d'amélioration, avec une approche holistique et une analyse du moule utilisé afin d'obtenir les meilleurs résultats. »
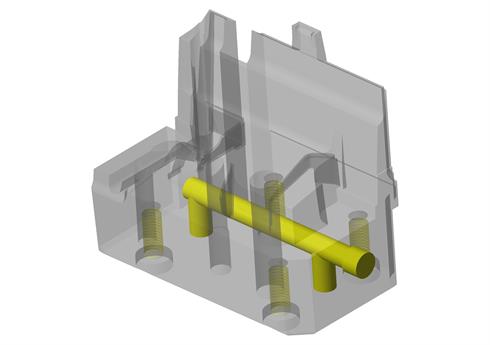
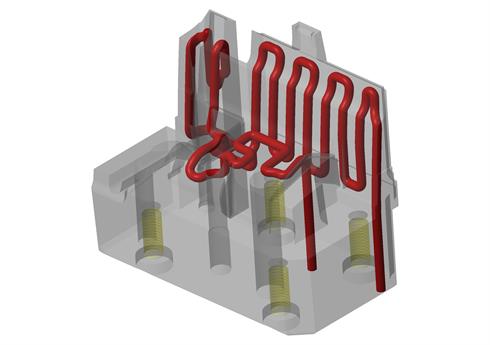
Renishaw fonde toujours ses solutions spécifiques à chaque client sur une combinaison technologique. « Dans notre cas, cela a signifié un mélange de techniques de refroidissement classiques, des noyaux spécifiques au projet, produits à l'aide de la fabrication additive, et des noyaux brasés sous vide » ajoute-t-il. « À partir de ces ingrédients, nous avons créé la bonne recette pour l'application. »
Avec ce projet, Monsieur Hoffer a amassé une expérience et un important savoir-faire. « À l'avenir, nous accorderons plus d'attention au refroidissement dans la phase de conception » a-t-il déclaré. « Les calculs de refroidissement seront une étape essentielle de chaque conception de moules chez Kärcher. À l’aide de cette information, nous pouvons alors prendre la décision de travailler avec des solutions de refroidissement classique ou de refroidissement conforme. »
« L’assistance de Renishaw a été excellente. Pour ce projet, Renishaw s’est avéré le bon choix et la société sera également notre partenaire clé lorsque nous devrons transformer la commande de température en matériau léger à l'avenir » conclut Monsieur Hoffer.
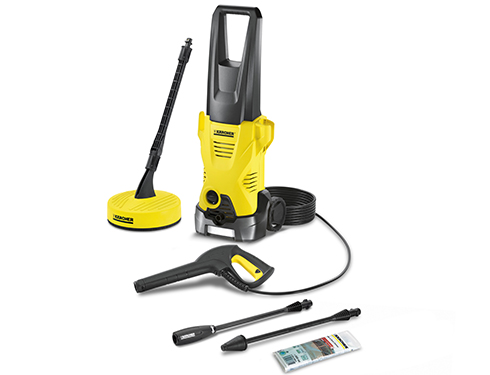
Images : Crédit Alfred Kärcher GmbH & Co.KG et Mr Gogoll