Inspection d’aubes de turbine 50 % plus rapide
Chez Europea Microfusioni Aerospaziali, fabricant d'aubes de turbine, basé à Morra De Sanctis près d'Avellino, en Italie, ces contrôles sont désormais réalisés au moyen d'une tête de palpage à 5 axes PH20 de Renishaw. Par comparaison avec l'utilisation d'un système à 3 axes, les temps de cycle ont été réduits de jusqu'à 50 % par rapport au contrôle précédemment fait avec un système de palpage 3 axes.
Contexte
Europea Microfusioni Aerospaziali (EMA) fait partie du groupe Rolls-Royce, leader mondial dans la fabrication de systèmes de propulsion pour avions civils et militaires, navires, sous-marins et turbines pour la production énergétique industrielle.
Les installations d'Europea Microfusioni Aerospaziali à Morra De Sanctis incluent une usine de 20 000 m2 qui fabrique des aubes de stator et de rotor à ultra-haute précision en alliages spéciaux pour des turbines aéronautiques installées dans les parties haute, intermédiaire et basse pression, d'applications civiles et militaires. La société fabrique également des aubes pour les turbines utilisées dans la génération d'électricité.
Plus des deux tiers de la production d'EMA sont destinés à des clients prestigieux dans le secteur aéronautique en Italie et dans le monde entier, notamment la société mère Rolls-Royce, AgustaWestland, Ansaldo Energia, Avio, Turbocare, Siemens et MAN. Environ 25 % des avions militaires produits dans le monde sont équipés de moteurs Rolls-Royce, dont beaucoup utilisent des produits EMA.
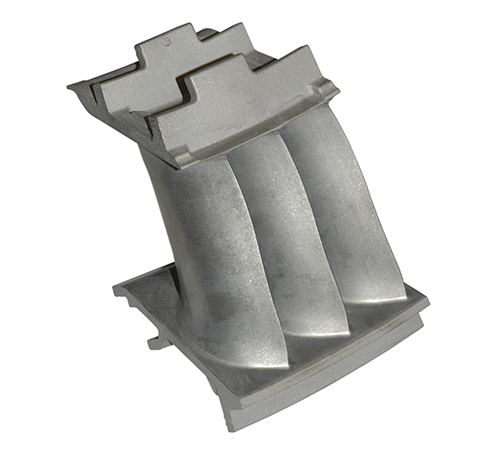
Depuis la mise en place de la tête de palpage PH20 de Renishaw, nous avons pu réduire significativement les temps de mesure et le nombre de changements de stylet réalisés pendant le cycle de contrôle. L'utilisation du logiciel MODUS™ nous a également permis de réduire et d'optimiser les temps de programmation. Nous avons fait en sorte de réduire les temps de cycle de 30 à 50 %, voire plus dans certains cas.
Europea Microfusioni Aerospaziali (Italie)
Défi
Les aubes de turbine et de moteur d'avion sont fabriquées à l'aide de super-alliages capables de résister à des températures et à des pressions très élevées. Leurs formes sont généralement complexes pour maximiser leur rendement, réduire les contraintes et la fatigue. Et pourtant, elles sont fabriquées en utilisant l'une des plus anciennes techniques de fabrication connues des hommes : le moulage.
EMA a perfectionné un large éventail de technologies de micro-moulage, en particulier celles utilisées pour la production d'aubes, constituées de monocristaux d'alliage métalliques. La société se spécialise également dans le procédé de micro-moulage à cire perdue, qui commence par la création de modèles en cire obtenus à partir de moules métalliques.
Ces modèles en cire sont ensuite enduits d'un matériau céramique conçu pour résister aux hautes températures. La cire est ensuite retirée et la carapace céramique forme le moule du super-alliage. Après solidification et refroidissement, les pièces moulées sont soumises à un traitement thermique et à une finition. Tous les composants font l'objet d'un contrôle dimensionnel et d'intégrité matière par ultrasons, rayons X et tests d'étanchéité matière.
La conception d'un procédé efficace pour le contrôle dimensionnel des aubes de turbine et de moteur d'avion est un défi compte tenu de la géométrie complexe des pièces et de la nécessité de contrôler chacune des aubes.
Solution
Vittorio Caggiano, ingénieur responsable du Contrôle qualité : « Nous devions trouver une solution nous permettant d’améliorer le processus du contrôle dimensionnel en termes de nombre de pièces mesurées par unité de temps. »
Pour cela, la société pouvait décider d’investir dans une nouvelle machine à mesurer ou de réduire le temps de cycle de la mesure, de manière à augmenter la capacité de ses machines existantes.
« Jusqu’à il y a quelques années, nos MMT travaillaient avec des têtes indexables 3 axes PH10, qui étaient limitées en indexation, temps de cycles et changement de stylets », déclare Caggiano. Ces limitations étaient dues à la complexité des pièces, qui demandaient de nombreux changements de stylet pour chaque cycle de mesure.
« Nous avons travaillé en étroite collaboration » avec les techniciens de Renishaw pour trouver une meilleure solution. Nous avons également envoyé nos pièces à Renishaw Italie, situé à Turin, pour des essais de mesure. À la suite de ces essais, nous en avons conclu que la meilleure solution était d’investir dans de nouvelles têtes de palpage 5 axes, PH20, plus flexibles et plus efficaces, ainsi que dans le nouveau logiciel de métrologie MODUS. Renishaw a installé en rétrofit les nouveaux palpeurs sur nos MMT existantes et a créé cinquante programmes de mesure, écrit sur site par l’équipe technique de Renishaw SpA pendant notre formation. »
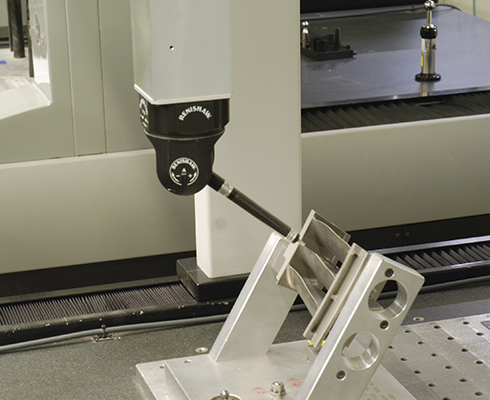
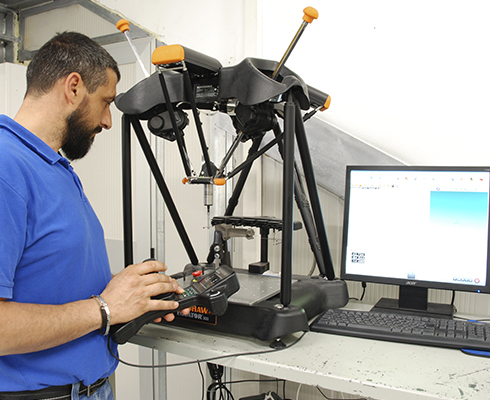
Résultats
« Le résultat final est extrêmement satisfaisant », ajoute Maurizio Rullo, programmateur MMT. « Depuis la mise en place de la tête de palpage PH20 de Renishaw, nous avons pu réduire significativement les temps de mesure et le nombre de changements de stylet réalisés pendant le cycle de contrôle. L’utilisation du logiciel MODUS nous a également permis de réduire et d’optimiser les temps de programmation. Nous avons fait en sorte de réduire les temps de cycle de 30 à 50 %, voire plus dans certains cas ! »
EMA a également investi dans un comparateur Equator™ Renishaw, qui lui permet de contrôler rapidement et efficacement la géométrie et la forme de pièces en grandes séries.
« Grâce au comparateur Equator Renishaw, nous sommes capables de regrouper tous les contrôles nécessaires sur certains composants, qui étaient auparavant effectués à l’aide de plusieurs multicotes. En conséquence, nous avons réduit de manière significative les temps de contrôle des pièces produites en grandes séries », conclut M. Rullo.
PH20 et logiciel MODUS Renishaw
La PH20 utilise ses propres mouvements pour saisir des points en se déplaçant uniquement sur ses axes et non la structure de la MMT. En utilisant les axes de rotation motorisés de la tête, les points de la gamme de palpage sont pris beaucoup plus rapidement tout en étant plus précis et répétables. En outre, le mouvement 5 axes supprime le temps que prenait l’indexation de la tête.
Le positionnement infini de la PH20 garantie un accès optimisé aux différentes entités tout en minimisant les changements de stylets. Les mouvements simultanés sur 5 axes permettent de mesurer des pièces plus grandes sur la MMT en minimisant, autour de la pièce, l’espace aux rotations de la tête. La PH20 s’aligne automatiquement sur le système de coordonnées de la pièce, ce qui évite les collisions de stylet et le recours à des montages précis.
Élaborée pour la PH20, la technique inédite de « calibration déductive » détermine l’orientation de la tête et la position du palpeur en une seule opération et permet ainsi de mesurer à partir de n’importe quel angle.
La PH20 est capable de s’aligner automatiquement avec le système de coordonnées de travail : cela évite les collisions et élimine la nécessité d’avoir recours à des montages complexes.
Le système exclusif de calibration rapide détermine l’orientation de l’ensemble de palpage en une seule opération et rend possible la prise de mesure depuis n’importe quel angle.
Grâce au logiciel de métrologie MODUS, les mesures complexes et la programmation de cycles de mesure ont été simplifiées. Le logiciel permet de développer hors ligne des programmes avancés directement à partir de la CAO, avec simulation, détection de collision et fonctions de contrôle du parcours palpeur sur écran. Cela permet de minimiser les temps d’indisponibilité de la machine ; les programmes, prêts à être exécutés, arrivent sur la machine et les temps d’essai sont réduits au minimum ou sont totalement éliminés.
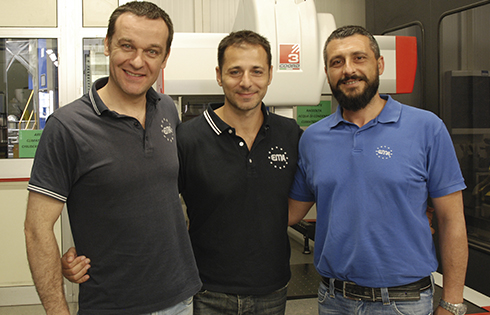
Contenu tiré de l’histoire originale d’Ernesto Imperio (Tecnologie Meccaniche)