Open optical encoders for motion control
Renishaw provides an extensive range of open optical encoder systems. Learn how our absolute and incremental technology, along with a non-contact design, plays a key role in precision measurement manufacturing.
Find your Renishaw open optical encoders
Renishaw's open optical encoders provide robust and high-performance position measurement. A compact optoelectronic readhead senses motion relative to a scale with regularly-spaced markings.
Our selection of linear, partial arc and rotary encoders are suitable for a wide range of applications. Additionally, variants such as Functional Safety, Ultra-High Vacuum and Extended Temperature Range encoders are available.
To assist you in selecting an encoder, our comparison tables and encoder product configurator highlight the variety of compatible readheads and scales. You can also find details of the industries that benefit from optical encoders, with our wide range of case studies and application notes.
What form of motion do you need to measure?
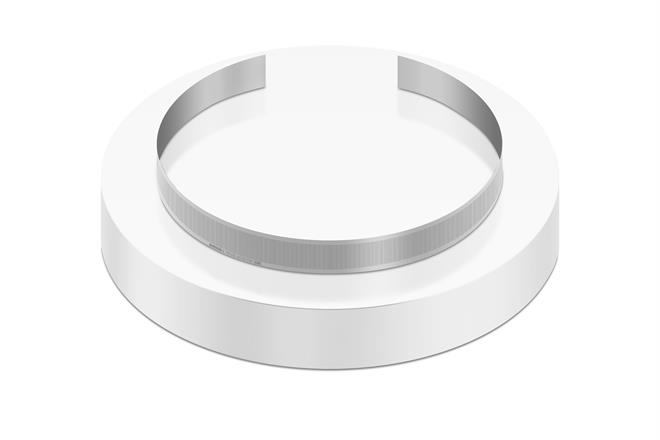
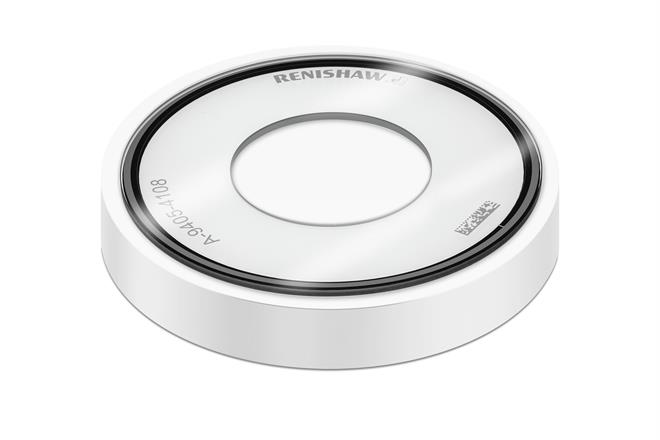
We were impressed by the capabilities of the RESOLUTE UHV encoder system, it fully meets our requirements including robust mechanical design, suitability for high-temperature bake-outs and resistance to radiation ageing. Renishaw's encoder really does the job.
IRELEC Alcen (France)
What is an open optical encoder?
Open encoders are exposed and feature no external integrated enclosure. The advantages of open optical encoders include the effective elimination of backlash, shaft wind-up (torsion) and other mechanical hysteresis errors.
A rotary open optical encoder consists of a position measurement readhead and an accurate rotary scale marked either on the periphery of a ring or on the face of a disc.
The readhead measures position by optically sensing the regularly-spaced scale markings. It then outputs this information as an analogue or digital signal.
The signal is subsequently converted into a position reading by a digital readout (DRO) or motion controller.
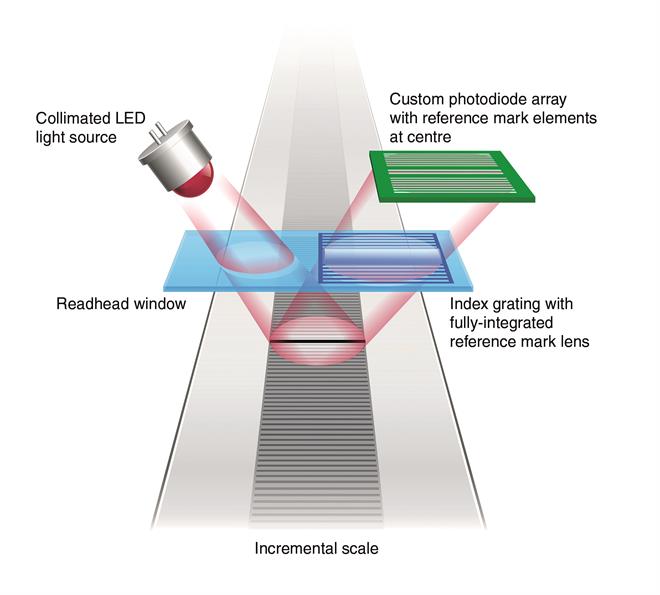
By understanding Renishaw's encoder technology, you will be able to compare our systems to determine what is right for your application.
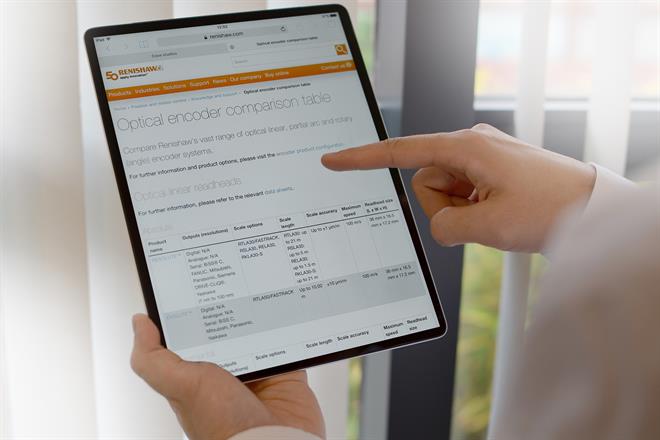
Compare Renishaw's vast range of absolute and incremental encoder systems, depending on your linear, partial arc or rotary requirements. Our tables detail output, accuracy, speed and size, and will guide you towards the most appropriate systems.
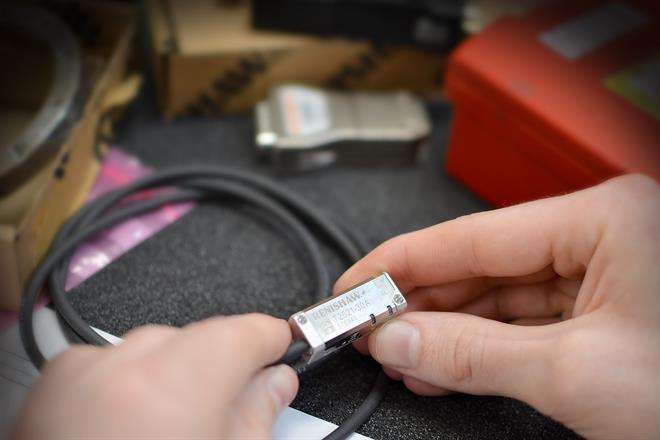
Build an encoder system and generate a part number with our encoder product configurator. With this information, easily send a request for a quote and determine the most relevant product for your requirements.
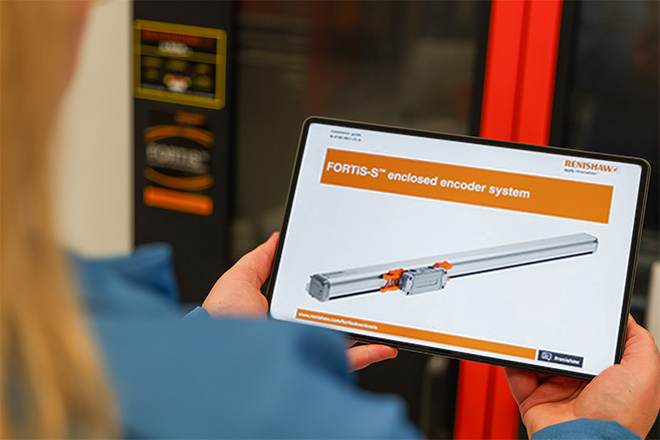
Find out the technical specifications for our optical encoder series, their options and variants, via our technical documents downloads. Our compliance certificates will give you an additional guarantee of Renishaw's commitment to quality.
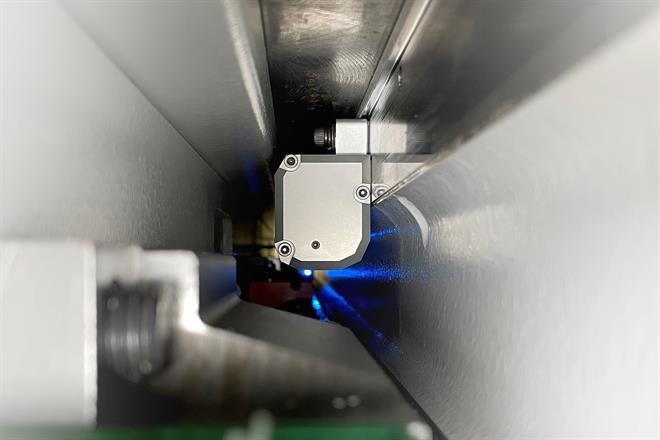
Discover which industries use optical encoders and how Renishaw's encoder technology and extensive expertise benefit manufacturers globally. See real-life examples of how customers have gained from Renishaw encoder systems.
How can we help you?
View the frequently asked questions for topics covering incremental and absolute encoder systems, scales, installation and sales support. We aim to help you understand the features and benefits of Renishaw encoder systems, and make selecting and installing our products easy.
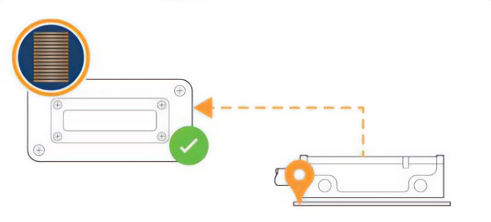
What does reliability mean to us?
Every encoder we design is built with reliability at its core, ensuring it is built to last. We put the product through tests that go far beyond normal operating conditions and prove the mechanical and design integrity of the product.
Renishaw maintains complete in-house production of all key manufacturing stages, including printed circuit board (PCB) assembly, machining, cable assembly, readhead assembly and readhead testing. This approach is extended to the production of scales, setting them apart from other encoder companies. By keeping these processes internal, the company ensures stringent quality control at every stage of product development.
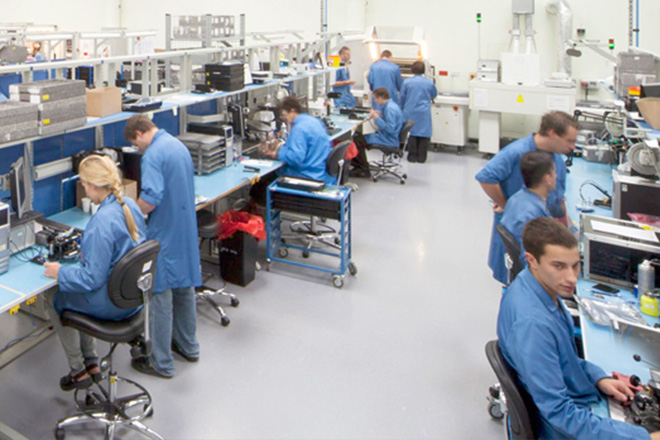
Upgrade your legacy Renishaw optical encoder systems
Some of our older, legacy products are either not recommended for new designs, are available on last-time-buy or are being made obsolete.
Renishaw is constantly developing new technology which means systems can be upgraded with an array of alternative high-performance Renishaw encoders.
Find our alternative solutions and contact us today for manufacturing support.
Contact our sales team today
Get in contact with your local office to find out more information and speak to an expert.