Tato stránka není v současné době k dispozici ve vašem jazyce. Automatizovaný překlad můžete zobrazit pomocí nástroje Google Translate. Neodpovídáme za poskytování této služby a výsledky překladu jsme nekontrolovali.
Potřebujete-li další pomoc, kontaktujte nás.
Reliable positioning without a reference run improves process reliability
Renishaw's RESOLUTE encoder is an innovative, true-absolute measuring system that guarantees maximum process reliability for precision assembly systems used in the micro-electronics and micro-optics industries.
Process reliability is one of the principal factors governing the economic operation of high-value micro assembly machines that produce miniature electronic and optical components. Amicra Mikrotechnologie GmbH has achieved major improvements with Renishaw's future-oriented absolute measuring system, RESOLUTE, which allow Micro Assembly Cells to be commissioned more quickly and, in particular, independently of the operator's vigilance. This is particularly important for micro-electronics and micro-optics applications in the automotive sector, telecommunications and IT industries.
The components to be bonded and mounted, such as active / passive semi-conductors, lenses, MEMS, and processors, are picked up with the aid of linear axes and special grippers from feed stations. The components are then positioned on boards or wafers, where they are bonded with adhesives, soldered conventionally or soldered with a laser beam. Surface mounting on wafers and stack die technology make particular demands on mounting and production technology. Stack die technology is used to construct three-dimensional memory and computer structures; Semi-conductors are not only mounted horizontally next to each other and connected (SoC), but also vertically in several planes (TSV). Further miniaturisation is achieved as a result of a higher packing density.
Amicra Mikrotechnologie GmbH in Regensburg, Germany, develops and manufactures Micro Assembly Cells designed for this purpose. These machines are known in particular for their high levels of accuracy and reliability. Depending on the model, they will mount micro-components with an accuracy of up to ±0.5 µm, achieving a process capability Cpk of 1.66.
The NovaPlus series from Amicra has been designed for maximum productivity. Using a large array of horizontal and vertical linear axes, they surface mount wafers with practically no unproductive downtime. While a component is being positioned, a second handling unit is already picking up the next component from a buffer store. At the same time, the work tables and other linear axes with lasers and UV lamps move to the positions required for the soldering and bonding processes. In addition, other axes position the integrated process monitoring cameras.
Collisions absolutely ruled out
As Horst Lapsien, Managing Director of the Regensburg-based company, explained, the high process reliability of these installations is particularly instrumental in their economic operation. A crash between the alternate positioning grippers and linear axes must be avoided.
“This can be achieved through the extremely precise programming of the motions”, Horst Lapsien explained, “furthermore, the measuring systems on the linear axes have to detect the current position of the slides reliably and very precisely”. This could only be achieved to a limited extent with the incremental measuring systems used previously. “In the past, starting up the production and mounting cycle after a stoppage was unsatisfactory because the readheads of all the linear axes had to travel to a reference position first. Only in this way was the control system able to detect the actual position of the axes, but that took an unnecessarily long time”, added Horst Lapsien.
Also, starting from reference positions from an undefined position of the slides represented a significant source of error. If the operator has not analysed the crash paths first and selected the reference travel cycle accordingly, the installations can suffer considerable damage as the result of the collision of grippers or even of the gantries. As Horst Lapsien reported, this leads to unnecessarily long unproductive times, unnecessary costs and uneconomical downtimes of the entire machine in the event of a crash.
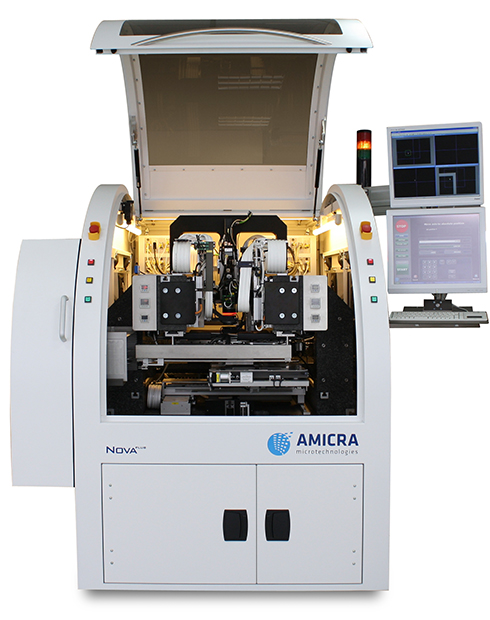
Absolute measurements without reference run
Thanks to Renishaw's RESOLUTE absolute encoders, Amicra's mechatronic engineers have been able to improve their machines considerably. The main advantage of these measuring systems according to Horst Lapsient is that they detect the absolute position immediately at switch-on, without a reference run. Consequently, the Micro Assembly Cells can start their automated cycle quicker, without relying on the operator's vigilance, after a stoppage or on commissioning for the first time. Process reliability is improved, unproductive times are reduced and expensive crashes are prevented.
Thomas Renner of Technical Sales at Renishaw GmbH explains further advantages of this absolute measuring system: “Compared with previous absolute measuring systems, RESOLUTE has a single track scale that combines both the absolute position and the embedded phase information into one single code. This means that RESOLUTE has very wide set-up tolerances and so it can be installed easily and continues to operate reliably over long-term use, even if the axes settle or move over time”. The RESOLUTE readhead also features a unique set-up LED for simple installation and commissioning, providing a simple visual check that the scale is being read correctly.
The RTLA absolute measuring scale can be bonded directly to the substrate or inserted into a special FASTRACK™ guide, both made from stainless steel. As a result, it easily installs compactly inside the Amicra machines, achieving ±5 µm/m accuracy. The tough stainless steel tape scale is highly resistant to damage, but if necessary, the FASTRACK guide allows easy scale replacement at any time.
RESOLUTE encoders feature a unique position detection method, analogous to a very high speed digital camera, capturing very high resolution images of the scale. These images are then analysed by a powerful Digital Signal Processor (DSP) that applies cross-checking and error-rejection, to determine position to 1 nm. Combined with a built-in position-checking algorithm, the encoder has high immunity to contamination. As confirmed by Horst Lapsien, since their introduction into three-shift production operation, his machines have recorded zero stoppages on account of reading errors of the measuring system caused by dirty measuring tapes.
The advanced detection technique also enables RESOLUTE absolute encoders to achieve high levels of accuracy with just ±40 nm cyclic error and jitter lower than 10 nm RMS. The result is excellent positional stability and a very low noise level. Therefore the Micro Assembly Cells equipped in this way benefit from higher levels of reliability and performance.
For Amicra, the RESOLUTE absolute encoder has yet another critical advantage; with its BiSS-C® open serial protocol, it can be easily integrated into many positioning axes. As Horst Lapsien explained, many industry-standard servo drives and controls now have this interface. Amicra can therefore avoid being tied to a single supplier of motion system components.
Summary of the optical encoder
RESOLUTE is a ground-breaking absolute encoder system for both linear and rotary applications, featuring 1 nm resolution at speeds up to 100 m/s (36 000 rpm), wide set-up tolerances and high dirt immunity. A range of pure serial protocols are available, including FANUC, Mitsubishi and Panasonic, for use in a wide range of applications including electronics assembly, flat panel display manufacturing, solar PV production, semiconductor processes, machine tools and precision motion control.
As with all Renishaw encoder products, RESOLUTE is backed by a comprehensive warranty and a responsive global support network of subsidiary staff. RESOLUTE is manufactured to a quality system certified to ISO9001 and the product is RoHS/WEEE compliant.
BiSS® is a registered trademark of iC-Haus.
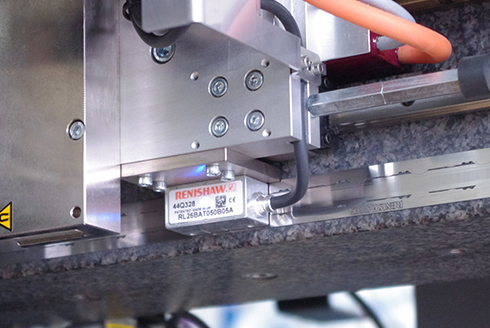